Статьи по неразрушающему контролю
Химический (спектральный) анализ стали – это качественное или количественное определение химических элементов, содержащихся в исследуемом образце. Исследование позволяет определить присутствие примесей и прогнозировать эксплуатационные характеристики готового изделия. По химическому составу стали делятся на углеродистые и легированные. Каждый тип в свою очередь включает подгруппы с низким, средним и высоким содержанием углерода и легирующих элементов. Помимо химического состава, стали группируют по назначению, качеству, структуре и другим характеристикам.
Наша аккредитованная лаборатория оказывает услуги по химическому анализу металлов и сплавов в диапазоне от углерода до урана (C6-U92), в том числе алюминиевых сплавов, нержавейки, титана золота и других драгоценных металлов, а также черных сталей, отличающихся только по углероду. Анализ проводится рентгенофлуоресцентным (РФА) и лазерно-искровым (ЛИЭС) спектрометром. Результаты анализа показывают долю каждого элемента и наиболее близкие по элементному составу марки стали. Проведение анализа возможно в нашей лаборатории или на территории заказчика. Цена выездного химического анализа в Москве начинается от 30 000 руб. Сдать металл на химанализ в нашу лабораторию можно по адресу г. Лобня, ул. Борисова д. 14 к2. Заявки на направляйте по адресу kontrol@ntcexpert.ru.
Дополнительные материалы:
- Статьи по спектральному анализу
- ГОСТ 22536.0-87 Сталь углеродистая и чугун нелегированный. Методы анализа
- ГОСТ Р 54153-2010. Сталь. Метод атомно-эмиссионного спектрального анализа.
- ГОСТ 12344-2003 Стали легированные и высоколегированные. Методы определения углерода
- ГОСТ 27809-95. Чугун и сталь. Метод спектрографического анализа.
- ГОСТ 27611-88. Чугун. Методы фотоэлектрического спектрального анализа.
- ГОСТ 9717.1-82. Медь. Методы спектрального анализа.
- ГОСТ 9716.2-79. Сплавы медно-цинковые. Метод спектрального анализа по металлическим стандартным образцам
- ГОСТ 6012-98. Никель. Методы химико-атомно-эмиссионного спектрального анализа.
- ГОСТ 15483.10-2004. Олово. Методы атомно-эмиссионного спектрального анализа.
- ГОСТ 8857-77. Свинец. Метод спектрального анализа.
- ГОСТ 17261-77. Цинк. Спектральный метод анализа.
- ГОСТ 23328-95. Сплавы цинковые. Методы спектрального анализа.
- ГОСТ 23902-79. Сплавы титановые. Методы спектрального анализа.
- ГОСТ 3221-85. Алюминий первичный. Методы спектрального анализа.
Смотрите также разделы: Измерение ферритной фазы, Металлография, Измерение твердости, Спектральный анализ металлов и сплавов.
Проведение неразрушающего контроля возможно на территории Московской области и в других регионах РФ в том числе городах: Москва, Дмитров, Долгопрудный, Химки, Зеленоград, Красногорск, Балашиха, Королев, Жуковский, Люберцы, Лобня, Подольск, Электросталь, Коломна, Одинцово, Домодедово, Щелково, Серпухов, Ногинск, Пушкино, Сергиев Посад, Воскресенск, Ивантеевка, Дубна, Егорьевск, Чехов, Клин, Подольск, Реутов, Видное, Ступино, Наро-Фоминск, Фрязино, Лыткарино, Дзержинский, Солнечногорск, Кашира, Котельники, Нахабино, Красноармейск, Протвино, Истра, Шатура, Луховицы, Можайск, Дедовск, Ликино-Дулево, Апрелевка, Красноармейск, Озеры, Санкт-Петербург, Екатеринбург, Владимир, Иваново, Калуга, Кострома, Курск, Липецк, Муром, Новосибирск, Обнинск, Омск, Орёл, Псков, Ржев, Ростов, Рязань, Смоленск, Сочи, Тамбов, Тверь, Тобольск, Томск, Тула, Уфа, Челябинск, Ярославль и другие города.
Спектральный (химический) анализ породы необходим в геологии и геохимии для разведки и добычи полезных ископаемых, оценки загрязнённости почвы тяжелыми металлами и другими опасными элементами. Применяемые нашей лабораторией рентгенофлуоресцентные и лазерно-искровые спектрометры оснащены специальным приложением «GeoChem Pro», содержащим калибровки для элементного анализа горных пород, руды, почвы и минералов. Данное приложение позволяет работать в расширенном диапазоне (Li3-U92) и определять содержание элементов с большей точностью. Предусмотрены функции перевода элементов в их оксиды, выбор единиц измерения (ppm или %), а также функция карты распределения элементов. Проведение спектрального анализа возможно в полевых условиях либо в нашей лаборатории. Цена анализа с выездом в Москве начинается от 30 000 руб. Сдать металл на химанализ в нашу лабораторию можно по адресу г. Лобня, ул. Борисова д. 14 к2. Заявки на направляйте по адресу kontrol@ntcexpert.ru.
Смотрите также разделы: Измерение ферритной фазы, Металлография, Измерение твердости, Спектральный анализ металлов и сплавов.
Проведение неразрушающего контроля возможно на территории Московской области и в других регионах РФ в том числе городах: Москва, Дмитров, Долгопрудный, Химки, Зеленоград, Красногорск, Балашиха, Королев, Жуковский, Люберцы, Лобня, Подольск, Электросталь, Коломна, Одинцово, Домодедово, Щелково, Серпухов, Ногинск, Пушкино, Сергиев Посад, Воскресенск, Ивантеевка, Дубна, Егорьевск, Чехов, Клин, Подольск, Реутов, Видное, Ступино, Наро-Фоминск, Фрязино, Лыткарино, Дзержинский, Солнечногорск, Кашира, Котельники, Нахабино, Красноармейск, Протвино, Истра, Шатура, Луховицы, Можайск, Дедовск, Ликино-Дулево, Апрелевка, Красноармейск, Озеры, Санкт-Петербург, Екатеринбург, Владимир, Иваново, Калуга, Кострома, Курск, Липецк, Муром, Новосибирск, Обнинск, Омск, Орёл, Псков, Ржев, Ростов, Рязань, Смоленск, Сочи, Тамбов, Тверь, Тобольск, Томск, Тула, Уфа, Челябинск, Ярославль и другие города.
Спектральный (химический) анализ драгоценных металлов применяется на всех этапах от добычи до повторной переработки. Анализ может определить содержание золота в горной породе, подтвердить пробу ювелирных изделий или чистоту технического золота, извлекаемого вторичной переработкой. Наша лаборатория делает спектральный анализ состава золота, серебра, платины, родия и палладия. Для анализа применяется современный РФА спектрометр, за несколько секунд определяющий процентное содержание драгметаллов и других элементов. Пакет специальных настроек позволяет видеть распределение золота на анализируемом участке породы и определять наличие сопутствующих золоту элементов-маркеров. Проведение анализа возможно в нашей лаборатории либо с выездом на объект заказчика. В Москве цена выездного спектрального анализа драгоценных металлов начинается от 30 000 руб. Сдать металл на химанализ в нашу лабораторию можно по адресу г. Лобня, ул. Борисова д. 14 к2. Заявки на направляйте по адресу kontrol@ntcexpert.ru.
Сфера применения | Объекты анализа |
Геологоразведка и добыча | Содержание золота в породе, самородках, сплаве Доре (лигатурное золото) |
Банковская деятельность | Чистота золотых слитков, реже серебра, платины и палладия. |
Ювелиры и нумизматы | Проверка пробы ювелирных изделий и подлинности монет |
Вторичная переработка | Содержание Au, Ag, Rh, Pd, Pt в автокатализаторах и переработанном радиоломе. |
Прочие сферы | Антиквариат, сусальное золото |
Дополнительные материалы:
- ГОСТ 17234-71. Золотые сплавы. Метод определения содержание золота и серебра.
- ГОСТ 27973.1-88. Золото. Методы атомно-эмиссионного спектрального анализа.
- ГОСТ 12563.2-83. Золото-палладиевые сплавы. Метод спектрального анализа.
- ГОСТ 16321.2-70. Серебряно-медные сплавы. Метод спектрального анализа.
- ГОСТ 12551.2-82. Платино-медные сплавы. Методы спектрального анализа.
- ГОСТ 12553.2-77. Платино-палладиевые сплавы. Метод спектрального анализа.
- ГОСТ 12556.2-82. Платино-родиевые сплавы. Методы спектрального анализа.
- ГОСТ 12227.0-76. Родий. Метод спектрального анализа.
- ГОСТ 12559.2-82. Платино-иридиевые сплавы. Методы спектрального анализа.
- ГОСТ 12223.0-76. Иридий. Метод спектрального анализа.
Смотрите также разделы: Измерение ферритной фазы, Металлография, Измерение твердости, Спектральный анализ металлов и сплавов.
Проведение неразрушающего контроля возможно на территории Московской области и в других регионах РФ в том числе городах: Москва, Дмитров, Долгопрудный, Химки, Зеленоград, Красногорск, Балашиха, Королев, Жуковский, Люберцы, Лобня, Подольск, Электросталь, Коломна, Одинцово, Домодедово, Щелково, Серпухов, Ногинск, Пушкино, Сергиев Посад, Воскресенск, Ивантеевка, Дубна, Егорьевск, Чехов, Клин, Подольск, Реутов, Видное, Ступино, Наро-Фоминск, Фрязино, Лыткарино, Дзержинский, Солнечногорск, Кашира, Котельники, Нахабино, Красноармейск, Протвино, Истра, Шатура, Луховицы, Можайск, Дедовск, Ликино-Дулево, Апрелевка, Красноармейск, Озеры, Санкт-Петербург, Екатеринбург, Владимир, Иваново, Калуга, Кострома, Курск, Липецк, Муром, Новосибирск, Обнинск, Омск, Орёл, Псков, Ржев, Ростов, Рязань, Смоленск, Сочи, Тамбов, Тверь, Тобольск, Томск, Тула, Уфа, Челябинск, Ярославль и другие города.
Определение химического состава необходимо для проверки марок сталей и сплавов, в том числе алюминиевых, медных, титановых, а также, черных сталей, отличающихся только по углероду. Исследование позволяет определить присутствие примесей и прогнозировать эксплуатационные характеристики готового изделия. Наша аккредитованная лаборатория определяет химический состав черных и цветных металлов в диапазоне от углерода до урана (C⁶-U⁹²). Результаты анализа показывают долю каждого элемента и наиболее близкие по элементному составу марки. Анализ проводится рентгенофлуоресцентным (РФА) и лазерно-искровым (ЛИЭС) спектрометром. Результаты анализа показывают долю каждого элемента и наиболее близкие по элементному составу марки. Проведение анализа возможно в нашей лаборатории или на территории заказчика. Цена выездного химического анализа в Москве начинается от 30 000 руб. Сдать металл на химанализ в нашу лабораторию можно по адресу г. Лобня, ул. Борисова д. 14 к2. Заявки на направляйте по адресу kontrol@ntcexpert.ru.
Смотрите также разделы: Измерение ферритной фазы, Металлография, Измерение твердости, Спектральный анализ металлов и сплавов.
Проведение неразрушающего контроля возможно на территории Московской области и в других регионах РФ в том числе городах: Москва, Дмитров, Долгопрудный, Химки, Зеленоград, Красногорск, Балашиха, Королев, Жуковский, Люберцы, Лобня, Подольск, Электросталь, Коломна, Одинцово, Домодедово, Щелково, Серпухов, Ногинск, Пушкино, Сергиев Посад, Воскресенск, Ивантеевка, Дубна, Егорьевск, Чехов, Клин, Подольск, Реутов, Видное, Ступино, Наро-Фоминск, Фрязино, Лыткарино, Дзержинский, Солнечногорск, Кашира, Котельники, Нахабино, Красноармейск, Протвино, Истра, Шатура, Луховицы, Можайск, Дедовск, Ликино-Дулево, Апрелевка, Красноармейск, Озеры, Санкт-Петербург, Екатеринбург, Владимир, Иваново, Калуга, Кострома, Курск, Липецк, Муром, Новосибирск, Обнинск, Омск, Орёл, Псков, Ржев, Ростов, Рязань, Смоленск, Сочи, Тамбов, Тверь, Тобольск, Томск, Тула, Уфа, Челябинск, Ярославль и другие города.
Химический (спектральный) анализ необходим для приемки металлолома, оценки автомобильных катализаторов, изучения горной породы, почвы и других объектов. Исследование позволяет определить присутствие примесей и прогнозировать эксплуатационные характеристики готового изделия. Наша лаборатория делает химический анализ состава черных и цветных металлов в диапазоне от углерода до урана (C⁶-U⁹²), в том числе алюминиевых сплавов, нержавейки, титана золота и других драгоценных металлов, а также черных сталей, отличающихся только по углероду. Анализ проводится рентгенофлуоресцентным (РФА) и лазерно-искровым (ЛИЭС) спектрометром. Результаты анализа показывают долю каждого элемента и наиболее близкие по элементному составу марки. Проведение анализа возможно в нашей лаборатории или на территории заказчика. Цена выездного химического анализа в Москве начинается от 30 000 руб. Сдать металл на химанализ в нашу лабораторию можно по адресу г. Лобня, ул. Борисова д. 14 к2. Заявки на направляйте по адресу kontrol@ntcexpert.ru.
Смотрите также разделы: Измерение ферритной фазы, Металлография, Измерение твердости, Спектральный анализ металлов и сплавов.
Проведение неразрушающего контроля возможно на территории Московской области и в других регионах РФ в том числе городах: Москва, Дмитров, Долгопрудный, Химки, Зеленоград, Красногорск, Балашиха, Королев, Жуковский, Люберцы, Лобня, Подольск, Электросталь, Коломна, Одинцово, Домодедово, Щелково, Серпухов, Ногинск, Пушкино, Сергиев Посад, Воскресенск, Ивантеевка, Дубна, Егорьевск, Чехов, Клин, Подольск, Реутов, Видное, Ступино, Наро-Фоминск, Фрязино, Лыткарино, Дзержинский, Солнечногорск, Кашира, Котельники, Нахабино, Красноармейск, Протвино, Истра, Шатура, Луховицы, Можайск, Дедовск, Ликино-Дулево, Апрелевка, Красноармейск, Озеры, Санкт-Петербург, Екатеринбург, Владимир, Иваново, Калуга, Кострома, Курск, Липецк, Муром, Новосибирск, Обнинск, Омск, Орёл, Псков, Ржев, Ростов, Рязань, Смоленск, Сочи, Тамбов, Тверь, Тобольск, Томск, Тула, Уфа, Челябинск, Ярославль и другие города.
Спектральный (химический) анализ алюминия применяется на всех этапах от добычи до повторной переработки. Анализ может определить содержание Al в горной породе, подтвердить заявленную поставщиком марку или чистоту технического алюминия, извлекаемого вторичной переработкой. Спектральный анализ алюминия можно условно разделись на базовый и тонкий. Базовая сортировка не определяет легкие элементы (Al, Mg, Si), показывая только их суммарную долю. Такой функционал имеют бюджетные и устаревшие модели с полупроводниковым PIN детектором, рассчитанные на работу с титаном и более тяжелыми элементами. Базовый анализ неприменим для точного определения марки алюминия и сплавов на его основе отличающихся только содержанием дополнительных элементов, таких как магний, кремний или марганец.
Наша аккредитованная лаборатория оснащена современным рентгенофлуоресцентным (РФА) и лазерно-искровым (ЛИЭС) спектрометром, дающие возможность тонкой сортировки с определением марки алюминия и его сплавов в том числе Al-Si, Al-Mg, Al-Fe, Al-Li. Пределы обнаружения по магнию и кремнию составляют 0.25% и 0.1% соответственно. Это позволяет быстро идентифицировать марки, отличающиеся только низкими концентрациями данных элементов, например АК8, Д16, АмЦ и Д12. Проведение спектрального анализа возможно лабораторно или с выездом на объект заказчика. Цена выездного анализа в Москве начинается от 30 000 руб. Сдать алюминий на спектральный анализ в нашу лабораторию можно по адресу г. Лобня, ул. Борисова д. 14 к2. Заявки на спектрометрию направляйте по адресу kontrol@ntcexpert.ru.
Дополнительные материалы:
- ГОСТ 7727-81 Сплавы алюминиевые. Методы спектрального анализа
- ГОСТ 3221-85. Алюминий первичный. Методы спектрального анализа.
Сортировка алюминия
Подпишитесь на наш канал YouTube
Смотрите также разделы: Измерение ферритной фазы, Металлография, Измерение твердости, Спектральный анализ металлов и сплавов.
Проведение неразрушающего контроля возможно на территории московской области и в других регионах РФ в том числе городах: Москва, Дмитров, Долгопрудный, Химки, Зеленоград, Красногорск, Балашиха, Королев, Жуковский, Люберцы, Лобня, Подольск, Электросталь, Коломна, Одинцово, Домодедово, Щелково, Серпухов, Ногинск, Пушкино, Сергиев Посад, Воскресенск, Ивантеевка, Дубна, Егорьевск, Чехов, Клин, Подольск, Реутов, Видное, Ступино, Наро-Фоминск, Фрязино, Лыткарино, Дзержинский, Солнечногорск, Кашира, Котельники, Нахабино, Красноармейск, Протвино, Истра, Шатура, Луховицы, Можайск, Дедовск, Ликино-Дулево, Апрелевка, Красноармейск, Озеры, Санкт-Петербург, Екатеринбург, Владимир, Иваново, Калуга, Кострома, Курск, Липецк, Муром, Новосибирск, Обнинск, Омск, Орёл, Псков, Ржев, Ростов, Рязань, Смоленск, Сочи, Тамбов, Тверь, Тобольск, Томск, Тула, Уфа, Челябинск, Ярославль и другие города.
Для защиты трубопроводов от коррозии применяются изоляционные покрытия разных типов. В процессе эксплуатации могут возникать дефекты изоляции, нарушающие их сплошность и защитные свойства. В связи с этим, контроль изоляции трубопроводов является важным условием безаварийной эксплуатации в течение всего срока их службы.
Наиболее часто применимым методом неразрушающего контроля изоляции трубопроводов является электроискровой метод. Искровые дефектоскопы фиксируют электрические пробои информируя пользователя о наличии дефекта звуковой и световой сигнализацией. Такие приборы работают с напряжением от 0,5 до 35 кВ, позволяя контролировать покрытия толщиной от 40 мкм до 40 мм, и выявлять дефекты размером от 50 мкм. К преимуществам этого метода можно отнести высокие скорость контроля и достоверность результатов. В России данный метод регламентирован ГОСТ 34395-2018.
Другим методом электрического контроля, получившим широкое распространение в зарубежной практике является метод влажной губки (Holiday Testing) описанный в ASTM D 5162: 2015. В отличии от искрового, данный метод использует низковольтное напряжение до 100 В, при котором возможность повреждения покрытия искровым пробоем полностью исключена. Недостатками метода являются низкая производительности (губку надо постоянно смачивать и протирать поверхность покрытия после обнаружения дефекта) и низкая чувствительность к дефектам типа утонения и включения.
Наша аттестованная лаборатория оказывает услуги по неразрушающему контролю изоляции трубопроводов. Работы проводятся дефектоскопистами, аттестованными на II и III уровни согласно СДАНК-02-2020 и имеющими всё необходимое оборудование (дефектоскоп, толщиномер, трещиномер). По результатам контроля выдается заключение о качестве контролируемого покрытия (примеры). Стоимость электрического контроля сплошности покрытий начинается от 100 рублей за погонный метр. Для составления КП необходимо дать описание объекта и контролируемого покрытия, сообщить место проведения и количество объектов контроля. Работы возможны в Москве и на всей территории РФ. Заявки направляйте по адресу kontrol@ntcexpert.ru
Статьи и нормативы по контролю изоляции трубопроводов:
- ГОСТ 34395-2018 - Материалы лакокрасочные. Электроискровой метод контроля сплошности диэлектрических покрытий на токопроводящих основаниях
- ГОСТ Р51164–98 - Трубопроводы стальные магистральные. Общие требования к защите от коррозии.
- Технологическая инструкция компании Роснефть «Антикоррозионная защита металлических конструкций на объектах нефтегазодобычи, нефтегазопереработки и нефтепродуктообеспечения компании»
- ASTM D 5162: 2015 - Стандартный порядок испытания нарушений сплошности (тест Холидей) непроводящих защитных покрытий на металлических подложках
- ВСН 210-87 - Инструкция по применению комплекса устройств для неразрушающего контроля сплошности изоляционных покрытий заглубленных трубопроводов
- Контроль и диагностика поверхностных слоев и покрытий. Тенденции и перспективы
- Приборы контроля сплошности покрытий
Контроль покрытий электроискровым дефектоскопом Elcometer
Подпишитесь на наш канал YouTube
Заявки на услуги по контролю изоляции трубопроводов направляйте по адресу kontrol@ntcexpert.ru. Смотрите так же разделы – Услуги по измерению твердости, Услуги по УЗК, Услуги по измерению шероховатости.
О качестве бетона судят в первую очередь по его прочности. Прочность бетона — это величина, выражающая его способность сопротивляться разрушению под внешним воздействием. Способы определения прочности бетона можно условно поделить на разрушающие и неразрушающие. К первому относятся испытания контрольных образцов на сжатие под прессом. Второй способ более вариативен и предусматривает семь различных методик, применяемых в зависимости от задач и условий контроля. Неразрушающие методы определения прочности особенно актуальны при невозможности выборки образцов, при больших объемах контроля, в процессе строительства, эксплуатации и реконструкции.
Общие правила контроля прочности бетона изложены в ГОСТ 18105-2010. Определение прочности бетона механическими методами неразрушающего контроля посвящен ГОСТ 22690-2015. Описание ультразвукового метода измерения прочности содержится в ГОСТ 17624-2012. Оборудование для контроля прочности бетона должно быть поверено. Персонал должен быть аттестован в одной из систем оценки соответствия. Нормативные предписания по различным методам приведены в таблице. Другие нормативы и статьи по данной теме можно найти в конце страницы.
Наша аттестованная лаборатория оказывает услуги определения прочности бетона неразрушающими методами. Работы проводятся специалистами, аттестованными по СДАНК-02-2020 и имеющими всё необходимое оборудование. По результатам контроля выдается подробное заключение (примеры). Стоимость работ по измерению прочности начинается от 500 руб. за 1 образец. Для составления КП необходимо сообщить метод необходимых испытаний, чертеж или фото, место проведения и количество контролируемых объектов. Контроль возможен в Московском регионе и за его пределами. Помимо услуг по контролю наша компания занимается поставкой оборудования для контроля бетона методами НК. Заявки направляйте по адресу kontrol@ntcexpert.ru.
Неразрушающие методы определения прочности бетона
Косвенные методы неразрушающего контроля прочности бетона | Прямые методы неразрушающего контроля бетона (методы местных разрушений) | ||||||
Ударный импульс | Упругий отскок | Пластическая деформация | Ультразвуковое обследование | Скалывание ребра | Отрыв со скалыванием | Отрыв металлических дисков | |
Диапазон прочности МПа | 5-150 | 5-50 | 5-50 | 10-40 | 10-70 | 5-100 | 5-60 |
Погрешность измерений | ± 50% | ± 50% | ± 30-40% | ± 30-50% | Нет данных | Нет данных | Нет данных |
Количество измерений | 10 | 9 | 5 | 3 или 4 | - | 150 | 50 |
Мин. расстояние от края изделия, мм | 50 | 50 | 50 | - | 2 | 1-2 | 1 |
Мин. расстояние между местами измерений мм | 15 | 30 | 30 | - | 200 | 5h | 2 диаметра диска |
Минимальная толщина образца, мм | 50 | 100 | 70 | - | 170 | 2h | 50 |
Типовое оборудование | ИПС-МГ4 | Молоток Шмидта | Молоток Кашкарова | Тестер UK1401 | ПОС-60МГ4 | ПСО-ХМГ4 | Оникс-1 |
Преимущества | Простота. Возможность определять класс бетона. | Простота и скорость исследования. | Простота и дешевизна. | Возможность определения прочности глубинных слоев. | Простота. Подготовка образцов не требуется. |
Высокая точность. Наличие градуировочных зависимостей по ГОСТ | Подходит для густоармированных конструкций. Менее трудоёмкий, чем отрыв со скалыванием. |
Недостатки | Низкая точность. Контролируется только верхний слой 25-30 мм. | Нужна подготовка поверхности. Контролируется только верхний слой 25-30 мм. | Низкая точность. | Нужна подготовка поверхности и высокая квалификация контроллера. | Не применим для поврежденного бетона и при толщине меньше 2 см | Трудоёмкость. Неприменимость для густоармированных и тонкостенных объектов. |
Нужна подготовка: на бетон нужно наклеить диски за 3-24 часа до проверки. |
Дополнительная информация:
- ГОСТ 18105-2010 Бетоны. Правила контроля и оценки прочности
- ГОСТ 22690-2015 Бетоны. Определение прочности механическими методами неразрушающего контроля
- ГОСТ 17624-2012 Бетоны. Ультразвуковой метод определения прочности
- ГОСТ 24332-88 Кирпич и камни силикатные. Ультразвуковой метод определения прочности при сжатии
- ГОСТ 10180-2012 Бетоны. Методы определения прочности по контрольным образцам
- Определение прочности бетона с использованием молотка Шмидта (по DIN EN 12504-2: 2001-12)
- Определение прочности бетона на отрыв адгезии нанесённых на бетон покрытий
- Оценка прочности бетона в конструкциях при их возведении и эксплуатации
Смотрите также разделы: Дефектоскопы для бетона, Услуги по контролю бетона, Приборы для поиска арматуры, Обучение и аттестация специалистов.
Автоматизация процессов неразрушающего контроля является одним из векторов развития мирового рынка НК. Основное преимущество автоматизации - это повышение качества контроля при снижении стоимости и сроков. Высокоточный автоматизированный контроль все чаще становится обязательным требованием для работы с крупными российскими и зарубежными заказчиками в нефтегазовой, металлургической, атомной и военной отраслях. Наибольший эффект от использования автоматизации достигается на предприятиях проводящих поточный контроль однотипных изделий, обычно это металлические и пластиковые трубы, листовой прокат, литые заготовки и рельсы. В ряде случае автоматизация необходима для контроля труднодоступных или опасных для человека объектов, например на атомных станциях.
Наша лаборатория НК предлагает услуги по разработке и производству автоматизированных систем ультразвукового, вихретокового, капиллярного и оптического контроля, в том числе с применением современных методов ФР, TODF, ЭМАП. Мы разрабатываем и внедряем как уже широко известные комплексы, так и узкопрофильные системы для контроля нестандартных объектов. Опишите вашу задачу, а наши специалисты помогут подобрать подходящее оборудование по оптимальной цене.
Смотрите также разделы: Услуги по ультразвуковому контролю, Услуги по капиллярному контролю, Услуги по магнитному контролю.
Проведение неразрушающего контроля возможно на территории московской области и в других регионах РФ в том числе городах: Москва, Дмитров, Долгопрудный, Химки, Зеленоград, Красногорск, Балашиха, Королев, Жуковский, Люберцы, Лобня, Подольск, Электросталь, Коломна, Одинцово, Домодедово, Щелково, Серпухов, Ногинск, Пушкино, Сергиев Посад, Воскресенск, Ивантеевка, Дубна, Егорьевск, Чехов, Клин, Подольск, Реутов, Видное, Ступино, Наро-Фоминск, Фрязино, Лыткарино, Дзержинский, Солнечногорск, Кашира, Котельники, Нахабино, Красноармейск, Протвино, Истра, Шатура, Луховицы, Можайск, Дедовск, Ликино-Дулево, Апрелевка, Красноармейск, Озеры, Санкт-Петербург, Екатеринбург, Владимир, Иваново, Калуга, Кострома, Курск, Липецк, Муром, Новосибирск, Обнинск, Омск, Орёл, Псков, Ржев, Ростов, Рязань, Смоленск, Сочи, Тамбов, Тверь, Тобольск, Томск, Тула, Уфа, Челябинск, Ярославль и другие города.
Тепловизор достаточно дорогой прибор, поэтому для решения разовых задач, аренда выгоднее покупки. Аренда тепловизора особенно актуальна при сдаче-приемке квартиры или коттеджа, поиске источников потери тепла, перегрева электросетей, выявлении очагов плесени и других проблемных участков для своевременного обслуживания и снижения расходов. В настоящее время наша компания предоставляет услугу аренды тепловизора только с оператором. Наша компания работает с юридическими и физическими лицами. Аренда возможна для обследования объектов в Москве, области и ближайших регионах.
Помимо проведения контроля, наша организация оказывает услуги по аттестации специалистов и лабораторий теплового контроля, помощь в подборе необходимого оборудования. Обследование тепловизором проводится с применением современных промышленных тепловизоров с матрицей 320x240 пикселей. Рабочие тепловизоры внесены в Госреестр и имеют свидетельство о поверке.
Лаборатория НТЦ «Эксперт» также оказывает профессиональные услуги по тепловизионному обследованию промышленных и жилых объектов. По результатам тепловизионного обследования составляется подробный отчет, включающий наглядную тепловую карту (термограмму), заключение о качестве объекта. Заключение выдается аттестованной лабораторией теплового контроля и может быть использовано как для решения производственных задач, так и аргументировать позицию заказчика в спорах с подрядными организациям.
Примерная стоимость аренды тепловизора (с оператором)
Объекты | Стоимость работ | |
Квартиры | 1 комната | 3 500 - 5 000 руб. (термограмма / полный отчет) |
2 комнаты | 4 500 - 6 000 руб. (термограмма / полный отчет) | |
3-5 комнатные | 5 000 - 7 000 руб. (термограмма / полный отчет) | |
Коттеджи | до 150 м2 | 4 000 - 6 000 руб. (термограмма / полный отчет) |
150 - 350 м2 | 6 000 - 8 000 руб. (термограмма / полный отчет) | |
350 - 500 м2 | 7 000 - 10 000 руб. (термограмма / полный отчет) | |
Здания | до 1000 м2 | 30 руб. за 1 м2 |
1000 - 5000 м2 | 25 руб. за 1 м2 | |
5000 -10000 м2 | 20 руб. за 1 м2 | |
Электрощиты | до 1 м2 | 1000 руб. за щит |
1 - 3 м2 | 2000 руб. за щит | |
3 - 5 м2 | 3000 руб. за щит | |
Трансформаторы | 6-10 кВ | 6 000 руб. |
35 кВ | 15 000 руб. | |
110-220 кВ | 20 000 руб. | |
Кабели и трубопроводы | 1 пог. м. шириной до 1 м | 30 руб. за погонный метр |
1 пог. м. шириной до 2 м | 40 руб. за погонный метр | |
1 пог. м. шириной до 3 м | 50 руб. за погонный метр | |
Аренда тепловизора (с оператором) | 3 500 руб. за 1 час работ |
Условная классификация обследуемых объектов и типов выявляемых нарушений приведена в таблице:
Группа объектов | Тип объекта | Тип выявляемы нарушений | Основные нормативы | Примеры термограммы |
Промышленные, жилые и административные здания | цеха, многоквартирные дома, квартиры, дачи, школы, больницы |
|
ГОСТ Р 54852-2011 СП 50.13330.2012 (актуализированная редакция СНиП 23-02-2003) ГОСТ 25380-2014 |
![]() ![]() ![]() |
Промышленные сооружения | дымовые трубы, мосты, градирни, стальные конструкции |
|
РД-13-04-2006 | ![]() |
Машины и оборудование | Транспорт, котлы, холодильники, двигатели, конвейеры, насосы, лопатки турбин, компрессоры, зубчатые передачи |
|
РД-13-04-2006 | ![]() |
Энергетические сети | трубопроводы, ЛЭП, ЦТП, печи, котлы, радиаторы отопления, солнечные батареи |
|
РД-13-04-2006 РД 153-34.0-20.364-00 |
![]() ![]() ![]() |
Электрооборудование | распределительные щиты, трансформаторы, конденсаторы, генераторы, предохранители, силовые кабели, радиоэлектроника, печатные платы |
|
РД 153-34.0-20.363-99 | ![]() |
Дополнительная информация:
- Пример отчета по результатам тепловизионного контроля
- Практическое руководство по термографии от компании Testo
- Введение в термографию от компании Fluke
- Применение тепловизоров в профилактическом техническом обслуживании (Flir)
- Пособие по выбору тепловизора
- Ассортимент поставляемых тепловизоров и других приборов теплового контроля
- Перечень ГОСТов по тепловому контролю
- Статья - «Диагностика строительных конструкция методом инфракрасной термографии»
- Статья – «Комплексный тепловой контроль зданий и строительных сооружений
- Статья – «Оценка фактической теплозащиты зданий методом теплового контроля»
- Статья – «Опыт применения теплового контроля в нефтепереработке»
- Статья – «Тепловой контроль изделий микроэлектроники»
- Аттестация специалистов по тепловому методу
- Аттестация лабораторий по тепловому методу
- Квалификационное удостоверение НОАП
- Свидетельство о поверке тепловизора
- Свидетельство об аттестации лаборатории
Заявки на тепловизионное обследование можно отправить по адресу kontrol@ntcexpert.ru. Смотрите так же разделы – Услуги по тепловому контролю, Тепловизионное обследование, Проведение работ по НК, Аттестация лабораторий НК, Обучение и аттестация дефектоскопистов, Нормативная база по НК в том числе ГОСТы, РД, ПНАЭ, EN, ISO
Аренда тепловизора для физических и юридических лиц возможно на территории Московской области и в других регионах РФ в том числе городах: Москва, Дмитров, Долгопрудный, Химки, Зеленоград, Красногорск, Балашиха, Королев, Жуковский, Люберцы, Лобня, Подольск, Электросталь, Коломна, Одинцово, Домодедово, Щелково, Серпухов, Ногинск, Пушкино, Сергиев Посад, Воскресенск, Ивантеевка, Дубна, Егорьевск, Чехов, Клин, Подольск, Реутов, Видное, Ступино, Наро-Фоминск, Фрязино, Лыткарино, Дзержинский, Солнечногорск, Кашира, Котельники, Нахабино, Красноармейск, Протвино, Истра, Шатура, Луховицы, Можайск, Дедовск, Ликино-Дулево, Апрелевка, Красноармейск, Озеры, Санкт-Петербург, Екатеринбург, Владимир, Иваново, Калуга, Кострома, Курск, Липецк, Муром, Новосибирск, Обнинск, Омск, Орёл, Псков, Ржев, Ростов, Рязань, Смоленск, Сочи, Тамбов, Тверь, Тобольск, Томск, Тула, Уфа, Челябинск, Ярославль и другие города.
Лаборатория НТЦ «Эксперт» и оказывает услуги по тепловизионному обследованию промышленных и жилых объектов. Целью тепловизионного обследования является поиск аномальных температурных участков, по которым можно судить о техническом состоянии объектов контроля. Основные задачи, решаемые тепловизионным обследованием это снижение теплопотерь зданий, поиск перегрева электросетей, мониторинг производственных процессов, выявление очагов плесени и других проблемных участков для своевременного обслуживания и снижения расходов.
По результатам тепловизионного обследования составляется подробный отчет, включающий наглядную тепловую карту (термограмму), заключение о качестве объекта. Заключение выдается аттестованной лабораторией теплового контроля и может быть использовано как для решения производственных задач, так и аргументировать позицию заказчика в спорах с подрядными организациям. Наша компания работает с юридическими и физическими лицами. Обследование возможно в московском регионе и за его пределами. Помимо проведения контроля, наша организация оказывает услуги по аттестации специалистов и лабораторий теплового контроля, помощь в подборе необходимого оборудования.
Тепловизионное обследование проводится с применением современных промышленных тепловизоров и других приборов. Используемые в работе приборы внесены в Госреестр и имеют свидетельство о поверке. Тепловизоры обладают высокой температурной чувствительностью позволяющей различать на термограмме объекты с разницей температур менее 1°С. Диапазон измеряемой температуры находится в пределах от -20°C до 350°C.
Условная классификация обследуемых объектов и типов выявляемых нарушений приведена в таблице:
Группа объектов | Тип объекта | Тип выявляемых нарушений | Основные нормативы | Примеры термограммы |
Промышленные, жилые и административные здания | цеха, многоквартирные дома, квартиры, дачи, школы, больницы |
|
ГОСТ Р 54852-2011 СП 50.13330.2012 (актуализированная редакция СНиП 23-02-2003) ГОСТ 25380-2014 |
![]() ![]() ![]() |
Промышленные сооружения | дымовые трубы, мосты, градирни, стальные конструкции |
|
РД-13-04-2006 | ![]() |
Машины и оборудование | Транспорт, котлы, холодильники, двигатели, конвейеры, насосы, лопатки турбин, компрессоры, зубчатые передачи |
|
РД-13-04-2006 | ![]() |
Энергетические сети | трубопроводы, ЛЭП, ЦТП, печи, котлы, радиаторы отопления, солнечные батареи |
|
РД-13-04-2006 РД 153-34.0-20.364-00 |
![]() ![]() ![]() |
Электрооборудование | распределительные щиты, трансформаторы, конденсаторы, генераторы, предохранители, силовые кабели, радиоэлектроника, печатные платы |
|
РД 153-34.0-20.363-99 | ![]() |
Примерные цены тепловизионного обследования
Объекты | Стоимость работ | |
Квартиры | 1 комната | 3 500 - 5 000 руб. (термограмма / полный отчет) |
2 комнаты | 4 500 - 6 000 руб. (термограмма / полный отчет) | |
3-5 комнатные | 5 000 - 7 000 руб. (термограмма / полный отчет) | |
Коттеджи | до 150 м2 | 4 000 - 6 000 руб. (термограмма / полный отчет) |
150 - 350 м2 | 6 000 - 8 000 руб. (термограмма / полный отчет) | |
350 - 500 м2 | 7 000 - 10 000 руб. (термограмма / полный отчет) | |
Здания | до 1000 м2 | 30 руб. за 1 м2 |
1000 - 5000 м2 | 25 руб. за 1 м2 | |
5000 -10000 м2 | 20 руб. за 1 м2 | |
Электрощиты | до 1 м2 | 1000 руб. за щит |
1 - 3 м2 | 2000 руб. за щит | |
3 - 5 м2 | 3000 руб. за щит | |
Трансформаторы | 6-10 кВ | 6 000 руб. |
35 кВ | 15 000 руб. | |
110-220 кВ | 20 000 руб. | |
Кабели и трубопроводы | 1 пог. м. шириной до 1 м | 30 руб. за погонный метр |
1 пог. м. шириной до 2 м | 40 руб. за погонный метр | |
1 пог. м. шириной до 3 м | 50 руб. за погонный метр | |
Аренда тепловизора (с оператором) | 3 500 руб. за 1 час работ |
Дополнительная информация:
- Пример отчета по результатам тепловизионного контроля
- Практическое руководство по термографии от компании Testo
- Введение в термографию от компании Fluke
- Применение тепловизоров в профилактическом техническом обслуживании (Flir)
- Пособие по выбору тепловизора
- Ассортимент поставляемых тепловизоров и других приборов теплового контроля
- Перечень ГОСТов по тепловому контролю
- Статья - «Диагностика строительных конструкция методом инфракрасной термографии»
- Статья – «Комплексный тепловой контроль зданий и строительных сооружений
- Статья – «Оценка фактической теплозащиты зданий методом теплового контроля»
- Статья – «Опыт применения теплового контроля в нефтепереработке»
- Статья – «Тепловой контроль изделий микроэлектроники»
- Аттестация специалистов по тепловому методу
- Аттестация лабораторий по тепловому методу
- Квалификационное удостоверение НОАП
- Свидетельство о поверке тепловизора
- Свидетельство об аттестации лаборатории
Заявки на тепловизионное обследование можно отправить по адресу kontrol@ntcexpert.ru. Смотрите так же разделы – Услуги по тепловому контролю, Аренда тепловизора, Проведение работ по НК, Аттестация лабораторий НК, Обучение и аттестация дефектоскопистов, Нормативная база по НК в том числе ГОСТы, РД, ПНАЭ, EN, ISO
Проведение теплового (тепловизионного) обследования возможно на территории Московской области и в других регионах РФ в том числе городах: Москва, Дмитров, Долгопрудный, Химки, Зеленоград, Красногорск, Балашиха, Королев, Жуковский, Люберцы, Лобня, Подольск, Электросталь, Коломна, Одинцово, Домодедово, Щелково, Серпухов, Ногинск, Пушкино, Сергиев Посад, Воскресенск, Ивантеевка, Дубна, Егорьевск, Чехов, Клин, Подольск, Реутов, Видное, Ступино, Наро-Фоминск, Фрязино, Лыткарино, Дзержинский, Солнечногорск, Кашира, Котельники, Нахабино, Красноармейск, Протвино, Истра, Шатура, Луховицы, Можайск, Дедовск, Ликино-Дулево, Апрелевка, Красноармейск, Озеры, Санкт-Петербург, Екатеринбург, Владимир, Иваново, Калуга, Кострома, Курск, Липецк, Муром, Новосибирск, Обнинск, Омск, Орёл, Псков, Ржев, Ростов, Рязань, Смоленск, Сочи, Тамбов, Тверь, Тобольск, Томск, Тула, Уфа, Челябинск, Ярославль и другие города.
Наша лаборатория оказывает услуги по тепловому контролю промышленных и жилых объектов. По результатам контроля составляется подробный отчет, включающий наглядную тепловую карту и заключение о качестве объекта (примеры). Заключение выдается аттестованной лабораторией теплового контроля и может быть использовано как для решения производственных задач, так и аргументировать позицию заказчика в спорах с подрядными организациям. Высокий уровень организации рабочих процессов нашей ЛНК дополнительно подтвержден сертификатом соответствия ISO 9001. Наша компания работает с юридическими и физическими лицами. Проведение работ возможно в московском регионе и за его пределами. Помимо проведения контроля, наша организация оказывает услуги по аттестации специалистов и лабораторий теплового контроля, помощь в подборе необходимого оборудования.
Целью теплового контроля является поиск аномальных температурных участков, по которым можно судить о техническом состоянии объектов контроля. Основные задачи, решаемые с применением теплового контроля это снижение теплопотерь, поиск перегрева электросетей, мониторинг производственных процессов, выявление очагов плесени и других проблемных участков для своевременного техобслуживания и снижения расходов. Тепловой контроль проводится с применением современных промышленных тепловизоров и других приборов. Используемые в работе приборы внесены в Госреестр и имеют свидетельство о поверке. Тепловизоры обладают высокой температурной чувствительностью позволяющей различать на термограмме объекты с разницей температур менее 1°С. Диапазон измеряемой температуры находится в пределах от -20°C до 350°C.
Условная классификация контролируемых объектов и типов выявляемых нарушений приведена в таблице:
Группа объектов | Тип объекта | Тип выявляемых нарушений | Основные нормативы | Примеры термограммы |
Промышленные, жилые и административные здания | цеха, многоквартирные дома, квартиры, дачи, школы, больницы |
|
ГОСТ Р 54852-2011 СП 50.13330.2012 (актуализированная редакция СНиП 23-02-2003) ГОСТ 25380-2014 |
![]() ![]() ![]() |
Промышленные сооружения | дымовые трубы, мосты, градирни, стальные конструкции |
|
РД-13-04-2006 | ![]() |
Машины и оборудование | Транспорт, котлы, холодильники, двигатели, конвейеры, насосы, лопатки турбин, компрессоры, зубчатые передачи |
|
РД-13-04-2006 | ![]() |
Энергетические сети | трубопроводы, ЛЭП, ЦТП, печи, котлы, радиаторы отопления, солнечные батареи |
|
РД-13-04-2006 РД 153-34.0-20.364-00 |
![]() ![]() ![]() |
Электрооборудование | распределительные щиты, трансформаторы, конденсаторы, генераторы, предохранители, силовые кабели, радиоэлектроника, печатные платы |
|
РД 153-34.0-20.363-99 | ![]() |
Примерная стоимость работ по тепловому контролю
Объекты | Стоимость работ | |
Коттеджи и квартиры | до 150 м2 | 8 000 - 10 000 руб. (термограмма / полный отчет) |
150 - 350 м2 | 10 000 - 15 000 руб. (термограмма / полный отчет) | |
350 - 500 м2 | 15 000 - 20 000 руб. (термограмма / полный отчет) | |
Здания | до 1 000 м2 | 30 руб. за 1 м2 |
1 000 – 5 000 м2 | 25 руб. за 1 м2 | |
5 000 -10 000 м2 | 20 руб. за 1 м2 | |
Трансформаторы и электрощиты | 6-10 кВ | 6 000 руб. |
35 кВ | 15 000 руб. | |
110-220 кВ | 20 000 руб. | |
Аренда тепловизора (с оператором) | 3 500 руб. за 1 час работ |
Дополнительная информация:
- Пример отчета по результатам тепловизионного контроля
- Практическое руководство по термографии от компании Testo
- Введение в термографию от компании Fluke
- Применение тепловизоров в профилактическом техническом обслуживании (Flir)
- Пособие по выбору тепловизора
- Ассортимент поставляемых тепловизоров и других приборов теплового контроля
- Перечень ГОСТов по тепловому контролю
- Статья - «Диагностика строительных конструкция методом инфракрасной термографии»
- Статья – «Комплексный тепловой контроль зданий и строительных сооружений
- Статья – «Оценка фактической теплозащиты зданий методом теплового контроля»
- Статья – «Опыт применения теплового контроля в нефтепереработке»
- Статья – «Тепловой контроль изделий микроэлектроники»
- Аттестация специалистов по тепловому методу
- Аттестация лабораторий по тепловому методу
- Квалификационное удостоверение НОАП
- Свидетельство о поверке тепловизора
- Свидетельство об аттестации лаборатории
Заявки на услуги по тепловому контролю можно отправить по адресу kontrol@ntcexpert.ru. Смотрите так же разделы – Аренда тепловизора, Тепловизионное обследование, Проведение работ по НК, Аттестация лабораторий НК, Обучение и аттестация дефектоскопистов, Нормативная база по НК в том числе ГОСТы, РД, ПНАЭ, EN, ISO
Проведение теплового (тепловизионного) контроля возможно на территории московской области и в других регионах РФ в том числе городах: Москва, Дмитров, Долгопрудный, Химки, Зеленоград, Красногорск, Балашиха, Королев, Жуковский, Люберцы, Лобня, Подольск, Электросталь, Коломна, Одинцово, Домодедово, Щелково, Серпухов, Ногинск, Пушкино, Сергиев Посад, Воскресенск, Ивантеевка, Дубна, Егорьевск, Чехов, Клин, Подольск, Реутов, Видное, Ступино, Наро-Фоминск, Фрязино, Лыткарино, Дзержинский, Солнечногорск, Кашира, Котельники, Нахабино, Красноармейск, Протвино, Истра, Шатура, Луховицы, Можайск, Дедовск, Ликино-Дулево, Апрелевка, Красноармейск, Озеры, Санкт-Петербург, Екатеринбург, Владимир, Иваново, Калуга, Кострома, Курск, Липецк, Муром, Новосибирск, Обнинск, Омск, Орёл, Псков, Ржев, Ростов, Рязань, Смоленск, Сочи, Тамбов, Тверь, Тобольск, Томск, Тула, Уфа, Челябинск, Ярославль и другие города.
Рекомендации по выбору дозиметра
В данном перечне содержатся ссылки на модели дозиметров, которые в большинстве случаев удовлетворяют требованиям перечисленных отраслей.
1 группа – лаборатории неразрушающего контроля, использующие импульсные рентгеновские аппараты - ДКС АТ-1123, ДКС-96.
2 группа – медицинские учреждения: приборы на гамма-рентген излучения для контроля установок, индивидуальный контроль персонала; (ДКС-АТ1123, ДКР-АТ1103М, ДКС-АТ3509)
3 группа – строительные организации: контроль территорий под застройку (поисковые приборы Дозы, ДКГ-03Д Грач, ДКГ-07Д Дрозд, ДКГ-02У Арбитр, ДКС-96)
4 группа – предприятия, занимающиеся сбором и отгрузкой металлолома: (приборы поисковые на гамма излучение ИСП-РМ1401МА, ИСП-РМ1701М, ДКГ-РМ1703МО-1/2)
5 группа – атомные структуры: контроль территорий АЭС, индивидуальный контроль персонала (МКС-АТ1117М, ДКС-96, ДКС-АТ3509, ДКГ-РМ1610, РМ1603А/В)
6 группа – банковские структуры: контроль загрязненности денежных знаков (МКС-РМ1405, МКС-151)
7 группа – частные лица (СИГ-РМ1208М, РМ1904 - для айфонов)
8 группа - военные ведомства, силовые структуры: поисковые приборы и индивидуальные дозиметры (МКС-РМ1402М, ДКГ-РМ1603А/В )
Сравнение характеристик малогабаритных твердомеров
Струтынский А.В., Худяков С.А.
Первоисточник статьи - https://vostok-7.ru/articles/3/
В практике судоремонта нередко возникает необходимость измерения твердости рабочих поверхностей деталей. Зачастую применение классических методов – Бринелля [1], Роквелла [2], Виккерса [3] оказывается невозможным, либо неоправданно трудоемким и непроизводительным. К таким случаям можно отнести контроль твердости крупногабаритных деталей, измерение без полной разборки узлов и в труднодоступных местах. Эти задачи могут быть решены при помощи малогабаритных твердомеров. Применение этих приборов имеет ряд особенностей и ограничений, которые необходимо учитывать. В таких приборах используется метод ультразвукового контактного импеданса (UCI - Ultrasonic Contact Impedance) и метод упругого отскока (динамический). Рассмотрим каждый из них с учетом преимуществ и недостатков.
1. Метод ультразвукового контактного импеданса
Суть метода заключается в следующем: при калиброванной нагрузке алмазная пирамидка, закрепленная на металлическом стержне, колеблющемся на резонансной частоте, внедряется в материал изделия. Частота колебаний стержня пропорциональна площади отпечатка на объекте контроля, то есть твердости материала. Метод несколько напоминает метод Виккерса [3], только площадь отпечатка оценивается без снятия нагрузки, то есть, совместно с упругой составляющей деформации. Поскольку фиксация датчика на объекте осуществляется рукой, величина рабочей нагрузки небольшая – около 10Н. При такой нагрузке и, соответственно, таком размере отпечатка метод занимает промежуточное положение между методом Виккерса [3] и методом микротвердости [4] по локальности воздействия на объект. Метод позволяет измерять твердость при любом пространственном положении датчика.
2. Метод упругого отскока
Методом упругого отскока определяется значение твердости HL по Либу (в некоторых переводах - Лейбу). Эта величина, введенная в практику измерений в 1978 г., является частным величины скорости отскока ударника к величине скорости удара, умноженным на 1000. В более твердых материалах возникает большая скорость отскока, чем в тех, у которых твердость меньше. Применительно к определенной группе материалов (например, сталь, алюминий и др.), значение HL совпадает со значением твердости, поэтому оно непосредственно и используется.
В ходе проведения испытания ударник с наконечником из твердого сплава приводится в действие пружиной, ударяется о поверхность и отскакивает. Скорости удара и отскока измеряются следующим образом: постоянный магнит, встроенный в тело ударника, проходит через катушку и в процессе своего поступательного и возвратного движения создает электрический ток. Величины возникающих при этом токов пропорциональны скоростям удара и отскока; результаты обрабатываются и представляются на дисплее индикаторного блока в виде значения твердости.
Для наиболее часто встречающихся материалов разработаны специальные кривые, позволяющие сравнивать полученные значения со стандартными статистическими (по Бринеллю, Роквеллу) и переводить их в эти системы. Метод напоминает метод Шора, только определяется не высота отскока ударника, а отношение величины скорости отскока ударника к величине скорости удара. С использованием поправок, метод позволяет измерять твердость при любом пространственном положении датчика (в отличие от метода Шора).
Следует понимать, что сопоставление величины твердости, приведенное, например, в [5], измеренной различными методами и даже одним методом, но с разными параметрами (величина, продолжительность и скорость нагружения, форма, размеры и материал индентора) не является строгим, точным и универсальным. Еще менее точной является оценка прочности сталей (временного сопротивления) по величине твердости. При подобном сопоставлении кроме [6], использующего пересчет по эмпирическому соотношению, близкому к σв = 9,8·0,35·НВ (МПа) [7], используются и другие зависимости. Например, используемая в теплоэнергетике формула σв = 9,8·(0,46·НВ – 22) лучше подходит для низкоуглеродистых сталей с твердостью до 200 НВ (см. рис.1).
Эти формулы не единственные и не претендуют на универсальность и точность. В случае измерения твердости переносным прибором происходит двойное сопоставление. Сначала динамическая твердость пересчитывается в НВ, затем во временное сопротивление. При таком "пересчете" перемножаются и коэффициенты корреляции, которые и так существенно меньше 1. Оценка пластических характеристик по твердости (относительного удлинения и сужения, ударной вязкости) обычно не проводится, так как между этими величинами нет корреляционной связи.
2.1. Сравнение основных характеристик датчиков малогабаритных твердомеров
Основные характеристики твердомеров определяют, прежде всего, характеристики датчиков. Наличие развитых сервисных функций только повышает удобство пользования прибором, что немаловажно при большом объеме измерений.
Для сравнения были выбраны датчики отечественных динамических твердомеров МЕТ-УД, ТЭМП-3 и ТДМ-2. Ультразвуковой датчик твердомера МЕТ-УД сравнивался с датчиком твердомера MICRODUR фирмы Крауткремер (рис.2).
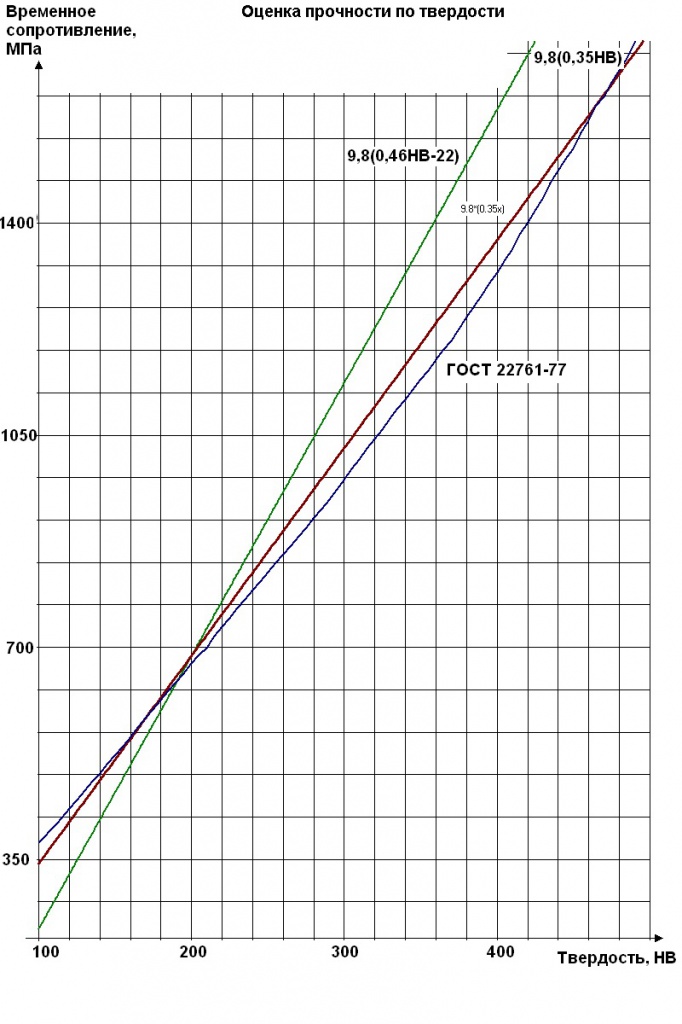
Рис. 1 Сопоставление твердости и прочности по разным методикам.
Сравнение датчика МЕТ с датчиком к прибору MICRODUR производства КРАУТКРЕМЕР не в пользу МЕТ. В датчике "MICRODUR" применен электрический привод нагружения, обеспечивающий стабильную скорость и время нагружения и значительно уменьшающий случайную составляющую погрешности измерения, в том числе, субъективный человеческий фактор. Датчик МЕТ-УД упрощенный. Такое упрощение требует от оператора хороших навыков, тщательности и аккуратности и приводит к повышенной случайной погрешности измерения.
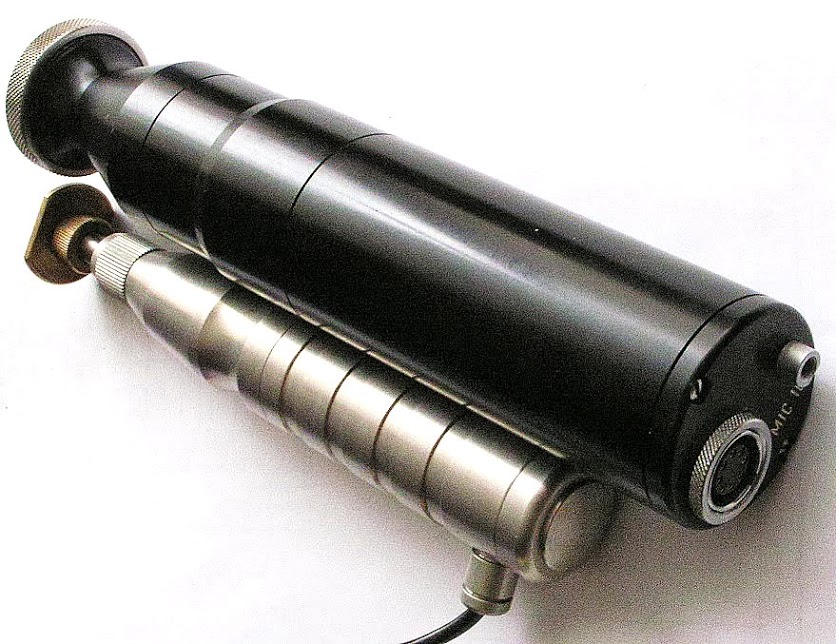
а) МЕТ-УД; б) MICRODUR
Рис.2. Внешний вид ультразвуковых датчиков.
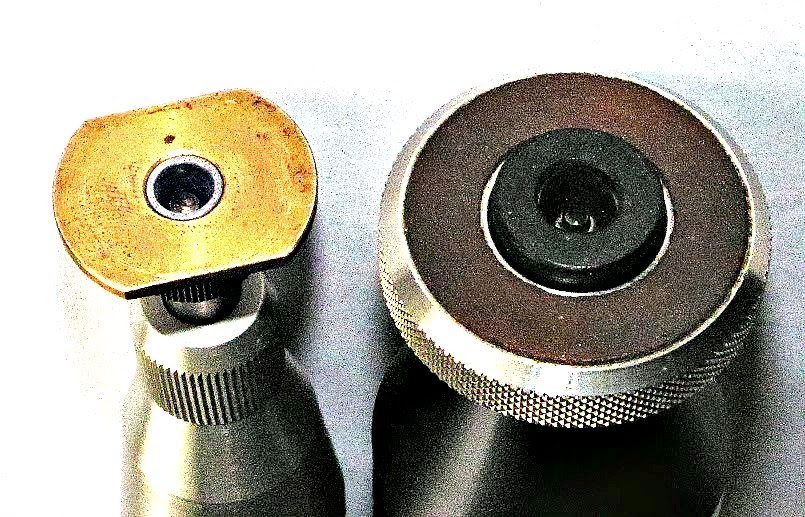
а) МЕТ-УД; б) MICRODUR
Рис.3. Поверхность базирования ультразвуковых датчиков.
Поверхность базирования датчика MICRODUR выполнена с эластичным нескользящим кольцом, обеспечивающим лучшую фиксацию датчика на объекте (рис.3).
Оба датчика оставляют отпечатки примерно одинакового размера (около 0,1 мм на стали с твердостью 150 НВ), то есть, имеют примерно одинаковые рабочие нагрузки.
В названии немецкого прибора присутствует слово "микро", напоминающее, что нагрузка и размер отпечатка приближаются к способу микротвердости [4], значительно ограничивая область применения "вслепую", без оценки микроструктуры и точности позиционирования на объекте. Производитель МЕТ-УД ограничивает только измерение твердости чугуна и, в качестве преимущества метода, указывает возможность использования этого датчика (метода) для тонкостенных конструкций (в том числе трубопроводов). Для термически упрочненных объектов с априори мелкозернистой, однородной микроструктурой (мартенсит, бейнит) проблем не предвидится, а даже для феррито-перлитной структуры возможны ограничения применения. Рассмотрим углеродистую сталь (0,1-0,2 % углерода характерно для сварных конструкций). По правилам (законам) Н. С. Курнакова известно, что твердость феррита составляет около 100 НВ, перлита -200 НВ. Твердость феррито-перлитной структуры линейно увеличивается от 100 до 200НВ пропорционально доле перлита в микроструктуре. При заявленной погрешности ± 10 НВ необходимо иметь чувствительность не менее 5 НВ, что соответствует 5 % изменению доли перлитной составляющей. То есть, минимальное количество зерен в отпечатке (при равномерном распределении структурных составляющих и одинаковой деформации под воздействием индентора) – 20. Учитывая пирамидальную форму отпечатка и, соответственно, неоднородность деформации на площади отпечатка, удвоим это число (а можно и утроить). Как указывалось выше, размер отпечатка - 0,1 мм на стали с твердостью 150 НВ, то есть, площадь – 0,01 мм2, это соответствует 4000 зерен на мм2. В [8], таблица 1, среднему значению 4096 зерен на мм2 соответствует зерно №9. То есть, метод с заявленной погрешностью работает на конструкционной стали с зерном более мелким, чем №9 (№10–14). Зерно № 7 – 8 – не редкость в стальном прокате, еще хуже может быть ситуация с поковками и отливками, где и размер зерна и неоднородность структуры значительно выше. На лицо явное недокументированное ограничение применимости метода.
2.2. Сравнение динамических датчиков
Российские производители не приводят основных характеристик датчиков, поэтому необходимо снять их самостоятельно. Для этого надо измерить диаметры шариков, массы ударников и их среднюю скорость. Для приближенного определения средней скорости необходимо записать электрические сигналы датчиков и проанализировать их.
2.2.1 Сравнение диаметров шариков
Различие диаметров шариков представлено на рис. 4
МЕТ, ТЭМП ТДМ
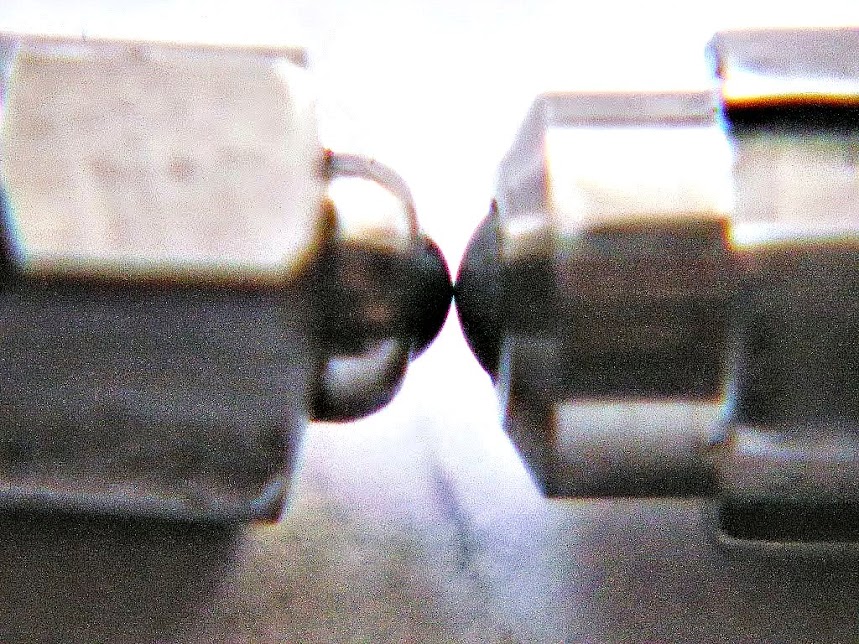
Рис. 4. Сравнение диаметров шариков
Отношение диаметров шариков составляет
DМЕТ, ТЭМП/DТДМ ≈ 0,67.
Диаметры шариков датчиков твердомеров МЕТ-УД и ТЭМП-3 составляют 2,0 мм, твердомера ТДМ-2 – 3,0 мм.
2.2.2. Сигналы датчиков
Сигналы датчиков снимались при помощи компьютерного осциллографа. Датчики устанавливались на массивную стальную плиту твердостью 150 НВ.
Осциллограммы представлены на рис. 5-7.
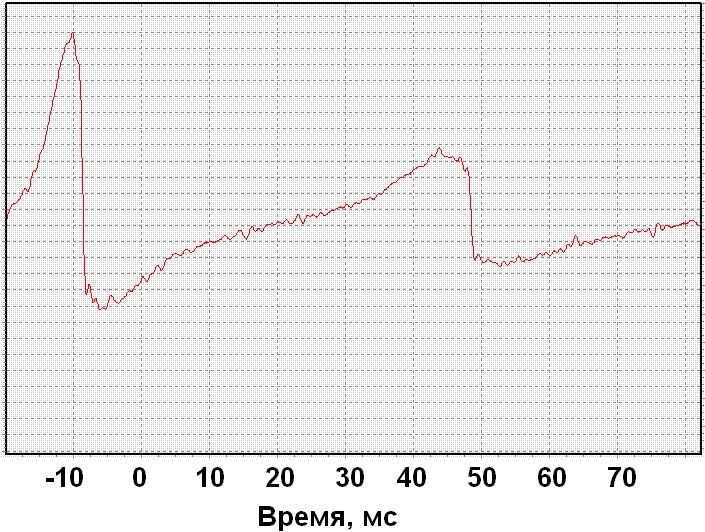
Рис. 5. Сигнал датчика твердомера МЕТ-УД.
Интервал времени между импульсами – τ = 58 мс
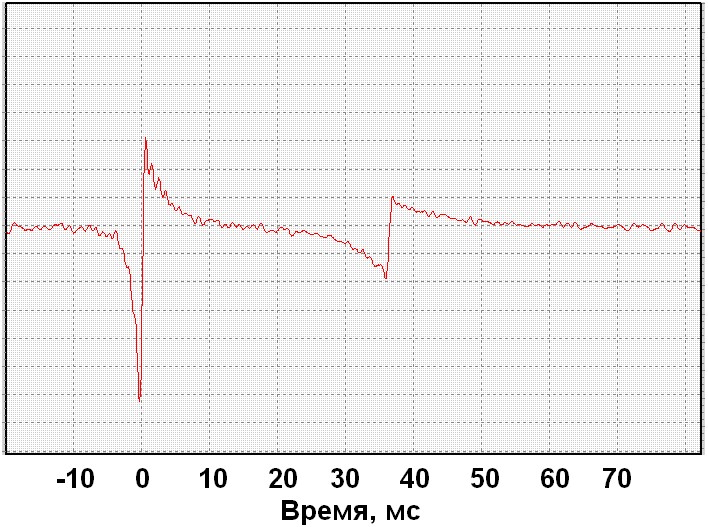
Рис. 6. Сигнал датчика твердомера ТДМ-2.
Интервал времени между импульсами – τ = 37 мс
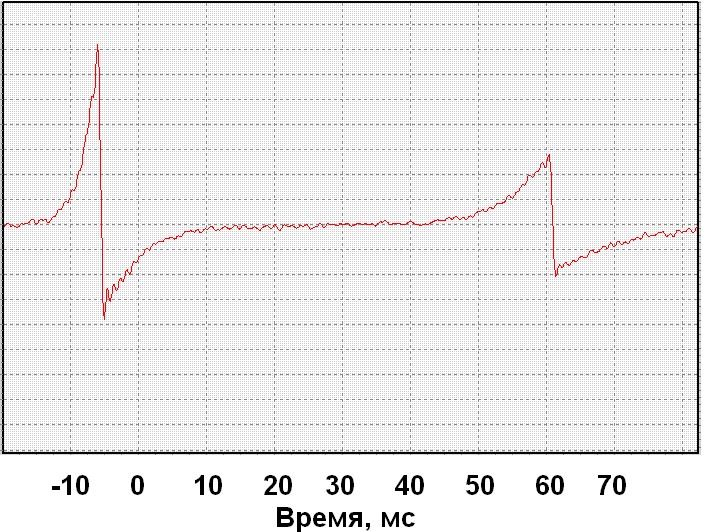
Рис. 7. Сигнал датчика твердомера ТЭМП-3.
Интервал времени между импульсами – τ = 69 мс
Сглаженный пик импульса отскока датчика МЕТ может вызывать дополнительную нестабильность показаний. Разная полярность и амплитуда – конструктивная особенность, учитываемая электронными блоками твердомеров.
2.2.3. Сравнение энергии удара (упрощенно)
Анализ сигналов позволяет определить время пролета ударника от середины катушки до поверхности объекта контроля и отскока до середины катушки. Приняв, что положение середины катушки соответствует свободному ходу ударника, среднюю скорость ударника определим по формуле:
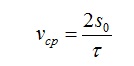
Энергию удара можно определить по формуле для кинетической энергии
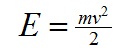
Скорость в момент удара v максимальна и составляет с учетом расходования энергии на пластическую деформацию около 4·vср то есть,
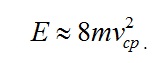
Такое упрощение не позволяет точно рассчитать энергию удара, но, с учетом того, что измерения проводились на одном образце, отношение энергий различных датчиков определяется корректно.
Результаты измерений и расчетов приведены в таблице 1.
Таблица 1. Основные характеристики датчиков твердомеров
Характеристики | МЕТ-УД | ТЭМП-3 | ТДМ-2 |
Диаметр шарика, D, мм | 2,0 | 2,0 | 3,0 |
Масса ударника, m, г | 7,0 | 8,2 | 5,5 |
Полный ход ударника, S, мм | 20 | 30 | 30 |
Свободный ход ударника, S0, мм | 8 | 15 | 12 |
Время между импульсами, τ, мс | 58 | 69 | 37 |
Средняя скорость ударника, v, м/с | 0,28 | 0,43 | 0,69 |
Энергия удара, E, мДж | 4,4 | 12,1 | 20,9 |
Энергию удара можно также оценить по характеристикам пружин:
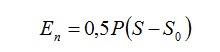
Потенциальная энергия ударника составляет:
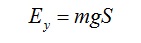
Полная энергия:
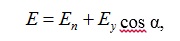
где α – угол между осью датчика и нормалью к поверхности Земли.
Отношение Еу/Еп определяет величину поправки на изменение пространственного положения датчика.
Результаты измерений и расчетов приведены в таблице 2.
Таблица 2. Основные характеристики пружин датчиков твердомеров
Характеристики | МЕТ-УД | ТЭМП-3 | ТДМ-2 |
Усилие взведенной пружины, Р, Н | 1,7 | 3,1 | 4,5 |
Полный ход ударника, S, мм | 20 | 30 | 30 |
Свободный ход ударника, S0, мм | 8 | 15 | 12 |
Потенц. энергия пружины, Eп, мДж | 10,2 | 23,25 | 40,5 |
Потенц. энергия ударника, Eу, мДж | 1,40 | 2,46 | 1,65 |
Eу / Eп | 0,137 | 0,105 | 0,041 |
Как видно из приведенных результатов, энергия удара датчиков твердомеров отличается более чем в 4 раза, причем производители твердомеров не приводят этой характеристики в паспортах и технических описаниях приборов. Это, вероятно, следствие отсутствия стандарта на метод. Если обратиться к [1], то обнаружится что результаты измерений твердости по Бринеллю при различных условиях испытаний записываются с соответствующими дополнениями (диаметр шарика, нагрузка, время). Те же данные приводятся и на мерах твердости, а в этом косвенном методе такие большие вольности, которые могут привести к различным результатам измерений на реальных объектах при одинаковых показаниях на мерах твердости.
2.2.4. Анализ граничных условий применимости
Понятно, что датчики с различной энергией удара должны иметь разные, обоснованные границы применимости. Паспортные границы применимости приведены в табл. 3.
Таблица 3. Паспортные границы применимости твердомеров
Характеристики | МЕТ-УД | ТЭМП-3 | ТДМ-2 |
Шероховатость поверхности, Ra, мкм | 3,2 | 2,5 | 2,5 |
Минимальный радиус кривизны, мм | 10 | 15 | 15 |
Минимальная масса объекта контроля, кг | 3 | 1,5 | 3 |
Минимальная толщина объекта контроля, мм | 12 | 6 | 10 |
Поправка на положение датчика | нет | есть | есть |
Логично предположить, что датчик с минимальной энергией удара (МЕТ-УД) должен иметь меньшие пределы по минимальной массе и толщине объекта контроля. Возможно, искусственное увеличение этих границ является маркетинговым ходом, цель которого – привлечение внимания к универсальному твердомеру, использующему два метода измерения твердости. Отсутствие поправки на пространственное положение датчика вызывает недоумение, так как влияние изменения пространственного положения для этого датчика максимально. Шероховатость поверхности Ra 3,2 мкм также не объяснима: при измерении твердости по Бринеллю [1] при значительно больших нагрузках требует подготовки поверхности с шероховатостью не более Ra 2,5 мкм. Чувствительность к наклепу при подготовке поверхности у датчика МЕТ-УД самая высокая, что необходимо учитывать при работе с этим прибором.
Выводы
1. Малогабаритные твердомеры, удобные и незаменимые при решении ряда задач измерения твердости, имеют ряд недокументированных ограничений и особенностей применения.
2. Энергия удара датчиков трех отечественных динамических твердомеров отличается более чем в 4 раза, причем, производители твердомеров не приводят этой характеристики в паспортах и технических описаниях приборов. Это, вероятно, следствие отсутствия стандарта на метод.
3. Динамические датчики с высокой энергией удара (ТДМ-2) имеют некоторое преимущество при контроле конструкционных сталей и сварных соединений. Применение датчиков с низкой энергией удара целесообразно для более тонкостенных и легких объектов, тонких слоев, либо когда нежелательны большие отпечатки на объекте. В других случаях применение датчиков с низкой энергией удара может привести к необходимости увеличения числа замеров для усреднения результатов и излишней чувствительности к наклепу поверхностного слоя, возможному при подготовке поверхности и к изменению пространственного положения.
4. При обнаружении нехарактерных значений твердости отдельных точек необходимо проводить дополнительные измерения вблизи (3… 5 мм) от выпавшей точки, так как причиной может быть не только промах при измерении, но и неоднородности объекта контроля.
5. Диаметр отпечатка от динамических датчиков на стали с твердостью 150 НВ составляет около 0,50 мм для твердомера МЕТ-УД и 0,82 мм для ТДМ-2. Учитывая малую площадь контакта с объектом, при значительной структурной и химической неоднородности объектов контроля (поковки, отливки), превышающей или сравнимой с размером отпечатка, необходимо использовать приборы с большим диаметром шарика и, соответственно, большей энергией удара. Более простое и эффективное решение при единичных измерениях – использование метода Польди [9].
6. Существует диапазон толщины и микроструктуры, в котором использование датчиков с рассмотренными параметрами не обеспечивает корректного подхода к измерению твердости: конструкция имеет недостаточную жесткость для применения динамического датчика, а малая нагрузка импедансного датчика определяет излишнюю локальность зоны воздействия.
7. Для широкого спектра задач контроля твердости целесообразно иметь малогабаритный твердомер не только поддерживающий импедансный и динамический методы. Желательно еще иметь набор датчиков с разными характеристиками – энергией удара и диаметром шарика для динамического датчика и рабочей нагрузкой для импедансного датчика.
8. В случае возникновения разногласий при измерении твердости малогабаритными твердомерами, необходимо сравнивать характеристики датчиков, а в качестве арбитражных методов использовать классические методы измерения твердости.
Литература
1. ГОСТ 9012 – 59 Металлы и сплавы. Методы определения твердости по Бринеллю.
2. ГОСТ 9013 – 59 Металлы и сплавы. Методы определения твердости по Роквеллу.
3. ГОСТ 2999 – 75 Металлы и сплавы. Методы определения твердости по Виккерсу.
4. ГОСТ 4950 – 76 Измерение микротвердости вдавливанием алмазных наконечников.
5. ОСТ5. 9287 – 78 Детали стальные изделий судового машиностроения и приборостроения, термически обработанные. Технические требования, правила приемки и методы испытаний.
6. ГОСТ 22761 – 77 Металлы и сплавы. Методы определения твердости по Бринеллю переносными твердомерами статического действия.
7. Испытание материалов. Справочник под ред. Х. Блюменауэра пер. с нем. 1979., 448 с. М. «Металлургия»
8. ГОСТ 5639 – 82 Стали и сплавы. Метод выявления и определения величины зерна.
9. ГОСТ18661 – 73 Сталь. Измерение твердости методом ударного отпечатка.
10. В. С. Золотаревский. Механические свойства металлов. 1983., 350 с. М. «Металлургия»
Способы измерения твёрдости металла, резины, бетона
Первоисточник статьи - https://vostok-7.ru/articles/tverdost/
Единого общепринятого определения термина «ТВЁРДОСТЬ» не существует поскольку методы определения этой метрологической величины настолько разнообразны, что нет возможности их объединить в одной фразе или описании. При этом даже для одного типа материала (напр. металлов) методов определения твердости существует более 5… Также именно по этой причине приборы для измерения твёрдости именуются не только твердомерами, но и другими названиями, указывающими на метод или материал измерения: дюрометр (для резин), склерометр (для минералов) и т.д.
Лаборатория НТЦ «Эксперт» оказывает услуги по измерению твердости различных деталей. Лаборатория укомплектована твердомерами различных типов и имеет аттестованных специалистов II уровня. По результатам измерений выдается заключение лаборатории неразрушающего контроля или заключение метрологической службы по выбору заказчика. Мы работаем с юридическими и физическими лицами. Проведение работ возможно как лабораторно, так и с выездом.
Твёрдость минералов
Шкала твёрдости минералов Мооса (склерометры царапающие) – метод определения твёрдости минералов путём царапания одного минерала другим минералом для сравнительной диагностики твёрдости минералов между собой по системе мягче-твёрже. Испытываемый минерал либо не царапается другим минералом (эталоном Мооса или склерометром) и тогда его твёрдость по Моосу выше, либо царапается - и тогда его твёрдость по Моосу ниже.
Типы исследуемых материалов:
- минералы (природные и искусственные), в т.ч. измеряется твёрдость камней горных пород
- бетон и другие строительные материалы: твёрдость искусственных камней, плитки, стекла и др.
Молотки Шмидта (склерометры-молотки) – метод определения твёрдости и прочности на сжатие без разрушения строительный материалов: бетона, кирпичей, строительного раствора и пр. Оценка материалов происходит по предварительно установленной градуировочной зависимости между прочностью эталонных образцов и значением отскока бойка молотка Шмидта от поверхности материала.
Типы исследуемых материалов:
- бетон
- кирпич
- строительный раствор
- природные камни и горные породы
Твёрдость металлов
Твёрдость металлов – наиболее глубоко изученное и стандартизированное международной практикой измерение твёрдости. Наиболее распространены следующие методы:
Измерение твёрдости металлов по Бринеллю (твердомеры)
Один из старейших методов, твёрдость определяется по диаметру отпечатка, оставляемому металлическим шариком, вдавливаемым в поверхность. Обозначается HB, где H — Hardness (твёрдость, англ.), B — Brinell (Бринелль, англ.)
Измерение твёрдости металлов по Роквеллу (твердомеры)
Это самый распространённый из методов начала XX века, твёрдость определяется по относительной глубине вдавливания металлического шарика или алмазного конуса в поверхность тестируемого материала. Обозначается HR, где H — Hardness (твёрдость, англ.), R — Rockwell (Роквелл, англ.), а 3-й буквой идёт обозначение типа шкалы, напр. HRA, HRB, HRC и т.д.
Измерение твёрдости металлов по Виккерсу (твердомеры и микротвердомеры)
Самая широкая по охвату шкала, твёрдость определяется по площади отпечатка, оставляемого четырёхгранной алмазной пирамидкой, вдавливаемой в поверхность. Обозначается HV, где H — Hardness (твёрдость, англ.), V — Vickers (Виккерс, англ.).
Измерение твёрдости металлов по Шору (твердомеры и склероскопы)
Данный метод крайне редко используется, твёрдость определяется по высоте отскока бойка от поверхности. Обозначается HS, где H — Hardness (твёрдость, англ.), S — Shore (Шор, англ.), а 3-й буквой идёт обозначение типа шкалы, напр. HSD
Измерение твёрдости металлов по Либу (твердомеры)
Это самый широко применяемый на сегодня метод в мире, твёрдость определяется как отношение скоростей до и после отскока бойка от поверхности. Обозначается HL, где H — Hardness (твёрдость, англ.), L — Leeb (Либ, англ.), а 3-й буквой идёт обозначение типа датчика, напр. HLD, HLC и т.д.
Твёрдость резины
Определить твердость резины сегодня можно несколькими методами:
Измерение твёрдости резины по Шору (твердомеры и дюрометры)
Самый широко применяемый на сегодня метод в мире, твёрдость резины определяется по глубине проникновения в материал специальной закаленной стальной иглы (индентора) под действием калиброванной пружины. Твёрдость резины обозначается в международной практике как H, где H — Hardness (твёрдость, англ.), а 2-й буквой идёт обозначение типа шкалы, напр. HA, HB, HC, HD и т.д., в практике России пишется как «твёрдость по Шору тип А» или «твёрдость по Шору тип D».
Измерение твёрдости по Аскеру (твердомеры и дюрометры)
Это национальный японский метод, сходный с методом измерения твёрдости резины по Шору, но отличающийся от него типом инденторов, пружин и пр. Твёрдость резины обозначается в международной практике как Asker (Аскер, англ.), а далее идёт обозначение типа шкалы, напр. Asker С, Asker D и т.д. В России не применяется.
Измерение твёрдости по Роквеллу (твердомеры)
В этом случае используется стандартный твердомер Роквелла для измерения твёрдости металлов, но вместо индентора-конуса используются инденторы со стальными шариками. Твёрдость резины обозначается HR, где H — Hardness (твёрдость, англ.), R — Rockwell (Роквелл, англ.), а 3-й буквой идёт обозначение типа шкалы, напр. HRP, HRL, HRM или HRE.
Принцип измерения по методу Leeb
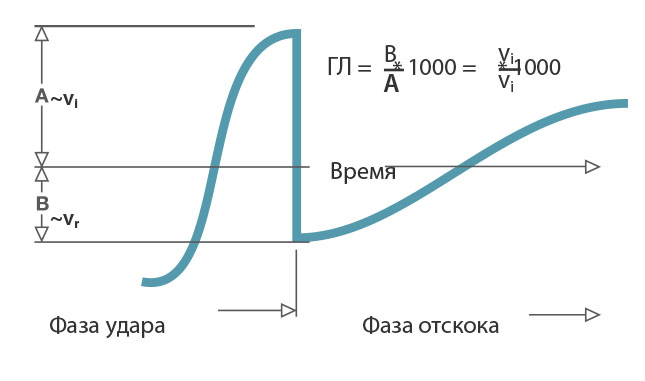
Принцип измерения твердости по Leeb основывается на динамическом методе (отскок). Боек с твердосплавным индентором приводится в движение силой сжатия пружины перпендикулярно поверхности тестируемого образца. Удар о поверхность деформирует поверхность тестируемого образца, и приводит к потере кинетической энергии бойка. Эта потеря энергии определяется путем сравнения скоростей vi и vr бойка на определенном расстоянии от поверхности образца до и после удара о поверхность, соответственно.
Скорости измеряются при помощи постоянного магнита в бойке, который создает индуктивное напряжение в катушке, расположенной в точно заданном месте датчика. Наводимая ЭДС пропорциональна скорости бойка. Дальнейшая обработка сигнала обеспечивает индикацию твердости. Описание динамических твердомеров работающих по методу Leeb здесь.
Шкалы | Приборы | Диапазон | ||
Диапазон измерений |
Сталь и литая сталь | Vickers Brinell Rockwell Shore Rm Н/мм² |
HV HB HRB HRC HRA HS σ1 σ2 σ3 |
81-955 81-654 38-100 20-68 30-99 275-2194 616-1480 449-847 |
Инструментальная сталь холодной обработки | Vickers Rockwell |
HV HRC |
80-900 21-67 |
|
Нержавеющая сталь | Vickers Brinell Rockwell |
HV HB HRB HRC |
85-802 85-655 46-102 20-62 |
|
Чугун, слоистый графит GG | Brinell Vickers Rockwell |
HB HV HRC |
90-664 90-698 21-59 |
|
Чугун, графит шаровидный GGG | Brinell Vickers Rockwell |
HB HV HRC |
95-686 96-724 21-60 |
|
Алюминиевые сплавы | Brinell Vickers Rockwell |
HB HV HRB |
19-164 22-193 24-85 |
|
Медноцинковые сплавы (латунь) | Brinell Rockwell |
HB HRB |
40-173 14-95 |
|
Сплавы CuAI/CuSn (бронза) | Brinell | HB | 60-290 | |
Кованные сплавы меди, низколегированные | Brinell | HB | 45-315 | |
» Другие комбинации можно получить путем пользовательских преобразований | ||||
Требования к тестируемому образцу |
Подготовка поверхности | Шероховатость, класс ISO 1302 | N7 | |
Максимальная глубина шероховатости Rt (мкм/мкдюйм) | 10 / 400 | |||
Средняя шероховатость Ra (мкм/мкдюйм) | 2 / 80 | |||
Минимальная масса образца | Образец (непосредственно) (кг / фунт) | 5 / 11 | ||
На массивной плите (кг / фунт) | 2 / 4,5 | |||
Притертый к плите (кг / фунт) | 0,05 / 0,2 | |||
Минимальная толщина образца | Непритертый (мм / дюйм) | 25 / 0,98 | ||
Притертый (мм / дюйм) | 3 / 0,12 | |||
Толщина поверхностного слоя (мм / дюйм) | 0,8 / 0,03 | |||
Размер отпечатка на контролируемой поверхности | при 300 HV, 30 HRC | Диаметр (мм / дюйм) | 0,54 / 0,021 | |
Глубина (мкм/мкдюйм) | 24 / 960 | |||
при 600 HV, 55 HRC | Диаметр (мм / дюйм) | 0,45 / 0,017 | ||
Глубина (мкм/мкдюйм) | 17 / 680 | |||
при 800 HV, 63 HRC | Диаметр (мм / дюйм) | 0,35 / 0,013 | ||
Глубина (мкм/мкдюйм) | 10 / 400 |
Разработка эталона твердости по Либу второго разряда
Источник: журнал "В мире НК" 2017. Том 20. №1.
Авторы:
Гоголинский Кирилл Валерьевич - директор Всероссийского научно-исследовательского института метрологии имени Д.И. Менделеева (Санкт-Петербург), д.т.н.
Никазов Артём Александрович - аспирант кафедры «Приборостроение» Национального минерального университета «Горный» (Санкт-Петербург).
Рассмотрены технические принципы метода измерения твёрдости по шкалам Либа и текущее состояние метрологического обеспечения метода. В связи с разработкой гармонизированного стандарта и необходимостью реализации метрологической цепи согласно структуре обеспечения прослеживаемости, а также определения и распространения шкал твёрдости рассмотрены и обоснованы методические и технологические решения для реализации стационарного прибора, воспроизводящего метод Либа, для эталона второго разряда. Исходя из проведённого анализа, предложена система измерения скорости на основе двух катушек индуктивности и представлен расчёт её параметров. Приведены результаты испытания макета стационарного прибора, воспроизводящего метод Либа, подтвердившие его соответствие требованиям иностранных стандартов и проекту гармонизированного стандарта.
V. A. Syasko , К. V. Gogolinskiy , A. A. Nikazov
Elaboration of Leeb hardness calibration machine
The article deals with the development of Leeb hardness secondary calibration machine. The article describes the technical principles of the Leeb hardness measurement method and the current state of metrological assurance in the Russian Federation. The analysis of Leeb hardness calibration machines of Germany and Switzerland are con ducted. The draft of metrological traceability (metrological chain) for disseminating of Leeb hardness scales is proposed. In connection with the development of harmonized standard and the need for the implementation of the metrological traceability of Leeb hardness method, as well as the identifying and disseminating of hardness scales, methodological and technological solutions for the Leeb hardness secondary calibration machine are considered. Based on the analysis of required metrological characteristics of secondary calibration machine and hardness reference blocks, the construction of velocity measuring system with two inductors and system parameters calculation with required metrological characters tics are suggested. Test results of Leeb hardness secondary calibration machine layout for HLD scale confirmed its compliance with international standards and the draft of harmonized standard. The obtained results can be used to develop the Leeb hardness secondary calibration machine to equip the standardization and metrology centers of the Russian Federation and abroad.
Применение динамических методов контроля твёрдости, основанных на измерении параметров отскока падающего ударника, получило широкое распространение в последние десятилетия. Преимущества таких методов — малые габариты твердомеров и возможность их использования вне измерительных лабораторий непосредственно на поверхностях деталей, трубопроводах, объектах энергетики и т.д.
Чаще всего в портативных динамических твердомерах реализуется метод измерения твёрдости по Либу, разработанный в Европе в 1970-х гг. сотрудниками фирмы Proceq. Суть метода заключается в измерении соотношения скоростей V падающего ударника до и после соударения с поверхностью испытуемого образца, при этом твёрдость по Либу HL рассчитывается в соответствии с формулой [1] HL = 100VR/VА, где VR — скорость отскока ударника; VA — скорость удара.
На сегодняшний день существует несколько различных шкал твёрдости по Либу для преобразователей, отличающихся радиусом R сферического индентора и массой т ударника, а также его кинетической энергией ЕА при ударе, зависящей от VА.
Метрологическое обеспечение метода Либа в США и Европе регламентируется стандартами: DIN 50156 (части 1, 2 и 3) [2-4], ASTM А956 [5], ISO/DIS 16859 (1-3) [6-8]. До настоящего времени из-за отсутствия стандарта на метод измерения твёрдости по Либу в Российской Федерации динамические твердомеры вносятся в Госреестр средств измерений под видом твердомеров по стандартизованным шкалам статических методов. На практике производители твердомеров, обозначаемых как «динамические», «портативные», «малогабаритные» или «переносные», по сути, реализуют с теми или иными допущениями метод измерения твёрдости по Либу. Ситуация с метрологическим обеспечением динамических методов подробно рассмотрена в [9,10].
В ООО «КОНСТАНТА» разработан проект гармонизированного стандарта на метод измерения твёрдости по Либу на основе стандартов [6-8]. На проект стандарта получены положительные отзывы, в том числе из ФГУП ВНИИФТРИ. Стандарт определяет требования к твердомерам, предназначенным для измерения твёрдости металлов и сплавов по Либу, ударникам, испытуемым образцам, методикам поверки твердомеров, требования к производству и поверке эталонных мер твёрдости, а также требования к эталонам и средствам измерений.
Для реализации метрологической цепи согласно структуре обеспечения прослеживаемости, а также для определения и распространения шкал твёрдости (рис. 1) необходима разработка эталона не только первого, но и второго разряда, для многочисленных центров стандартизации и метрологии (ЦСМ).
Рис. 1. Обобщенная структура обеспечения прослеживаемости (метрологической цепи) для определения и распространения шкал твердости Либа.
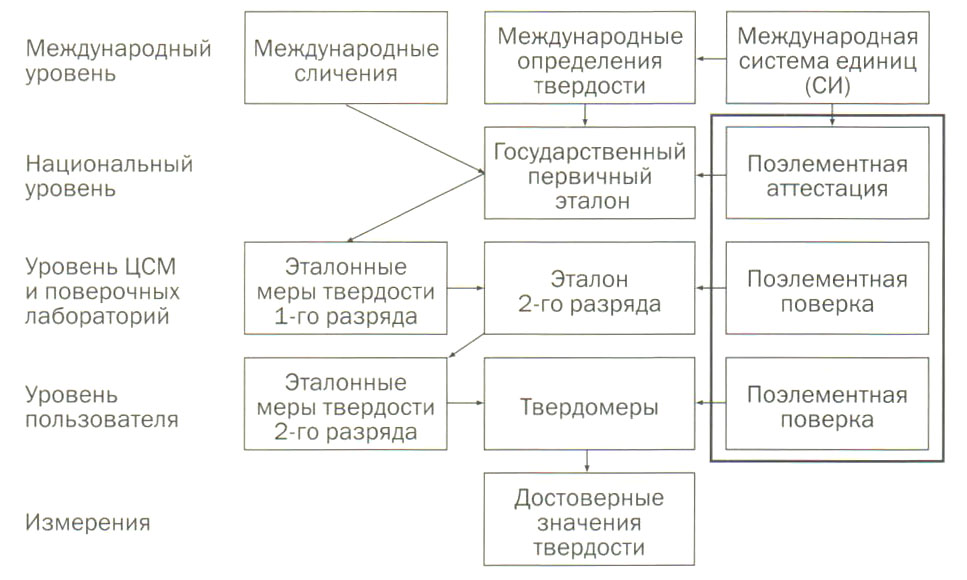
После принятия стандарта должно будет произойти достаточно быстрое увеличение парка твердомеров, реализующих метод Либа, а также мер твердости для их поверки. В связи с этим необходимо будет оснастить большое число ЦСМ эталонами второго разряда, которые должны иметь заданные технические характеристики при минимальной цене, определяемой их себестоимостью. Рассмотрим их возможные конструкции.
Проект стандарта определяет комплект (стационарный прибор, воспроизводящий метод Либа, и комплект средств измерений для поэлементного контроля его параметров) и параметры эталона второго разряда: VA, m, R и материал индентора, проверяемые при поэлементной поверке (табл. 1), а также диапазоны твёрдости и метрологические характеристики при поверке по эталонным мерам твёрдости 1-го разряда. В ударных преобразователях рабочих средств измерений (твердомерах) ударник разгоняется до необходимой скорости при помощи пружины. В известных эталонных установках ударник разгоняется под воздействием гравитационного поля Земли.
Табл. 1. Параметры эталона второго разряда по методу Либа
Параметр | Ед. измерения | Тип ударного преобразователя | ||||||
D | S | E | DL | D+15 | C | G | ||
Скорость удара VА | м/с | 2,05 | 2,05 | 2,05 | 1,82 | 1,70 | 1,40 | 3,00 |
Предельно допустимое отклонение скорости удара | м/с | ±0.0025 | ±0.0025 | ±0.0025 | ±0.0020 | ±0.0020 | ±0.0020 | ±0.0050 |
Масса ударника m | г | 5,45±0,03 | 5,45±0,03 | 5,45±0,03 | 7,25±0,03 | 7,25±0,03 | 3,10±0,03 | 20,00±0,03 |
Радиус сферического наконечника индентора R | мм | 1,500±0,003 | 1,500±0,003 | 1,500±0,003 | 1,390±0,003 | 1,500±0,003 | 1,500±0,003 | 2,500±0,003 |
Материал индентора | WC-Co* | с** | PCD*** | WC-Co | WC-Co | WC-Co | WC-Co | |
Твердость индентора по Виккерсу | HV2 | 1600 ± 50 | 1600 ± 50 | >4500 | 1600 ± 50 | 1600 ± 50 | 1600 ± 50 | 1600 ± 50 |
* Вольфрам-карбид кобальта ** Керамика *** Поликристаллический алмаз |
Табл. 2. Диапазоны твердости по Либу и метрологические характеристики эталонов второго разряда при поверке по эталонным мерам твердости первого разряда.
Тип ударного преобразователя | Диапазоны твердости, HL* | Минимальная повторяемость, % | Предельная погрешность, % | |||||
D, D + 15 | <500 500-700 >700 |
1,0 1,0 1,0 |
±2,0 ±1,5 ±1,0 |
|||||
DL, S | <700 700-850 >850 |
1,0 1,0 1,0 |
±2,0 ±1,5 ±1,0 |
|||||
С, Е | <600 600-750 >750 |
1,0 1,0 1,0 |
±2,0 ±1,5 ±1,0 |
|||||
G | <450 450-600 >600 |
1,0 1,0 1,0 |
±2,0 ±1,5 ±1,0 |
|||||
*HLD для ударных преобразователей типа D; HLD+15 для ударных преобразователей типа D+15; HLDL для ударных преобразователей типа DL; HLS для ударных преобразователей типа S; HLC для ударных преобразователей типа С; HLE для ударных преобразователей типа Е; HLG для ударных преобразователей типа G. |
Известны две реализации эталонных установок, принципиально отличающихся способом измерения скорости ударника: на основе лазерного интерферометра и на основе катушки индуктивности.
Система измерения скорости на основе лазерного интерферометра используется в эталоне, разработанном в Германии (рис. 2). Установка реализует непрерывное измерение скорости движения ударника в процессе падения и отскока. Для измерения используется лазерный интерферометр на базе He-Ne-лазера фирмы SIOS Messtechnik GmbH, который имеет стабилизированную частоту излучения. В данной конструкции форма ударников отличается от применяемых в твердомерах, так как они должны обеспечивать отражение луча интерферометра.
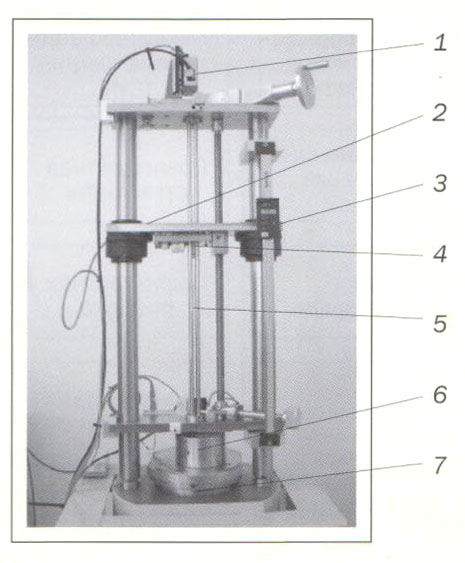
Рис. 2. Структура и техническая реализация эталона на основе интерферометра:
- лазерный интерферометр,
- система позиционирования высоты сброса ударника,
- цифровая линейка,
- ударник,
- направляющие стержни,
- мера твердости,
- стол.
Система измерения скорости с катушкой индуктивности реализована в эталоне, разработанном на базе твердомера Equotip 3 (рис. 3). В системе используется катушка индуктивности и ударник с постоянным магнитом в корпусе, аналогичный рабочим средствам измерения швейцарского производителя. Ударник с встроенным магнитом, пролетая сквозь катушку индуктивности со скоростью VА при падении, наводит в ней ЭДС, амплитудой ЕА. При отскоке, двигаясь через катушку вверх со скоростью VR, наводит в ней ЭДС амплитудой ER противоположной полярности (рис. 4). В рамках работы над стандартом был разработан макет стационарного прибора, воспроизводящего метод Либа, для эталона второго разряда. Для решения задачи измерения скорости была выбрана система с использованием катушек индуктивности. Согласно стандартам для вычисления кода Либа используется отношение скоростей удара и отскока, однако в рабочих средствах измерений, в соответствии с теми же стандартами, расчёт кода по Либу выполняется по формуле: HL = 100 ЕR/ЕА.
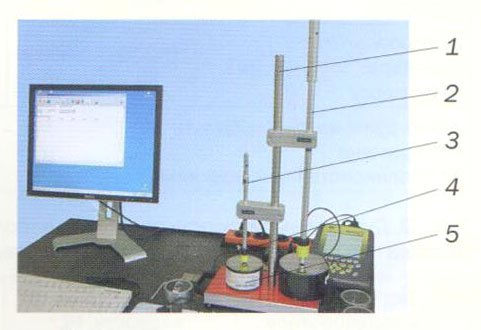
Рис. 3. Эталон на базе твердомера Equotip 3 фирмы Proceq (Швейцария):
- несущая стойка,
- направляющая трубка для датчика типа D,
- направляющая трубка для датчика типа G,
- катушка индуктивности,
- мера твердости.
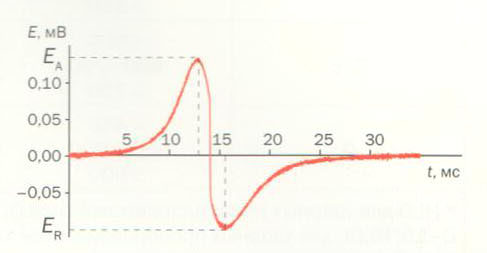
Рис. 4. Диаграмма ЭДС, наведенной на катушке индуктивности при измерении твердости.
На взгляд авторов система с катушкой индуктивности является предпочтительной ввиду того, что она аналогична технологическому решению, используемому в рабочих средствах измерений. При этом для измерения VA предлагается установка дополнительной катушки индуктивности.
Система измерения VA (рис. 5) состоит из двух катушек L1 и L2, расположенных друг от друга на расстоянии ∆h. ЭДС с катушек поступают через измерительные усилители на входы аналого-цифровых преобразователей микроконтроллера, вычисляющего значение скорости.
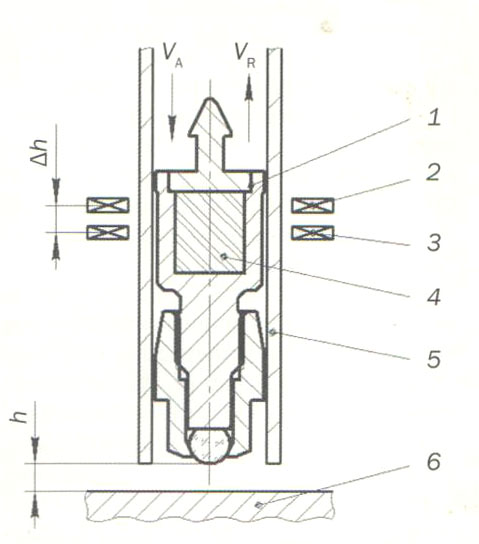
Рис. 5. Структура системы измерения VA с двумя катушками индуктивности:
- ударник,
- дополнительная катушка L1,
- основная катушка L2,
- постоянный магнит ударника,
- направляющая трубка,
- испытуемый образец.
Расчеты показали, что для ударника типа D VA =2,05±0,0025 м/с обеспечивается при сбросе свободно падающего ударника с высоты H = 214±0,26 мм.
Скорость ударника должна измеряться при h не более 2 мм. После прохождения катушки L2 со скоростью V скорость ударника продолжает линейно увеличиваться до требуемой скорости VA = V + gt.
При этом h = t(VA + V)/2.
Время t прохождения расстояния h может быть найдено из решения квадратного уравнения: h = t(VA+V)/2 = t(VA + VA - gt)/2 = VAt - gt2/ 2;
откуда gt2 - 2 VAt + 2h = 0
и t=[VA- (VA2 - 2hg)1/2]/ g=[2,05 - (2,052- 2*0,002*9,819)1/2]/9,819≈ 0,978 мс.
Для обеспечения требуемых характеристик необходимо контролировать фактическую скорость и высоту h. Выполнить это можно по фиксации моментов прохождения ударником катушек L1 и L2, соответствующих амплитудам EА1 и ЕА2 (рис. 4). Фиксация t1 выполняется по пику ЭДС при прохождении катушки L1, а фиксация t2 — при прохождении катушки L2 на расстоянии ∆h между ними. Параметры определяются из решения системы уравнений:
h = VAt1+gt12/2;
h + ∆h = VAt2+gt22/2.
Расстояние между измерительными катушками ∆h = VA(t2 – t1) +g(t22 – t12)/2.
Скорость в момент удара:
VA = [∆h - g(t22 – t12)/2]/(t2 – t1).
С учётом того, что ∆t=t2-t1, имеем: VА=(∆h/∆t)-g(t12 + ∆t/2).
На точность вычисления скорости влияют погрешности измерения ∆h и ∆t. Чувствительность к вариации ∆h: SVA(∆h) = d(V0)/d(∆h) = (1/∆t).
При допустимой погрешности задания расстояния между катушками от истинного значения δ∆h погрешность измерения скорости VA составит: ∆VA=SVA(∆h)* δ∆h = δ∆h/∆t.
Допустимое отклонение скорости определено стандартом: ∆VA = ±2,5 мм/с. Тогда предельно допустимая погрешность задания расстояния между катушками: δ∆h= ∆VA ∆t.
Чувствительность к погрешности измерения времени движения ударника после пика ЭДС:
SVA(t1) = d |VA | /d(t1) = d | [∆h/(t2 – t1)] - g [t1 + (t2 - t1)/2] | /d(t1) = ∆h/∆t2+g/2;
SVA(t2) = d | VA | /d(t2) = d | [∆h/(t2 – t1)]- g [t1 + (t2 - t1)/2] | /d(t2) = ∆h/∆t2 + g/2.
Общая чувствительность к погрешности измерения времени с учётом равной вероятности знака погрешности:
SVA(t)= ISVA(t1) I+ ISVA(t2)l = 2∆h/∆t2+g.
При допустимой погрешности измерения времени δ1 погрешность измерения скорости VA составит:
∆VA = SV0(t) δ1 = (2∆h/∆t2+g) δ1.
Так как ∆VA = ±2,5 мм/с, то предельно допустимая погрешность измерения времени δ1 = ∆VA /(2∆h/∆t2 + g) = ∆VA∆t2/(2∆h + g∆t2).
Анализ показывает, что оцифровка ЭДС с выходов катушек должна производиться с частотой fкв = 1 МГц. При этом определение моментов t1 и t2, соответствующих пикам ЭДС. а также момента удара должны производиться после оцифровки ЭДС с полосой пропускания 100 кГц. Расстояние ∆h = 1 мм должно быть обеспечено с погрешностью не хуже ±10 мкм.
По результатам проведённой работы был разработан макет стационарного прибора, воспроизводящего метод Либа, для эталона твёрдости второго разряда по шкале D, параметры которого приведены в табл. 3. Катушки индуктивности L1 и L2 имели следующие размеры: внутренний диаметр 12 мм, внешний диаметр 17 мм, длина намотки 0,5 мм.
Табл. 3. Параметры макета эталона твердости по Либу второго разряда (по шкале D)
Параметры | Ед. измерения | Значения |
Скорость удара, VA | м/с | 2,05 ±0,0025 |
Высота сброса ударника | мм | 214 ±0,26 |
Масса ударника, m | г | 5,45 ±0,03 |
Радиус сферического индентора, R | мм | 1,5 ±0,003 |
Материал индентора | WC-Co | |
Твердость индентора по Виккерсу | HV2 | 1600 ±50 |
Частота оцифровки ЭДС | МГц | 1 |
Расстояние между катушками, ∆h | мм | 1±0,01 |
Расстояние h | мм | <2 |
Предварительные испытания макета эталона были произведены с использованием комплекта мер твёрдости HLD491.5. HLD608 и HLD770, изготовленных компанией Proceq и поверенных в Physikalisch-Technische Bundesanstalt (РТВ). При измерениях на мерах ∆VA < ±2,5 мм/с. Результаты измерений представлены в табл. 4.
Табл. 4. Результаты экспериментов
Шкала твердости | HLD | |||
Твердость эталонной меры твердости, ед.тв. | 491,5 | 608 | 770 | |
Показания прибора, ед.тв. | 1 | 484 | 600 | 770 |
2 | 487 | 599 | 765 | |
3 | 489 | 601 | 766 | |
4 | 488 | 605 | 766 | |
5 | 490 | 605 | 767 | |
6 | 483 | 607 | 769 | |
7 | 484 | 603 | 761 | |
8 | 485 | 604 | 762 | |
9 | 486 | 607 | 759 | |
10 | 487 | 605 | 761 | |
Среднее значение показаний, ед.тв. | 487 | 604 | 764 | |
Абс. погрешность, ед.тв. | 5 | 4 | 6 | |
Размах показаний, ед.тв. | 5 | 2 | 1 | |
СКО | 2,3 | 2,8 | 3,3 | |
Повторяемость, % | 0,5 | 0,5 | 0,4 | |
Предельная погрешность, % | 0,97 | 0,72 | 0,78 |
Выполненные эксперименты с использованием разработанного макета стационарного прибора, воспроизводящего метод Либа, показали, что предложенные технические решения могут быть положены в основу при разработке эталона твёрдости по Либу второго разряда для центров стандартизации и метрологии.
Литература
- Leeb D. New dynamic method for hardness testing of metallic materials. — In: VDI-Report №308,1978. pp. 123-128.
- DIN 50156-1:2007/Metallic materials — Leeb hardness test — Part 1: Test Method.
- DIN 50156-2:2007/Metallic materials — Leeb hardness test — Part 2: Verification and calibration of the testing devices.
- DIN 50156-3:2007/Metallic materials — Leeb hardness test — Part 3: Calibration of reference blocks.
- ASTM A956/Standard Test Method for Leeb Hardness Testing of Steel Products. 2012.
- ISO/DIS 16859-l:2015/Metallic materials — Leeb hardness test — Part 1: Test method.
- ISO/DIS 16859-2:2015/Metallic materials — Leeb hardness test — Part 2: Verification and calibration of the testing devices.
- ISO/DIS 16859-3:2015/Metallic materials — Leeb hardness test — Part 3: Calibration of reference test blocks.
- Гоголинский К. В., Сясько В. А. Метрологическое обеспечение динамических методов измерения твёрдости в Российской Федерации: существующие проблемы и пути их решения. — В мире НК. 2014. № 1 (63). С. 69-76.
- Потапов А.И., Сясько В.А.. Гоголинский К. В., Никазов А. А. Обеспечение единства измерений твёрдости динамическим методом в Российской Федерации. — Контроль. Диагностика. 2016. № 12. С. 44-50.
Источники излучения для промышленного радиационного контроля можно условно разделить на рентгеновские аппараты и гамма-дефектоскопы, использующие в качестве источника излучения радионуклид вместо рентгеновской трубки. Каждый тип имеет свои достоинства и недостатки и более применим в конкретной области НК. Рентгеновские аппараты в общем виде можно классифицировать на аппараты постоянного и действия и импульсные. Импульсные рентгеновские аппараты как правило дешевле, легче и проще в управлении. Аппараты с постоянным напряжением дороже, но при этом долговечней и обеспечивают лучшее качество снимков.
Основным документом, регулирующим правила аттестации и основные требования к лабораториям неразрушающего контроля, является СДАНК-01-2020, в соответствии с положениями данного норматива выделяются общие и специальные требования к лабораториям НК, а так же требования к оборудованию и специалистам лаборатории.
II. Статус, административная подчиненность и структура ЛНК
2.1. ЛНК может быть юридическим лицом или подразделением юридического лица, которые несут юридическую ответственность за ее деятельность. ЛНК может быть организована физическим лицом (индивидуальным предпринимателем), осуществляющим свою деятельность в установленном законодательством порядке.
2.2. Деятельность ЛНК структурируется и управляется таким образом, чтобы обеспечивалась беспристрастность.
2.3. Статус, административная подчиненность и структура ЛНК обеспечивают объективность результатов контроля, исключают возможность любого воздействия на сотрудников лаборатории с целью оказать влияние на результаты контроля.
2.4. ЛНК несет ответственность за беспристрастность своей деятельности и не допускает коммерческое, финансовое или иное давление, ставящее беспристрастность под угрозу:
2.4.1. ЛНК, имеющая статус юридического лица или индивидуального предпринимателя, удовлетворяет следующим критериям беспристрастности:
- независима от сторон, заинтересованных в результатах НК;
- не участвует в разработке, изготовлении, строительстве, монтаже, ремонте, реконструкции и эксплуатации или не является покупателем, собственником, потребителем объектов, НК которых осуществляет.
2.4.2. ЛНК, являющаяся структурным подразделением юридического лица или индивидуального предпринимателя, удовлетворяет следующим критериям беспристрастности:
- в рамках организационной структуры четко разграничены функциональные обязанности по осуществлению НК, а также установлена отчетность лаборатории перед руководством юридического лица или индивидуального предпринимателя, структурным подразделением которых она является;
- персонал ЛНК не участвует в разработке, изготовлении, строительстве, монтаже, ремонте, реконструкции и эксплуатации объектов, НК которых осуществляет;
- лаборатория не выполняет работы, которые могут повлиять на объективность результатов НК.
2.5. ЛНК идентифицирует и минимизирует риски для своей беспристрастности на постоянной основе. Это включает риски, которые возникают в процессе ее деятельности, в результате ее отношений или отношений ее персонала.
Примечание. Отношения, которые угрожают беспристрастности ЛНК, могут основываться на праве собственности, управлении, руководстве, персонале, финансах, договорах, маркетинге или на других видах стимулирования в отношении заказчиков и т.п.
III. Помещения и специальные требования для НК
3.1. Помещения ЛНК (размещение персонала, места проведения НК, архив и фонд НТД, хранение и эксплуатация технических средств) по производственной площади, характеру и объему выполняемых работ и окружающая среда при проведении контроля вне помещения должны соответствовать методическим документам по НК и условиям эксплуатации средств НК.
Помещения по месту (местам) осуществления деятельности лаборатории (в том числе по месту осуществления временных работ) должны находиться в собственности юридического лица или индивидуального предпринимателя или использоваться на ином законном основании, предусматривающем право владения и пользования.
Лаборатория может проводить НК по месту осуществления временных работ, если в соответствии с документами по НК работы проводятся за пределами места (мест) осуществления деятельности лаборатории, но с использованием средств НК, а также иных технических средств и материальных ресурсов, соответствующих требованиям раздела V настоящих Правил.
3.2. При НК с использованием источников ионизирующего излучения (ИИИ) обеспечивается выполнение требований по радиационной безопасности, установленных Федеральным законом от 9 января 1996года №3-ФЗ «О радиационной безопасности населения», требований по защите людей от вредного радиационного воздействия ИИИ, установленныхСанПиН2.6.1.2523-09 «Нормы радиационной безопасности (НРБ-99/2009)» (зарегистрированы Министерством юстиции Российской Федерации 14 августа 2009 года, регистрационный №14534).
3.2.1. Деятельность по НК с использованием ИИИ осуществляется при наличии у юридического лица или индивидуального предпринимателя санитарно-эпидемиологического заключения и специального разрешения (лицензии) на право осуществления этой деятельности, выданных уполномоченными на это органами.
При создании временных хранилищ источников излучения вне территории организации, в том числе для гамма-дефектоскопических аппаратов, используемых в полевых условиях, необходимо иметь санитарно-эпидемиологическое заключение о соответствии условий работы с источниками излучения (физическими факторами воздействия на человека) санитарным правилам.
3.2.2. Получение и передача источников ионизирующего излучения и содержащих их изделий, за исключением источников, освобожденных от необходимости оформления лицензии, разрешается только для юридических лиц или индивидуальных предпринимателей, имеющих лицензию на деятельность в области использования ИИИ, с обязательным информированием органов, осуществляющих федеральный государственный санитарно-эпидемиологический надзор по месту нахождения как передающего, так и принимающего ИИИ юридического лица или индивидуального предпринимателя.
3.3. Лаборатория, выполняющая работы по НК вне мест ее постоянного размещения, на временных или передвижных площадях и на объектах заказчика (в полевых условиях), должна подтвердить возможность надежной доставки средств НК к объекту с соблюдением требований радиационной безопасности и обеспечить проверку средств НК перед использованием после транспортировки.
V. Средства НК
5.1. ЛНК оснащается собственными средствами НК, обеспечивающими возможность выполнения работ по НК в рамках ее области аттестации.
Для проведения отдельных видов работ допускается использование оборудования, материалов, принадлежностей, принадлежащих другим юридическим или физическим лицам с условием (для средств измерений) их поверки(калибровки)и наличия документов, подтверждающих право владения и пользования.
5.2. Номенклатура средств НК определяется действующей нормативной технической и методической документацией по НК, распространяющейся на объекты контроля, виды (методы) НК и виды деятельности, при осуществлении которых проводится НК.
5.3. Каждое средство НК, которое имеется в лаборатории, включая и настроечные (контрольные) образцы, регистрируется в ЛНК. Сведения о средствах НК вносятся в Паспорт лаборатории и в регистрационные документы (учетный лист, карточка).
Сведения о средствах НК включают данные о:
- наименовании, типе средства НК;
- стране, заводе-изготовителе (фирме),заводском и инвентарном номере, годе выпуска, дате ввода в эксплуатацию;
- техническом обслуживании, ремонтах;
- поверке, калибровке, аттестации;
- местонахождении паспорта и (или) руководства по эксплуатации, методических указаний по поверке (если они входят вкомплект поставки прибора);
- свидетельствах (протоколах, сертификатах) поверки, калибровки, аттестации;
- перечне комплекта поставки прибора, если он не входит в состав других документов.
5.4. Сведения о средствах НК других организаций, индивидуальных предпринимателей и физических лиц, применяемых в лаборатории, вносятся в Паспорт лаборатории. При этом указывается срок, в течение которого лаборатория имеет право использовать не принадлежащее ей средство НК.
5.5. Средства НК, относящиеся к средствам измерения (дефектоскопы, преобразователи, меры и т.п.), поверяются или калибруются в установленном порядке.
5.6. В ЛНК имеются документированные процедуры технического обслуживания и проверки технического состояния используемых средств НК, а также графики поверки, калибровки, аттестации, технического обслуживания и проверки технического состояния собственных и временно привлеченных средств НК.
5.7.Каждая партия материалов для НК (порошки, суспензии, пенетранты, радиографические пленки, химические реактивы) до начала применения подвергаются входному контролю с оформлением отчетного документа, при котором проверяются: наличие на каждом упаковочном месте (пачке, коробке, емкости) этикеток (сертификатов), полнота приведенных в них данных и соответствие этих данных требованиям стандартов или технических условий на контролируемые материалы (при изготовлении реактивов и пенетрантов для собственных нужд проверяются только наличие этикетки и наименование реактива или пенетранта; отсутствие повреждений упаковки и материалов; срок годности; соответствие материалов применяемому методу (виду) НК.
VI. Персонал ЛНК
6.1. ЛНК имеет:
- руководителя лаборатории (при необходимости, технического руководителя, заместителей руководителя, заместителей технического руководителя), отвечающих в полном объеме за организацию, выбор видов (методов)и проведение работ по НК;
- аттестованный в независимых органах по аттестации системы НК персонал, имеющий соответствующую профессиональную подготовку, теоретические знания и практический опыт, необходимые для выполнения работ по НК (аттестация персонала в совокупности включает все виды (методы) и объекты НК, которые закреплены за лабораторией и входят в область ее аттестации).
Руководители юридических лиц и индивидуальные предприниматели, в состав которых входят лаборатории НК, руководители (технические руководители, их заместители) лабораторий (подразделений, осуществляющих НК) проходят подготовку и аттестацию в области промышленной безопасности в объеме вопросов и требований, необходимых для исполнения ими трудовых обязанностей в соответствии с требованиями пунктов 1 и 2 статьи 14.1 Федерального закона от 21 июля 1997г. № 116-ФЗ «О промышленной безопасности опасных производственных объектов». Иные работники лабораторий (дефектоскописты) проходят проверку знаний утвержденной в лаборатории документации, устанавливающей порядок и технологию производства работ по НК в соответствии с областью деятельности, характером и объемом выполняемых лабораторией НК работ.
Работниками лаборатории, непосредственно выполняющими работы по НК в области аттестации, состоящими в штате по основному месту работы, должно обеспечиваться проведение НК по не менее чем половине включенных в область аттестации объектов и видов (методов) НК.
Весь персонал лаборатории, как постоянный, так и привлекаемый, который может повлиять на деятельность лаборатории, действует беспристрастно, компетентен и работает в соответствии с системой менеджмента лаборатории.
6.2. Руководитель и технический руководитель лаборатории (заместители руководителя, технического руководителя), лица, ответственные за радиационную безопасность, систему менеджмента назначаются из числа сотрудников организации, работа для которых в данной организации является основной. В соответствии со статьей 66 Трудового кодекса Российской Федерации.
6.3. К работе с источниками излучения (в т.ч. гамма-дефектоскопическими и рентгеновскими дефектоскопами) допускаются лица не моложе 18 лет, не имеющие медицинских противопоказаний, отнесенные приказом руководителя к категории персонала группы А, прошедшие обучение по правилам работы с источником излучения (гамма-дефектоскопическими и/или рентгеновскими дефектоскопами) и по радиационной безопасности, и соответствующий инструктаж в соответствии с установленными требованиями.
6.4.В лаборатории обеспечиваются обучение, профессиональная подготовка, повышение квалификации, мероприятия по оценке опытности, ведется постоянный учет сведений об обучении, аттестации, повышении квалификации и профессиональном опыте каждого сотрудника, выполняющего НК.
Лаборатория устанавливает необходимые этапы подготовки каждого сотрудника, включающие:
- период официального введения в должность;
- период работы под наблюдением опытных сотрудников;
- постоянную подготовку на протяжении служебной деятельности.
6.5. Все сотрудники лаборатории имеют должностные инструкции, утвержденные руководителем юридического лица или индивидуальным предпринимателем (или назначенным ими лицом) и определяющие их служебные обязанности и связанную с ними ответственность. В случае применения новой техники и технологий, изменений в организации труда, изменения правовых актов и нормативных документов должностные инструкции пересматриваются в установленном в лаборатории порядке. В лаборатории ведутся записи, подтверждающие ознакомление персонала с должностными инструкциями.
6.6. В лаборатории назначаются лица, отвечающие за определенные участки работ, в частности за:
- хранение, проверку технического состояния, техническое обслуживание, эксплуатацию и метрологическое обеспечение средств НК;
- ведение фонда нормативных технических и методических документов;
- подготовку заключений (отчетов, протоколов, актов) о результатах НК, их проверку и утверждение;
- функционирование системы менеджмента;
- ведение и хранение документации по результатам НК;
- радиационную безопасность, учет и хранение источников ионизирующих излучений.
VII. Документация ЛНК
Перечень необходимых документов смотрите в разделе Перечень документов необходимых для аттестации лаборатории НК
Смотрите так же разделы:
Аттестация лабораторий неразрушающего контроля
Аттестация специалистов неразрушающего контроля
Перечень оборудования необходимого для аттестации лаборатории НК
Перечень документов необходимых для аттестации лаборатории НК
Частые вопросы по аттестации лабораторий НК
Цена услуг по аттестации лабораторий (калькулятор)
На сегодняшний день тепловизоры являются оптимальным инструментом неразрушающего теплового контроля в самых разных отраслях промышленности. Основные сферы применения промышленных тепловизоров это тепловой аудит объектов строительства, поиск неисправности электросетей, мониторинг производственных процессов и другие случаи, когда по неоднородности теплового поля можно судить о техническом состоянии контролируемых объектов.
Использование тепловизоров дает возможность выявить потенциально проблемные участки для проведения превентивного обслуживания, значительно сокращая дальнейшие затраты по эксплуатации. Ниже описаны наиболее востребованные направления современной строительной и промышленной термографии.
В строительстве одним из основных направлений теплового контроля является общий энергоаудит зданий и сооружений с целью оптимизации расходов на энергию. Проведение инспекции здания с последующим анализом его особенностей и данных о расходе энергии позволяет определять оптимальные способы снижения энергопотерь. Использование тепловизора для контроля строительных объектов имеет ряд преимуществ, одним из которых является возможность распознать причины потерь тепла, оценить их масштабы, и предпринять меры по их сокращению.
На объектах строительства тепловизор позволяет обнаружить различные дефекты кирпичной кладки и ограждающих конструкций, являющихся причиной утечки тепла. Термически слабые участки конструкций. проявляют себя через так называемые тепловые мостики которые тепловизор четко регистрирует. Полученная в результате контроля термограмма может служить доказательством производственного брака или некачественного проектирования.
Среди дефектов ограждающих конструкций, увеличивающих теплопотери, одними из самых распространенных является проблема с окнами. Дефекты оконных конструкций могут стать причиной повышенного шума, сквозняков, запотевания и сырости. Высокая чувствительность современных тепловизоров позволяет выявить даже минимальные перепады температуры, определяя места имеющихся дефектов для их последующего ремонта.
Еще одним направлением строительной термографии является тепловизионный контроль систем отопления, вентиляции и кондиционирования. Здесь частыми причинами энергопотерь могут быть ошибки проекта, нарушение правил эксплуатации, складирования и перевозки. Давая возможность в выявить участки с аномальным распределением температуры, результаты теплового контроля позволяют судить о правильности монтажа и наладке инженерных коммуникаций.
Среди других направлений тепловизионного контроля в строительстве, можно выделить, поиск мест проникновения влаги, поиск трубопроводов горячей и холодной воды и мест их разрывов.
Дополнительная информация
Статья - диагностика строительных конструкция методом инфракрасной термографии
Статья - комплексный тепловой контроль зданий и строительных сооружений
Статья - Оценка фактической теплозащиты зданий методом теплового контроля
Каталог Строительная термография Testo
ГОСТ Р 54852-2011 "Здания и сооружения. Метод тепловизионного контроля качества теплоизоляции ограждающих конструкций"
СНИП 2302-2003 "Тепловая защита зданий"
СНИП 2301-99 "Строительная климатология"
![]() |
![]() |
![]() |
В промышленном производстве основной целью теплового неразрушающего контроля является обнаружение дефектов оборудования на их ранней стадии. Аномальный нагрев, механических компонентов, часто может указывать на чрезмерную нагрузку, и риск выхода системы из строя. Использование промышленных тепловизоров дает возможность выявить проблемные участки для их превентивного обслуживания, значительно сокращая дальнейшие затраты по эксплуатации.
Современные тепловизоры применяются в самых разных отраслях промышленного производства. Среди наиболее распространенных направлений теплового контроля можно выделить превентивную диагностику промышленного оборудования, контроль заполнения резервуаров, поиск неисправности электросетей, мониторинг солнечных батарей, анализ критических температур на печатных платах и другие случаи, когда полученная термограмма дает возможность судить о техническом состоянии контролируемых объектов.
К типовым объектам тепловизионного контроля в промышленном производстве можно отнести станки, конвейеры, турбины, компрессоры, насосы, генераторы, ДВС, системы нагрева и охлаждения, различное гидравлическое оборудование.
Дополнительная информация
Статья - Тепловизионное обследование металлургических печей
Статья - Тепловизионное обследование дымовых труб
Практическое руководство по промышленной термографии
Каталог промышленная термография
![]() |
![]() |
![]() |
В работе предприятий энергетического сектора, основными направлениями теплового контроля является поиск перегретых участков электросетей, дымовых труб, паровых и водогрейных котлов. Тепловизоры также часто применяются для поиска неисправностей в теплоизоляции трубопроводов и турбин, определения мест подсоса холодного воздуха, для проверки эффективности работы систем охлаждения трансформаторов, двигателей, линий электропередач и другого оборудования.
К типовым объектам тепловизионного контроля в сфере энергетики можно отнести всевозможные конденсаторы, рубильники, распределительные щиты, места контактных соединений электропроводки, трансформаторы, генераторы, батареи, бойлеры, паровые системы и другое оборудование.
Отдельным направлением тепловизионного контроля в энергетике, является мониторинг солнечных энергосистем, который проводится для обеспечения безопасности и анализа эксплуатационных показателей. В современных тепловизорах предусмотрена возможность ввода показателя интенсивности солнечного излучения, которое сохраняется вместе с тепловыми снимками в в дальнейшем может быть использовано для анализа результатов контроля.
Практическое примениние тепловизоров для теплового контроля объектов энергетики
Статья - Тепловизионное обследование дымовых труб
Подробнее о применении тепловизоров в энергетике
РД 153-34.0-20.363-99 «Основные положения метода инфракрасной диагностики электрооборудования и высоковольтных линий
![]() |
![]() |
![]() |
В нефтегазовом комплексе тепловизоры нашли свое применение при контроле наполняемости резервуаров, позволяя дистанционно определять температуру и уровень жидкости, делая этот процесс максимально быстрым и безопасным (при отказе систем автоматического оповещения). Тепловизоры также применяются для контроля систем противопожарной защиты, систем резервуарного парка, таких как трубопроводы и электрооборудование, позволяя дистанционно выявлять места критического изменения температур. При использовании тепловизоров, контроль магистральных трубопроводов возможен с высоты до 500 метров и скоростью полета до 300 км/ч
В химической промышленности тепловизор решает похожие задачи, что и в нефтегазовом секторе, а именно проверка уровня жидкости резервуаров, диагностика герметичности и изоляции емкостей, общий мониторинг температуры веществ. Важным преимуществом тепловизионного контроля в химической отрасли является очень низкий уровень теплового воздействия, кроме того, использование тепловизора возможно как в стационарном режиме, так и в процессе работы установок. Быстрота и достоверность результатов теплового контроля позволяют оперативно реагировать на протекание химических процессов.
Дополнительная информация
Статья - Опыт применения теплового контроля в нефтепереработке
Практическое руководство по промышленной термографии
![]() |
![]() |
![]() |
В сфере электроники и электротехники тепловизоры позволяют оценить уровень нагрева в системах низкого, среднего и высокого напряжения. Полученные термограммы дают возможность своевременно обнаружить неисправные компоненты и предпринять меры по их ремонту.
В процессе контроля электротехнического оборудования, важным плюсом тепловизоров является бесконтактный характер их применения. Кроме того, контроль с использованием тепловизора не требует прекращения рабочих процессов на время его проведения. Полученная термограмма дает информацию о состоянии объектов, тепловой контроль которых без применения тепловизоров невозможен или сильно затруднен, например, в случае с кабелями, проложенными в технических рукавах и потолочных нишах.
Среди основных направлений теплового контроля в сфере электротехники можно выделить контроль систем распределения электроэнергии (трехфазные системы, распределительные щиты, предохранители, электропроводка, подстанции, измерительные лаборатории), контроль электромеханического оборудования (электродвигатели, насосы, вентиляторы, подшипники, коробки передач и конвейеры), контроль промышленных контрольно-измерительных приборов (контроллеры, трубы, клапаны, конденсационные баки и резервуары и прочее).
Дополнительная информация
Подробнее о применении тепловизоров в электронике
РД 153-34.0-20.363-99 «Основные положения метода инфракрасной диагностики электрооборудования и высоковольтных линий
![]() |
![]() |
![]() |
Технология SuperResolution
Специалисты во многих отраслях промышленности часто сталкиваются с необходимостью теплового контроля мелких и удаленных объектов. Контроль таких объектов требует высокого разрешения, недоступного в тепловизорах начального и среднего уровня. Применение же моделей с высоким разрешением (640x480) часто бывает ограничено бюджетом организации.
Данная проблема особенно актуальна в области микроэлектроники, где требуются термограммы с максимально высоким разрешением. С аналогичными трудностями также можно столкнуться в области энергетики и строительства, где объекты контроля могут находиться на расстоянии нескольких метров, например крыши зданий и линии электропередач.
Разработанная компанией Testo технология SuperResolution дает возможность улучшить пространственное разрешение тепловых снимков в 1,6 раза а количество температурных точек в 4 раза позволяя получить термограмму сравнимую по качеству с детектором более высокого класса.
При создании термограмм SuperResolution, используется комбинация двух технологий – метод супервыборки и метод обратной свёртки или деконволюции. Благодаря синтезу этих методов, использование естественного движения руки в процессе контроля, является основой для создания серии снимков, из которых комбинируется термограмма с улучшением пространственного разрешения в 1,6 раза. Обработка термограммы происходит в режиме реального времени и занимает примерно 0,5 секунды.
Говоря более простым языком, при использовании технологии SuperResolution, тепловизор делает не один а сразу четыре снимка. Из-за естественных колебаний руки все четыре изображения получаются уникальными. Далее программы IRSoft проводит анализ и выдает итоговое изображение с разрешением, в два раза выше, чем у исходников.
Необходимо отметить, что для создания снимков технология SuperResolution использует реальные температурные значения без использования процесса интерполяции, при котором создаются искусственные промежуточные значения температур без дополнительных сведений. Такие искусственно сгенерированные значения не могут превышать «соседние» значения, что недопустимо при контроле температур малых объектов, в частности – при поиске горячих точек. В отличие от интерполяции технология SuperResolution направлена на повышение разрешения и степени детализации с возможностью воссоздания изначальных характеристик сигнала, выполняя программный расчёт показаний исходя из массива данных, поэтому результат максимально сходен с изображением, получаемым от матрицы с более высоким разрешением.
![]() |
На приведенном графике, чёрная кривая – это исходный сигнал, белые столбики это исходные значения пикселей. Серые столбики это искусственно сгенерированные значения интерполяции, с помощью которых воссоздать исходный сигнал невозможно. Оранжевые столбики это значения, полученные посредством технологии Super Resolution которые могут быть использованы для воссоздания исходного сигнала. Как видно из приведенных графиков, при помощи технологии SuperResolution выполняется расчёт реальных значений, результат которого можно сравнить с изображением, созданным тепловизором с детектором более высокого класса. На практике это означает, что при неизменном расстоянии теплового контроля, полученная термограмма будет более детальной. Как результат, изображение с разрешением 160х120 по качеству будет соответствовать изображению 320х240 пикселей, термограмма 320х240 пикселей, станет термограммой 640х480 пикселей, а снимок 640х480 пикселей – снимком с разрешением 1280х960 пикселей. При этом каждый полученный в результате пиксель будет содержать реальные температурные значения контролируемых объектов. Пример изображен следующих рисунках.
![]() |
![]() |
Снимок, сделанный тепловизором testo 881 с разрешением 160 х 120 пикселей и снимок того же прибора, но с использованием технологии SuperResolution с качеством изображения аналогичным детектору 320 х 240 пикселей.
![]() |
![]() |
Термограмма тепловизора testo 885 с разрешением 320 х 240 пикселей и термограмма, полученная при обработке SuperResolution, с качеством изображения аналогичным детектору 640 X 480 пикселей.
Технология Testo SuperResolution доступна для всех моделей тепловизоров серий тесто 875, тесто 876, тесто 881, тесто 882, тесто 885 и тесто 890. С помощью специального обновления встроенного ПО возможно дооснащение поставленных ранее моделей технологией SuperResolution.
В строительной термографии технология SuperResolution идеально подходит для быстрого и эффективного обнаружения дефектов строительства, а также для анализа потерь энергии в системах отопления и кондиционирования зданий, особенно при контроле удаленных объектов.
В сфере энергоснабжения технология значительно упрощает процесс теплового контроля систем низкого, среднего и высокого напряжения где предъявляются особые требования к разрешению полученных термограмм.
В области научно-исследовательских работ и электроники высокое разрешение SuperResolution может быть полезна для анализа распределения тепла на печатных платах и любых мельчайших деталей.
Подводя итог вышесказанному, можно сделать вывод - технология SuperResolution это возможность точного измерения температур мелких и удаленных объектов без необходимости в использовании детектора более высокого класса.
Видео презентация технологии Testo SuperResolution
Подпишитесь на наш канал RuTubeПрограммное обеспечение Testo IRSoft для анализа термограмм
IRSoft программное обеспечение для профессионального анализа термограмм на ПК, разработанное компанией Testo.
Аналитические функции программы IRSoft дают возможность корректировки коэффициента излучения различных материалов для отдельных областей снимка, вплоть до каждого пикселя. Функция гистограммы отображает распределение температур на контролируемой поверхности с возможностью анализа температурных кривых, определения границ предельных значений, самой холодной/горячей точки. Программа имеет возможность параллельного анализа нескольких термограмм с функцией переноса правок с текущего изображения на все открытые снимки одним нажатием клавиши. Также предусмотрена возможность добавления голосовых и текстовых комментариев.
Помимо своего функционала программа IRSoft отличается понятной структурой и удобством в использовании. Все функции программы сопровождаются интуитивно понятными символами и подсказками. Помощник создания отчетов имеет пошаговую инструкцию и типовые шаблоны облегчающие процесс работы неопытным пользователям. Шаблоны содержат информацию о местах проведения контроля, поставленных задачах и полученных результатах, в том числе по стандарту DIN EN 13187. Также предусмотрена возможность создания индивидуальных шаблонов с учетом требований заказчика.
Полная версия программы IRSoft поставляется в комплекте со всеми моделями тепловизоров Testo. Скачать программу бесплатно, можно перейдя по ссылке. Презентация программного обеспечения IRSoft для тепловизоров Testo
Программа обработки термограмм тепловизоров Тесто
Программа для анализа термограмм тепловизоров Testo
IRSoft – программное обеспечение тепловизоров Testo
Среди других технологий и потребительских свойств тепловизоров Testo можно выделить:
Температурная чувствительность. При регистрации самых незначительных перепадов температур особенно важным фактором является оптимальная температурная чувствительность (NETD). Тепловизоры Testo обеспечивают высокую температурную чувствительность до < 30 мК, которая в комбинации с высокой разрешающей способностью позволяет визуализировать малейшие перепады температур независимо от размеров обследуемого объекта.
Возможность измерения высоких температур. В некоторых секторах промышленности необходимо измерение очень высоких температур. У тепловизоров Testo есть возможность расширения температурного диапазона до 1200°C. Данный максимум делает тепловизоры Testo применимыми практически в всех отраслях промышленности. Высококонтрастное отображение высоких и низких температур возможно благодаря высокотемпературной цветовой палитре Iron HT или специальной компенсации на гистограмме.
Анализ тепловых процессов в режиме реального времени. С помощью функции создания полностью радиометрических видеозаписей пользователи тепловизоров Testo имеют возможность регистрировать тепловые процессы в режиме реального времени. В дальнейшем термографические видеозаписи могут передаваться на ПК для детального анализа любого момента видеозаписи содержащей данные температуры по каждому пикселю. Данная функция полезна при контроля всех стадий нагрева в течении определенного промежутка времени. Кроме того, функция регистрации данных обеспечивает возможность создания серии отдельных изображений в заданные временные интервалы или после определенных событий, например после превышения допустимых температур. В качестве опции, функция доступна для тепловизоров Тесто 885-2 и Тесто 890-2
Технология TwinPix (двойное изображение). Тепловизоры Testo с встроенной цифровой камерой выполняют одновременное сохранение инфракрасного и реального изображений. Новая функция наложения снимков Testo TwinPix накладывает эти изображения друг на друга делая термограмму намного проще для восприятия. Настройка уровней прозрачности и диапазона критических температур регулируют соотношения реального и инфракрасного изображения, после чего проблемные участки выделяются характерным цветом делая термограмму гораздо более наглядной чем инфракрасная. Данная функция применима даже если объекты контроля находятся на разных расстояниях.
Тепловизоры Тесто – технология твинпикс
Режим измерения “Солнечная энергия”. Интенсивность солнечного излучения играет важную роль в диагностике фотоэлектрических систем. При недостаточно интенсивном солнечном свете получение качественной термограммы невозможно. При выполнении измерений в режиме “Солнечная энергия” возможен ввод параметров интенсивности солнечного излучения, которое сохраняется в памяти тепловизора для дальнейшего анализа термограмм с помощью программы IRSoft.
Беспараллаксный лазерный целеуказатель, выводимый на дисплей тепловизоров Testo, облегчает решение задач теплового мониторинга, помогая не упускать из вида контролируемые объекты.Точка-ориентир зеркально отображает область замера, на которую наведен лазерный указатель. Помимо этого на дисплее отображается точная температура точки, находящейся под прицелом лазера.
Интуитивное управление. При разработке тепловизоров Testo большое внимание было уделено возможности интуитивного управления приборами. В результате, управление любой моделью осуществляется пользователем с максимальной легкостью.Новое гибридное управление дает возможность навигации через сенсорный дисплей. с помощью одной руки, это позволяет пользователю держать вторую руку свободной (например, в целях безопасности).
Оптимальная эргономичность тепловизоров Testo позволяет эффективней справляться с задачами строительной термографии. Помимо широко известных моделей тепловизионных камер с дизайном рукоятки-пистолета тесто предлагает модели в форме видеокамеры, оснащенные откидным поворотным дисплеем, позволяющим располагать тепловизор наиболее удобным способом для создания термограмм любых участков. Эргономичная вращающаяся рукоятка обеспечивает дополнительную надежность и удобство при проведении съемки труднодоступных участков.
Технология SiteRecognition дает возможность точной идентификации местоположения контролируемых объектов. Данная функция особенно актуальна при тепловом контроле большого количества сходных предметов, когда могут возникнуть сложности при идентификации сделанных термограмм. Технологии SiteRecognition автоматически распознает объекты по специальным отметкам обрабатываемых программой. Для удобства пользователей возможен поиск по названию объекта, дате или температурным параметрам. Технология SiteRecognition так же дает возможность просмотреть и сравнить снимки за прошедшие периоды. Подробное описание технологии SiteRecognition
Частые вопросы по тепловому контролю
Как выбрать тепловизор?
Выбирая тепловизор прежде всего надо определиться для каких задач он будет использоваться и исходя из этого подобрать прибор с соответствующими техническими характеристиками не переплачивая за функции которые в дальнейшем не пригодятся. Описание основных ценообразующих характеристик, которые помогут ответить на вопрос – как выбрать тепловизор, приведено здесь.
Чем тепловизоры Testo лучше аналогичных моделей других производителей?
Смотрите сравнение тепловизоров Testo с конкурентами Flir, Fluke, SAT, NEC
Как рассчитать поле зрения тепловизора и минимальный контролируемый объект?
Для того чтобы определить поле зрения тепловизора и минимальный объект точную температуру которого он способен измерить. Можно воспользоваться конвертером поля зрения тепловизоров Тесто.
В каких случаях необходим дополнительный узкоугольный объектив?
Объектив определяет поле зрения тепловизора. Стандартный широкоугольный объектив позволяет сделать снимок большого участка с близкого расстояния. Дополнительные узкоугольные объективы дают возможность контролировать мелкие, удаленные объекты. По общему правилу - чем меньше угол поля зрения, тем дальше можно отойти от объекта, без потери качества термограммы
Чтобы определиться с необходимостью покупки дополнительного узкоугольного объектива надо знать примерное максимальное расстояние до объекта контроля, его размер и требования к качеству получаемых термограмм. Дальнейший расчет можно произвести при помощи конвертера поля зрения тепловизоров Тесто
Какой тепловизор необходим для аттестации лаборатории неразрушающего контроля?
Для аттестации лаборатории НК по тепловому методу контроля, достаточно самого бюджетного тепловизора представленного в линейке приборов Testo. Стоимость аттестации можно рассчитать здесь.
Что такое – технология SuperResolution?
Технология SuperResolution (супер разрешение) дает возможность без использования процесса интерполяции, улучшить пространственное разрешение тепловых снимков в 1,6 раза а количество температурных точек в 4 раза, позволяя получить термограмму сравнимую по качеству с детектором более высокого класса. С подробным описанием технологии, можно ознакомиться здесь.
Возможно ли наблюдать процессы нагрева и охлаждения в динамике?
Динамику тепловых процессов можно отобразить, используя серию термограмм сделанных через заданные промежутки времени или при помощи функции создания полностью радиометрических видеозаписей, которая позволяет регистрировать тепловые процессы в режиме реального времени. Данной функцией в качестве опции могут оснащаться модели testo 885-2 и 890-2.
На до ли поверять тепловизор?
Тепловизор это измерительный инструмент подлежащий поверке с периодичностью один раз в год. Тепловизоры не внесенные в Госреестр средств измерений РФ подлежат калибровке с той же периодичностью. Если тепловизор не поверен (не откалиброван) то работы, выполненные с его помощью могут быть признаны не действительными, т.к. к отчету с результатами теплового контроля должно прикладываться действующее метрологическое свидетельство.
Стоимость поверки тепловизора зависит от срока и диапазона поверяемых температур. На октябрь 2013 стоимость поверки составляет:
- поверка тепловизора в диапазоне от -20 до 400 ˚С (срок - 21 день) - 16 500р.
- поверка тепловизора в диапазоне от -20 до 400 ˚С (срок – 7 дней) - 26 500р.
- поверка тепловизора в диапазоне от 0 до 1200 ˚С (срок - 21 день) - 19 000
- поверка тепловизора в диапазоне от -20 до 1200 ˚С (срок - 21 день) - 23 000р.
Когда лучше покупать тепловизор?
Поскольку тепловизоры часто используются для контроля систем отопления и отапливаемых объектов, пик использования приборов приходится именно на отопительный сезон, поэтому оптимальное время покупки тепловизора в многом связано со сроками отопительного сезона в регионе где планируется его использование. Оптимальным временем для покупки тепловизора (в центральном регионе) можно считать период с июля по сентябрь. Причины следующие:
- цена на тепловизоры до начала сезона часто бывает ниже чем после;
- поверка купленного летом тепловизора закончится через 12 месяцев, следовательно, у владельца прибора будет время оформить новое свидетельство до начала следующей сезонной эксплуатации. Для справки – не срочная поверка тепловизора в ФБУ "Ростест-Москва" выполняется в срок 21 день.
Оказываете ли вы услуги по тепловизионному контролю?
Лаборатория НТЦ «Эксперт» оказывает услуги по тепловому контролю промышленных и жилых объектов. Тепловой контроль проводится с применением современных промышленных тепловизоров и других приборов. По результатам контроля составляется подробный отчет, включающий наглядную тепловую карту (термограмму), заключение о качестве объекта и рекомендации по устранению выявленных дефектов.
Каков порядок аттестации специалистов проводящих тепловой контроль?
Тепловой контроль опасных производственных объектов перечисленных в приложении 1. СДАНК-01-2020, выполняется лабораторими НК располагающими аттестованным в установленном порядке персоналом. Подробная информация по аттестации специалистов содержится здесь. Информация по аттестации лабораторий здесь.
Порядок лицензирования специалистов проводящих тепловой контроль на объектах, не относящихся к опасным производственным объектам, регулируется соответствующими отраслевыми ведомствами и саморегулируемыми организациями.
Для начинающих пользователей полезно будет ознакомиться с практическим руководством по промышленной термографии. В руководстве рассмотрены вопросы связанные с теорией тепловизионного контроля, условиями его проведения, распространенными ошибками и другая полезная информация.
Источник - статья Е. А. Иванова опубликованная в журнале «В мире НК» № 3(17). сентябрь 2002.
Другие статьи на тему аттестации специалистов и лабораторий неразрушающего контроля можно посмотреть в разделе Статьи.
Задача обеспечения промышленной безопасности в условиях продолжающегося физического износа оборудования на опасных производственных объектах и отсутствия средств на его замену и реконструкцию обуславливает повышение роли созданной Госгортехнадзором России Системы НК как одного из основных факторов, определяющих техническое состояние указанных объектов, возможность и сроки их дальнейшей эксплуатации [1].
В 2000 г. износ действующих в России фондов достиг 42,4 % при коэффициенте обновления 1,2 % по сравнению с 5,8 % в 1990 г. и 8,2 % в 1980 . В настоящее время на опасных производственных объектах до 60–80 % технических устройств и сооружений выработали проектные сроки эксплуатации [2]. Даже при условии реализации мероприятий, предусмотренных постановлением Правительства РФ [3], к 2010 г. планируется обновить только около 30 % оборудования на опасных производственных объектах. Таким образом, значительная часть оборудования опасных производственных объектов будет эксплуатироваться после выработки проектных сроков эксплуатации. Дальнейшая эксплуатация такого оборудования без проведения специальных мер по обеспечению промышленной безопасности не только нецелесообразна экономически, но и представляет природную и техногенную опасность и обуславливает необходимость проведения комплексных мероприятий по оценке возможности эксплуатации оборудования с истекшим нормативным сроком эксплуатации.
Решение задач по поддержанию высокой эксплуатационной надежности опасных производственных объектов требует совершенствования и более широкого использования мониторинга технического состояния оборудования и сооружений на опасных производственных объектах, что целесообразно осуществлять путем проведения НК и ТД с последующей оценкой ресурса эксплуатации до наступления предельного состояния.
Признавая, что только комплексный подход обеспечит повышение достоверности, воспроизводимости и сопоставимости результатов НК, а также принятие своевременных и адекватных решений по обеспечению промышленной безопасности и станет основой обеспечения необходимого уровня эксплуатационной безопасности технических устройств, зданий и сооружений на опасных производственных объектах, Госгортехнад-зор России создал Систему НК. Актуальность развития и совершенствования НК в отраслях промышленности определяется тем, что постановлением Правительства [4] Госгортехнадзору России поручено организовать работы по развитию и внедрению системы контроля, позволяющего осуществлять экспертизу промышленной безопасности и проводить техническое диагностирование для принятия решения о продлении срока безопасной эксплуатации на опасных производственных объектах на территории России. Данным постановлением установлено, что продление срока безопасной эксплуатации технических устройств, оборудования и сооружений, эксплуатируемых на опасных производственных объектах на территории РФ, осуществляется в порядке, определяемом Госгортех-надзором России.
В соответствии с принятой «Концепцией...» [1] вводится аттестация персонала, лабораторий, методических документов и средств НК.
Первой подсистемой Системы НК, реализованной в практической деятельности организаций, осуществляющих НК на опасных производственных объектах, стала аттестация лабораторий НК. Аттестация лабораторий, выполняющих НК на объектах котлонадзора и подъемных сооружениях, проводилась с1996 г. Ввиду общности целей и близости задач работы по аттестации лабораторий НК было решено проводить в рамках Системы экспертизы промышленной безопасности [1].
Для аттестации лабораторий НК создана организационно-методическая база. Прошли регистрацию в Минюсте России (25.07.2000 N 2324) и постановлением Госгортехнадзора России от 25.09.2000 N 54 введены в действие «Правила аттестации и основные требования к лабораториям неразрушающего контроля» ПБ 0337200. К 1 января 2002 г. в организациях, подконтрольных 20 территориальным управлениям ГосгортехнадзораРоссии, аккредитовано 32 Независимых органа по аттестации лабораторий НК (НОАЛ): в Управлении Московского округа – 9; в Управлении Северо-Западного округа – 3; в Управлении Западно-Уральского округа и Самарском управлении – по 2; в 18 управлениях – по одному НОАЛ. С момента введения в действие ПБ 03-372-00 до 1 января 2002 г. в организациях, подконтрольных 36 территориальным органам Госгортехнадзора России, аттестовано 850 лабораторий НК.
Функционирование подсистемы аттестации лабораторий позволило определить некоторые статистические характеристики подразделений НК, выполняющих НК на опасных производственных объектах. Распределение областей аккредитации НОАЛ и аттестации лабораторий НК по промышленным секторам * и видам (методам) НК приведены в табл. 1 и 2.
* Промышленный сектор определяется конкретными типами технических устройств и сооружений, надзор за эксплуатацией которых на опасных производственных объектах осуществляют отраслевые управления и отделы Госгор-технадзора России.
Таблица 1. Распределение аккредитованных НОАЛ и аттестованных лабораторий НК по промышленным секторам
Области аккредитации НОАЛ и области аттестации лабораторий НК по промышленным секторам | % от общего количества: | |
аккредитованных НОАЛ | аттестованных лабораторий НК | |
Оборудование, работающее под избыточным давлением | 97 | 63 |
Системы газоснабжения (газораспред.) | 94 | 52,8 |
Подъемные сооружения | 84 | 43 |
Оборудование нефтяной и газовой промышленности | 72 | 32 |
Оборудование взрывоопасных и химически опасных производств | 63 | 28 |
Оборудование металлургической промышленности | 47 | 5,4 |
Объекты горнорудной промышленности | 19 | 1,5 |
Объекты угольной промышленности | 19 | 0,7 |
Объекты железнодорожного транспорта | 0 | 0,4 |
Объекты хранения и переработки зерна | 6 | 0 |
Таблица 2. Распределение аккредитованных НОАЛ и аттестованных лабораторий НК по видам (методам) НК
Виды (методы) НК в области аккредитации НОАЛ и области аттестации лабораторий НК | % от общего количества: | |
аккредитованных НОАЛ | аттестованных лабораторий НК | |
1. Ультразвуковой | 100 | 84,3 |
2. Визуальный и измерительный | 100 | 79,7 |
3. Радиационный | 96,9 | 68,8 |
4. Проникающими веществами | 93,8 | 46,3 |
5. Магнитный | 90,6 | 39 |
6. Акустико-эмиссионный | 81,3 | 8,7 |
7. Вихретоковый | 56,3 | 7 |
8. Вибродиагностический | 34,4 | 2,1 |
В области аккредитации НОАЛ входит от 2 до 8 промышленных секторов и от 3 до 8 видов (методов) контроля. Сведения о количестве промышленных секторов и количестве видов (методов) НК в области аккредитации НОАЛ и области аттестации лаборатории НК приведены в табл. 3.
Таблица 3. Распределение НОАЛ и лабораторий НК по количеству промышленных секторов и видов (методов) НК в области аккредитации (аттестации)
Области аккредитации НОАЛ и области аттестации ЛНК | % от общего количества НОАЛ (лабораторий НК), имеющих в области аккредитации (аттестации) следующее количество промышленных секторов, видов (методов) контроля | ||||||||
1 | 2 | 3 | 4 | 5 | 6 | 7 | 8 | ||
НОАЛ | Промышленных секторов | 3,1 | 6,3 | 9,4 | 15,6 | 37,5 | 6,3 | 6,3 | 15,6 |
Видов (методов) НК | 0 | 0 | 3,1 | 6,3 | 6,3 | 18,8 | 50,0 | 15,6 | |
ЛНК | Промышленных секторов | 34,2 | 30,9 | 17,6 | 10,9 | 5,9 | 0,2 | 0,2 | 0,1 |
Видов (методов) НК | 10,0 | 16,1 | 25,9 | 27,6 | 13,5 | 4,0 | 2,7 | 0,2 |
Более 65 % лабораторий НК выполняют работы по НК в 1–2 промышленных секторах, почти 30 % — в 3–4 секторах. Более половины лабораторий выполняют НК 3–4 видами (методами) контроля. Как правило, это ультразвуковой и/или радиационный, капиллярный и/или магнитный и визуально-измерительный виды (методы).
Наименьшее количество видов (методов) контроля применяют лаборатории, выполняющие НК только на объектах газоснабжения (часто только рентгенографический метод). Наибольшее количество видов (методов) применяется при НК на объектах котлонадзора и при контроле оборудования взрывопожароопасных и химически опасных производств. При контроле оборудования этих объектов кроме вышеперечисленных часто используется вихретоковый и акустико-эмисси-онный методы НК, реже вибродиагностический.
Аттестация лабораторий позволила упорядочить, во-первых, организационные формы подразделений НК, их структуру, подчиненность, взаимоотношения с другими подразделениями и сторонними организациями, обеспечение принципов независимости при НК как структурных подразделений, так и персонала лаборатории. Во-вторых, упорядочить документированные процедуры, которыми руководствуется лаборатория, включая:
- правовые и организационно-методические документы – учредительные документы юридических лиц и положения подразделений НК рганизации, документированные процедуры обеспечения качества при НК;
- методические документы по НК и технологические документы по объектам контроля, позволяющие осуществлять контроль и производить оценку качества технических устройств и сооружений видами (методами) НК, включенными в область аттестации лаборатории;
- документацию по персоналу лаборатории – должностные инструкции и документы, подтверждающие квалификацию и аттестацию по типам технических устройств и сооружений видами (методами) НК, включенными в область аттестации лаборатории, аттестацию на знание правил безопасности;
- ведение документооборота лаборатории и архива, наличие процедур проведения работ по НК, включая оформление результатов контроля, выдачу заключений и их хранение, обеспечение конфиденциальности и охраны прав собственности.
В-третьих, аттестация лабораторий позволила упорядочить оснащенность техническими средствами НК и их состояние – организацию учета, технического обслуживания, ремонта и метрологической аттестации (поверки), достаточность для организации контроля технических устройств и оборудования видами (методами) НК, включенными в область аттестации лаборатории.
Аттестация лабораторий НК является комплексной оценкой функционирования всех элементов аттестации в Системе НК, при аттестации лабораторий проверяются правильность и обоснованность аттестации технических средств, методических документов и персонала НК.
Таким образом, аттестация лабораторий НК является критерием организационной и технической готовности к выполнению эффективного и достоверного НК технических устройств, зданий и сооружений, основанного на реализации возможностей современных технических средств и методик контроля, единых требований к подготовке и аттестации персонала, а также к управлению структурными подразделениями, осуществляющими НК на опасных производственных объектах. Выполнение работ по НК аттестованной лабораторией является гарантией соблюдения технологической дисциплины НК и обеспечения промышленной безопасности на опасных производственных объектах.
Дальнейшее развитие получила подсистема аттестации персонала НК. Постановлением Госгортехнадзора России от 23.01.2002 N 3 утверждены и прошли регистрацию в Минюсте России от 17.04.2002 N 3378 «Правила аттестации персонала в области неразрушающего контроля» СДАНК-02-2020. Они охватывают все виды (методы) НК и всю номенклатуру технических устройств, зданий и сооружений, применяемых на опасных производственных объектах, гармонизированы с требованиями и процедурами Системы НК и международных стандартов в области аттестации персонала НК, что позволит полнее реализовать положения Федерального закона [5] в части аттестации работников в области промышленной безопасности.
Задержка с организацией работы подсистем аттестации методических документов и средств НК приводит к тому, что не по всей номенклатуре технических устройств и сооружений на опасных производственных объектах имеются документы по НК. Действующие документы имеют разный уровень утверждения, согласования и сроки разработки. В лабораториях НК не исключены случаи применения технических средств, не обеспечивающих необходимое качество НК, недостаточно метрологическое обеспечение НК.
Таким образом, подтверждается необходимость функционирования всех элементов Системы НК – подготовки и аттестации специалистов НК и применяемых методических документов, организации процесса контроля, а также состояния и технического уровня используемых средств контроля.
Ближайшими задачами развития Системы НК являются:
- принятие и введение в действие документированных процедур аттестации методических документов и технических средств НК;
- реализация принципа безопасной эксплуатации оборудования на опасных производственных объектах по его техническому состоянию с оценкой остаточного ресурса по определяющим критериям, установленными методами НК и ТД.
Решение этих задач внесет существенный вклад в обеспечение промышленной безопасности опасных производственных объектов.
Литература
1. Концепция управления Системой неразру-шающего контроля и основные направления ее развития, Система неразрушающего контроля. Аттестация лабораторий (сборник документов). Сер. 28. Вып. 1. – М.: ГУП «НТЦ «Промышленная безопасность», 2000. С. 5–16.
2. Государственный доклад «О состоянии промышленной безопасности опасных производственных объектов, рационального использования и охраны недр Российской Федерации в 2000 году» /Под ред. В.М. Кульечева. – М.: ГУП «НТЦ «Промышленная безопасность», 2001. – 196 с.
3. Федеральная целевая программа «Энергоэффективная экономика» на 2002–2005 гг. и на перспективу до 2010 г. (утверждена постановлением Правительства РФ от 17.11.2001 N 796). – Собрание законодательства РФ. 2001. N 49. С. 10242–10298.
4. Постановление Правительства РФ от 28.03.2001 N 241 «О мерах по обеспечению промышленной безопасности опасных производственных объектов на территории Российской Федерации». – Там же. 2001. N 15. С. 3367.
5. Федеральный закон «О промышленной безопасности опасных производственных объектов» – М.: НТЦ «Промышленная безопасность», 1999. – 36 с.
Источник - статья Г. Я. Дымкина опубликованная в журнале «В мире НК» № 4(10). декабрь 2000.
Другие статьи на тему аттестации специалистов и лабораторий неразрушающего контроля можно посмотреть в разделе Статьи.
Требования по обеспечению эксплуатационной надежности пути и подвижного состава обуславливают необходимость повышения эффективности систем НК транспортных конструкций как при их изготовлении, так и при эксплуатации и ремонте. Техническая эффективность систем НК в значительной мере зависит от надежности комплекса "дефектоскоп-оператор-среда", которая, в свою очередь, определяется квалификацией дефектоскопистов и правильной организацией процесса НК.
В путевом, вагонном, пассажирском и локомотивном хозяйствах ж.-д. транспорта России в области НК по 25 специализациям и должностям работает более 14 тыс. специалистов, функционирует около 900 лабораторий (подразделений ) НК[1].
Для повышения эффективности действующих систем НК МПС России введены отраслевые Система сертификации персонала по НК (ССПНК ЖТ) и Система аккредитации лабораторий НК (САЛНК ЖТ), функционирующие как подсистемы в рамках соответствующих национальных систем, введенных Госстандартом России.
ССПНК ЖТ регламентируется "Правилами сертификации персонала по НК технических объектов железнодорожного транспорта. ПР 32.113-98".
Сертификации подлежат специалисты по магнитному, вихретоковому и акустическому (ультразвуковому) видам (методам) НК элементов, деталей и узлов следующих технических объектов:
- вагоны грузовые и пассажирские;
- локомотивы;
- рельсы железнодорожные;
- мостовые конструкции железнодорожные, металлические.
Сертификацию проводят Дорожные (региональные) Уполномоченные органы и экзаменационные центры, аккредитованные в российской системе после прохождения экспертизы и признания их в соответствии с "Положением об экспертизе уполномоченных органов и экзаменационных центров П ССПНК ЖТ.01-98". В настоящее время действуют:
Уполномоченные органы
- Аттестационный центр "Путь" при НК-Центре (Санкт-Петербург);
- Уральский центр аттестации (Екатеринбург).
Экзаменационные центры
- На Западно-Сибирской ж. д. (при СибГУПС, г. Новосибирск);
- На Восточно-Сибирской ж. д. (при Дорожном центре обучения, ст. Суховская).
Документами ССПНК ЖТ конкретизированы требования к специальной подготовке персонала по НК. Подготовка к сертификации должна проводиться в Учебных центрах, получивших свидетельство о признании согласно "Положению об экспертизе учебных центров... П ССПНК ЖТ.02-98" и по программам, согласованным Экспертной организацией МПС России по НК. Функции экспертной организации МПС РФ по НК возложены на "Отраслевой учебно-методический и аттестационный центр по НК и диагностике технических объектов" (НК-Центр) при НИИ мостов и дефектоскопии МПС России. Первыми на сети ж. д. России прошли экспертизу и признаны Учебные центры по НК при Дорожном центре обучения Восточно-Сибирской ж. д., Дорожной технической школе № 1 Свердловской ж. д., СибГУПС и Западно-Сибирской ж. д., Дорожном центре обучения Забайкальской ж. д. В них осуществляется подготовка специалистов к сертификационным экзаменам на I и II уровни квалификации по НК рельсов, а также деталей и узлов вагонов и локомотивов. Подготовка к экспертизе Учебных центров ведется на Северо-Кавказской, Дальневосточной, Северной и Горьковской ж. д.
В первую очередь проходят сертификацию руководители подразделений НК предприятий ж. д. С момента введения ССПНК ЖТ сертифицировано 176 специалистов с 15-ти железных дорог, среди которых наиболее активны Октябрьская, Северная и Свердловская. Около 33% из числа сертифицированных - дефектоскописты рель-сосварочных предприятий и начальники участков дефектоскопии дистанций пути, 35 % - специалисты по НК вагонного и пассажирского хозяйств.
Сертификация не заменяет, а дополняет и предваряет действующую систему аттестации персонала в области НК.
Организационная структура САЛНК ЖТ, порядок аккредитации и специальные требования к лабораториям НК определены документами системы (ПР 32.151-2000, П САЛНК 01, П САЛНК 04). Под лабораторией НК понимается как самостоятельное юридическое лицо или структурное подразделение предприятия (участок, бригада в депо, цех дефектоскопии дистанции пути, вагон-дефектоскоп и т. п.), так и рабочие места НК с персоналом (контрольный пост на РСП, рабочее место дефектоскописта в депо и т. п.).
Аккредитацию проводят Орган по аккредитации лабораторий НК на ж.-д. транспорте (Аттестат № РОСС RU.0001.550001), входящий в состав НК-Цент-ра, и уполномоченные им территориальные (дорожные) аудиторские организации. В качестве аудиторской организации зарегистрирована, в частности, Дорожная лаборатория дефектоскопии Службы пути Московской ж. д.
В соответствии с требованиями МПС России большое внимание уделяется аккредитации лабораторий НК предприятий, поставляющих продукцию для ж.-д. транспорта. Аккредитованы Служба НК Нижнетагильского металлургического комбината, производящего рельсовый прокат, бандажи и цельнокатаные колеса, и Отдел НК Уралвагонзавода, выпускающего оси колесных пар и вагоны различных типов.
Введение ССПНК ЖТ и САЛНК ЖТ - эффективное средство повышения надежности НК и установления таким образом действенного контроля за качеством технологических процессов эксплуатации и ремонта подвижного состава и рельсового пути, определяющих в целом безопасность движения поездов.
Литература
1. Герасимов ЮМ. Неразрушающий контроль и безопасность перевозочного процесса на железных дорогах России. - В мире НК. 1999. № 5. С. 14-15.
Источник - статья Г. Я. Дымкина опубликованная в журнале «В мире НК» № 2(48). 2010.
Другие статьи на тему аттестации специалистов и лабораторий неразрушающего контроля можно посмотреть в разделе Статьи.
Сертификация персонала НК в отрасли железнодорожного транспорта проводится с 1998 г. в рамках Системы добровольной сертификации персонала в области НК – ССПНК (зарегистрирована в системе Ростехрегулирования под ¹ РОСС RU.0001.04ЮА00 и перерегистрирована под ¹ РОСС RU.0001.03Н300) и в соответствии с отраслевым нормативным документом ПР 32.113-98 [1], введение которого отразило понимание в МПС России важной роли независимой проверки знаний и навыков работников, выполняющих НК, в обеспечении безопасности движения на железнодорожном транспорте.
Методическое руководство Системой сертификации персонала по НК объектов железнодорожного транспорта (ССПНК ЖТ) осуществляет «Отраслевой учебно-методический и аттестационный центр по неразрушающему контролю и диагностике технических объектов» (НК-Центр) – филиал ФГУП «Научно-исследовательский институт мостов и дефектоскопии Федерального агентства железнодорожного транспорта», который выполняет функции экспертной организации в области НК и ведет Реестр ССПНК ЖТ, включающий реестры уполномоченных органов, экзаменационных и учебных центров, признанных в ССПНК ЖТ, а также реестр сертифицированного персонала по НК.
Сертификацию по акустическому (А), магнитному (М), вихретоковому (Вт) видам и акустико-эмиссионному (АЭ) методу НК объектов железнодорожного пути и подвижного состава при их производстве, эксплуатации и ремонте проводят 11 уполномоченных органов и экзаменационных центров (табл. 1). За истекшие годы сертифицировано более 2640 специалистов по НК – работников ОАО «РЖД» и других предприятий всех форм собственности, выполняющих производство и ремонт технических средств железнодорожного транспорта: деталей и узлов вагонов (58,2 %), локомотивов (17,7 %), рельсов (22,4 %), сварных конструкций искусственных сооружений (1,7 %). Распределение сертифицированных специалистов по уровням квалификации и видам НК (рис. 1) подтверждают как общие для всех отраслей промышленности потребности в специалистах различного уровня, так и особенности железнодорожного транспорта и транспортного машиностроения.
Введение дополнительных «отраслевых» требований к процедурам сертификации, а также к органам по сертификации и учебным центрам по подготовке специалистов к сертификации способствовало обеспечению единого методического уровня и объективности оценки квалификации специалистов по НК ответственных объектов железнодорожного транспорта.
Как известно, ССПНК является лишь одной из нескольких систем добровольной сертификации персонала по НК (или «аттестации», что в отечественной практике, по существу, одно и то же), зарегистрированных и более или менее активно действующих в настоящее время в России.
Анализ международных норм, регулирующих сертификацию персонала по НК, зарубежного и отечественного опыта сертификации, а также более чем 10-летний опыт проведения сертификации на железнодорожном транспорте подтверждает многократно декларируемую всеми участниками процесса необходимость восстановления единой национальной системы сертификации персонала по НК.

Рис. 1. Распределение персонала по НК, сертифицированного в соответствии с ПР 32.113-98, по уровням квалификации (а): зеленый, оранжевый и синий цвета – I, II и III уровни соответственно; и по видам (методам) НК (б): синий, желтый, красный и фиолетовый цвета – акустический, вихрето-ковый, магнитный и акустико-эмиссионный контроль соответственно
Основой для объединения (взаимного признания) действующих систем могут, по нашему мнению, стать новые нормативные документы, гармонизированные с международными стандартами и устанавливающие единые процедуры сертификации, формы удостоверений, требования к кандидатам и методические основы проведения базовых и общих экзаменов по видам (методам) НК. Перечень производственных секторов должен отражать отраслевое деление объектов контроля, а содержание и процедуры проведения специальных и практических экзаменов должны соответствовать отраслевым требованиям. При этом удельный вес проверки знаний кандидата должен быть перенесен с общего на специальный экзамен, а основной упор при сертификации на I и II уровни сделан на практическом экзамене, проводящем-ся в экзаменационных центрах, осна-щенных большим количеством образцов объектов контроля.
Для реализации та-кого подхода должны быть решены соот-ветствующие научно-методические зада-чи – пересмотр программ сертификации по всем видам НК и производственным секторам и перечней экзаменационных вопросов с существенным увеличением их количества. Наконец, следует устано-вить и ввести в практику правила и про-цедуры экспертизы и признания органов сертификации персонала по НК отрасле-выми органами государственной власти, в необходимых случаях органами надзо-ра и работодателями – саморегулируе-мыми организациями, некоммерчески-ми партнерствами предприятий и т. п. Представляется, что модернизация системы сертификации персонала мо-жет проводиться одновременно с об-суждением и введением в России ново-го унифицированного государственного стандарта, касающегося квалификации и сертификации персонала по НК.
Табл. 1. Выписка из реестра Уполномоченных органов и Экзаменационных центров, признанных в ССПНК ЖТ
Наименование Уполномоченного органа (Экзаменационного центра) по сертификации | Вид НК |
Уполномоченные органы (УО) | |
УО НК-Центр (филиал НИИ мостов), Санкт-Петербург | А, М |
УО «Уральский центр аттестации», Екатеринбург | А, М, Вт, АЭ |
УО «Транссиб» при Сибирском государственном университете путей сообщения, г. Новосибирск | А, М, АЭ |
Дорожный УО при Омском государственном университете путей сообщения | А, Вт, М |
УО при Ижевском государственном техническом университете | А, М, АЭ |
Экзаменационные центры (ЭЦ) | |
ЭЦ по НК при Петербургском государственном университете путей сообщения | А, М |
ЭЦ по НК «Импульс» Дорожного центра обучения Восточно-Сибирской ж. д., г. Иркутск | А |
ЭЦ по НК «Сигнал» Красноярской ж. д., г. Красноярск | А, М |
ЭЦ «Технология» Дорожного центра обучения Забайкальской ж. д., г. Чита | А, М |
Дорожный ЭЦ «Юго-Восток НК» при Воронежском филиале РГОТУПС | А |
ЭЦ по НК на базе Челябинского института путей сообщения | А, Вт, М |
Обозначения. Виды (методы) НК: А – акустический, М – магнитный, Вт – вихретоковый, АЭ – акустико-эмиссионный
Литература
1. ПР 32.113-98. Правила сертификации спе-циалистов по неразрушающему контролю техни-ческих объектов железнодорожного транспорта
Источник - статья Н. П. Бирюковой опубликованная в журнале «В мире НК» № 2(48). 2010.
Другие статьи на тему аттестации специалистов и лабораторий неразрушающего контроля можно посмотреть в разделе Статьи.
Сертификация персонала в области НК и технического диагностирования, т. е. подтверждение соответствия знаний и профессионального опыта специалиста документально установленным требованиям, является общепризнанной как в России, так и за рубежом.
Процедура проведения сертификации (аттестации), требования к органам, ее организующим и проводящим, регламентированы международными стандартами ISO 17024, ISO 17021, EN-473, ISO-9712 и др., а также документами российских систем СДСПНК РОНКТД, ЕС ОС-CДА-13-2009, СДАНК-02-2020, которые разработаны с учетом основных положений перечисленных зарубежных стандартов.
Эти документы хорошо изучены и освоены российскими органами по аттестации персонала, и их работа осуществляется согласно их требованиям.
В последние годы освоены и реализованы требования по системе менеджмента качества в соответствии с требованиями ISO 9001 и др. Проверяющие и аккредитующие организации выполнению этих требований уделяют большое внимание.
Упомянутые документы в основном определяют организационные и процедурные требования. Проблем у органов по сертификации в этом направлении нет, все процедуры идентифицированы.
Научно-учебный центр «Качество» аккредитован по российским и международным стандартам практически по всем методам и промышленным секторам. Центр – единственный в России и странах СНГ – аккредитован на тепловой метод и метод течеискания по стандартам ЕN-473 и ISO-9712, на сектор «Авиация и космонавтика» по стандарту EN 4179 и директиве EASA AMC 145.A.30; единственный в стране и Европе аккредитован на право сертификации персонала оценки напряженно-деформированного состояния материалов и конструкций.
Одной из основных задач настоящего времени является обеспечение объективности, беспристрастности и достоверности в оценке соответствия установленным требованиям уровня компетентности специалиста по объему теоретических знаний и профессионального опыта. Основные критерии, которым надлежит соответствовать специалистам, определяются содержанием общего, специального и практического экзаменов.
Различные сборники вопросов и по количеству, и по содержанию, процедура приема экзамена, оснащенность лабораторных баз и подходов к проведению практических экзаменов, состав экзаменационных личных дел, состав и требования к экзаменационным образцам, – все это не регламентировано документами, и, следовательно, идентичность оценки компетентности и квалификационного уровня специалистов, проходящих аттестацию в различных органах по сертификации, не обеспечивается.
Ниже приводятся подходы к решению этих задач в Научно-учебном центре «Качество», опыт которого в области подготовки и сертификации специалистов более 15 лет.
Остановлюсь последовательно на каждой части квалификационного экзамена.
Общая ответственность за содержание, актуализацию, соответствие курса современному уровню технологии и техники в НУЦ «Качество» возложена на специально созданную «Комиссию по разработке и актуализации экзаменационных вопросов и образцов». Комиссия состоит из подкомиссий, которые по каждому методу НК включают 4 – 5 специалистов III уровня квалификации и преподавателей по соответствующему методу. Заседания комиссии проводятся не реже 1 раза в полугодие.
Общий экзамен
Сборник вопросов общего экзамена для каждого метода состоит из трех блоков вопросов на соответствие требованиям к знаниям для специалистов I, II и III уровней.
Каждый из сборников имеет 4 раздела:
I. Физические основы и параметры метода.
II. Приборы и средства контроля.
III. Основы технологии, схемы контроля.
IV. Несоответствия при изготовлении и эксплуатации. Выявляемость данным методом.
Каждый раздел сборника содержит одинаковое количество вопросов, расположенных в порядке возрастания сложности. На каждый вопрос предлагается четыре варианта ответа, один из которых верный.
Экзаменационные вопросы отражают современное состояние науки, методов, средств, технологии НК и нормативной документации. Уровень сложности разрабатываемых экзаменационных вопросов определен достаточным для проверки соответствия квалификации кандидата требованиям российских, европейских и международных стандартов по методу НК, уровню квалификации.
Содержание вопросов, определение по разделам, подтверждение степени сложности рассматриваются и утверждаются Комиссией по актуализации сборников вопросов. Количество вопросов в сборниках по общему экзамену не менее чем в два раза превышает минимально требуемое количество вопросов, регламентируемых документами СДАНК-02-2020, EN 473, ISO 9712 и EN 4179.
Специальный экзамен
Специальный экзамен отражает особенности условий контроля, характерные дефекты, требования к качеству, оптимальные схемы и параметры контроля, основные положения соответствующих данному виду объектов нормативных документов и т. п.
Сборники вопросов специального экзамена составляются по каждому производственному сектору (объекту).
Так, например, по УЗК разработано и используется 15 сборников вопросов специальных экзаменов плюс один сборник, обобщающий одинаковые требования ко всем объектам, контролируемым ультразвуковым методом. Аналогичное положение и по остальным методам.
Таким образом, мы имеем более 100 сборников вопросов специального экзамена по всем методам и производственным секторам, причем каждый из них на I, II, III уровни.
Такой банк экзаменационных вопросов специального экзамена позволяет убедиться, что специалист владеет не только физическими основами метода и технологией контроля по нему, но и знает особенности подлежащих контролю объектов, характерные дефекты и эффективные схемы их выявления.
Процесс сдачи экзаменов
Сдача кандидатами письменных экзаменов (общего и специального) проводится на компьютере, для объективности и непредвзятости процесса номера вопросов выбираются с использованием генератора случайных чисел. Компьютерная программа составлена таким образом, что:
– на экране отсутствуют номера вопросов, что исключает возможность использования формализации в ответах; – обеспечивается обязательный выбор вопросов из каждого раздела и каждого уровня сложности;
– обеспечивается возможность возврата к вопросу, ответ на который вызвал затруднения – по аналогии со сдачей экзамена без использования компьютера; – по окончании экзамена производится распечатка протокола результатов с фиксированием продолжительности экзамена; – на отдельном листке распечатывается текст вопросов, на которые были даны неверные ответы.
Такая система позволяет объективно и достоверно, в полном объеме оценить знание кандидатом физических основ и параметров метода по различным разделам и степени сложности, а также предоставляет возможность кандидату в дальнейшем обдумать вопросы, по которым у него не было достаточных знаний.
Актуализация сборников вопросов
Сборники вопросов не реже одного раза в полугодие подлежат актуализации.
Так как прием общих и специальных экзаменов в НУЦ «Качество» проводится с использованием компьютерной программы, все результаты экзаменов автоматически заносятся в электронную базу данных, что позволяет проводить статистический анализ результатов экзаменов в автоматическом режиме и упрощает процедуру актуализации. Результаты ответов на экзамене обрабатываются дополнительно за любой промежуток времени, при этом на протоколе отражаются:
– номера вопросов (общий перечень);
– число раз, когда выпадал данный вопрос;
– число правильных и неправильных ответов на конкретный вопрос.
По протоколу корректировке подлежат вопросы, 100 % ответов на которые были правильными, что свидетельствует о простоте вопроса или явной однозначности ответа, а также те вопросы, на которые дано менее 50 % правильных ответов, т. е. они либо некорректно сформулированы, либо не соответствуют требованиям программы данного квалификационного уровня.
– некорректность вопросов, выявленная по результатам ответов экзаменуемых;
– сложность, выявляемая по постоянным неправильным ответам; – однозначность ответов на вопрос;
– замечания и предложения экзаменаторов по содержанию вопросов; – необходимость включения новых вопросов в связи с введением новой нормативной документации;
– необходимость исключения вопросов, соответствующих нормативной документации, срок действия которой истек.
Решение по изменению принимает подкомиссия по актуализации по соответствующему методу, каждый раз оформляя это соответствующим протоколом, после чего соответствующие изменения вносятся в сборник экзаменационных вопросов.
Кроме экзаменационных вопросов в центре разработаны соответствующие сборники вопросов для стажировки, которые по содержанию близки к экзаменационным вопросам, однако вместо ответов в них содержатся ссылки на источник и номера страниц, где можно найти ответ. Таким образом обеспечиваются условия закрепления материалов перед экзаменом.
Практический экзамен
Этот экзамен состоит из трех частей: технологическая карта, контроль трех образцов, собеседование.
Технологическая карта
В нормативно-методические документы на НК конкретных объектов включены формы технологических карт, несколько отличающиеся друг от друга. Форма технологической карты, разработанная в нашем центре и предлагаемая кандидатам, включает все последовательные технологические операции контроля заданного объекта. Оформленная правильно, в соответствии с требованиями, технологическая карта подтверждает четкое знание всех этапов технологии контроля.
Кандидат заполняет две карты: одну – для стажировки, другую – экзаменационную на один из подлежащих контролю экзаменационных образцов.
Контроль экзаменационных образцов
В системе СДСПНК РОНКТД разработан документ 003.03.10 «Технические правила для органов по сертификации персонала в области НК», где представлены минимальные требования по типу и количеству приборов, средств, контрольных образцов для оснащения лабораторных баз практического экзамена по каждому методу. Лаборатория НК НУЦ «Качество» полностью соответствует требованиям указанного документа и насчитывает около 230 единиц оборудования. В этой части экзамена очень важно соблюдение технологии контроля, соблюдение условий контроля. С целью объективной независимой беспристрастной оценки практического экзамена разработана форма протокола оценки практического экзамена. Протокол состоит из 4-х частей:
– оценка знания приборов и средств;
– параметры и настройка режимов контроля;
– обнаружение и протоколирование не-сплошностей; – письменная инструкция (технологическая карта).
Каждая из частей включает несколько подпунктов, детализирующих данную часть процедуры.
Каждый пункт оценен в баллах, а также определены баллы снижения за каждую ошибку, допущенную кандидатом.
Экзаменаторы оценивают практическую работу независимо друг от друга; результаты представляются как среднее значение.
Собеседование
В заключение практического экзамена по российским нормам проходит собеседование, которое мы считаем очень эффективным мероприятием, т. к. это не только позволяет подтвердить письменные оценки квалификации специалиста, но создает условия его беседы с двумя специалистами III уровня и уточнения неясных для него вопросов.
Изложенная выше система по утверждению уровня квалификации специалиста документирована и способствует достоверности, объективности оценки знаний и практического опыта специалистов, а также обеспечивает меньшую степень зависимости результатов от того центра, в котором кандидат проходит сертификацию.
В этом случае, т. е. при соблюдении органами по сертификации одинаковых по содержанию и объемам экзаменационных материалов, идентичных по форме и содержанию процедур и протоколов организации и оценки уровня компетенции специалистов, отпадет необходимость в недоверии ряда ведомств к результатам сертификации и их предложении пройти повторную аттестацию в специально уполномоченных единичных центрах.
Эффективность описанного процесса подтверждается результатами обратной связи с заявителями, т. е. позитивными отзывами кандидатов и организаций.
Источник - статья Н. А. Быстровой, Д. И. Галкина, И. С. Хретинина опубликованная в журнале «В мире НК» № 2(48). 2010.
Другие статьи на тему аттестации специалистов и лабораторий неразрушающего контроля можно посмотреть в разделе Статьи.
Под сертификацией (аттестацией) специалистов НК подразумевается процедура подтверждения достаточности теоретической и практической подготовки, опыта, компетентности специалиста, т. е. его профессиональных знаний, навыков, мастерства, и предоставления права на выполнение работ по одному или нескольким видам (методам) НК [1]. Для осуществления сертификации применяются схемы сертификации – своеобразные фильтры, которые должны исключать возможность допуска к контролю потенциально опасных технических объектов специалистов, не обладающих достаточной квалификацией.
В настоящее время на территории РФ действуют несколько схем сертификации специалистов:
- на объектах, подведомственных Рос-технадзору, в соответствии с требованиями [1];
- объектах, подведомственных ОАО «Концерн Росэнергоатом», в соответствии с требованиями [2];
- на железнодорожном транспорте в соответствии с требованиями [3];
- на объектах ПАО «Транснефть» в соответствии с требованиями [4];
- в области авиации и космонавтики по российским и европейским нормам ([5, 6]);
- в области объектов Российского морского регистра судоходства (EN 473:2000, [5]);
- в соответствии с требованиями системы добровольной сертификации персонала НК [5];
- в соответствии с требованиями европейского стандарта [7].
Необходимость сертификации по той или иной схеме определяется видами объектов, на которых проводятся работы по НК. Необходимость проведения дополнительной аттестации в соответствии с требованиями [4] обусловлена наличием отраслевых требований к квалификации специалистов НК, допускаемых к выполнению работ на объектах ПАО «Транснефть» в части проведения, оценки и оформления результатов контроля. Процедуру дополнительной аттестации должны пройти специалисты НК для получения допуска к работе на объектах ПАО «Транснефть».
Последние две схемы сертификации являются полностью добровольными, и необходимость сертификации (аттестации) по этим системам диктуется заказчиком, т. е. относится к области договорных взаимоотношений. Так, например, трубы, изделия проката и другая продукция, изготавливаемая в РФ и поставляемая на территорию EC, должна быть проконтролирована в соответствии с требованиями европейских стандартов качества специалистами, сертифицированными согласно EN 473:2008
Параллельное развитие схем сертификации привело к отсутствию:
- единой терминологии по сертификации персонала;
- единых требований, предъявляемых к кандидату, для допуска к сертификации;
- единых требований к процедуре и порядку оценки квалификационного экзамена.
Табл. 1. Сравнение требований различных систем сертификации (аттестации)*
Критерий сравнения | Требования согласно | |||
[1] | [3] | [2] | [7] | |
Минимальные требования к стажу работы по данному методу НК | 18 мес. | 12 мес. | 36 мес. | 12 мес. |
Требования к состоянию здоровья и зрению | Медицинское заключение (справка) в соответствии с «Временным перечнем вредных, опасных веществ и производственных факторов, при работе с которыми обязательны предварительные и периодические осмотры работников …» | Отсутствие противопоказаний по состоянию здоровья и зрению. При сертификации по контролю маг-нитопорошковым методом – отсутствие дальтонизма | Медицинское заключение (справка) в соответствии с «Временным перечнем вредных, опасных веществ и производственных факторов, при работе с которыми обязательны предварительные и периодические осмотры работников …» | Чтение минимум таблицы Егера ¹ 1 или шрифта Times Rоmаn 4,5 одним или обоими глазами; возможность различать контраст между цветами или оттенками серого, используемыми в методе НК |
Минимальные сроки специальной подготовки | 120 ч | Требования отсутствуют. Подготовка должна проводиться в соответствии с программами, согласованными экспертной организацией по сертификации персонала НК | 120 ч | 144 ч |
Наличие собеседования | Да, по результатам практического экзамена | Да, по результатам общего экзамена | Да, по результатам теоретического экзамена | Нет |
Кандидат считается выдержавшим квалификационный экзамен, если: | суммарная оценка за экзамен не менее 80 %, но не менее 70 % по каждой части экзамена | оценка по каждой части экзамена не менее 80 % | суммарная оценка за экзамен не менее 80 %, но не менее 70 % по каждой части экзамена | оценка по каждой части экзамена не менее 70 % |
Срок действия квалификационного удостоверения | 3 года | 3 года | 3 года | 5 лет |
*на примере прямой (при отсутствии I уровня квалификации) сертификации на II квалификационный уровень по УЗК
Ошибка специалиста НК (дефекто-скописта, контролера), связанная с недостатком его квалификации, в равной степени недопустима на объектах, подведомственных Ростехнадзору, на железнодорожном транспорте, на объектах ОАО «Концерн Росэнергоатом». Очевидно, что пропуск дефекта на любом из этих объектов может привести к катастрофическим последствиям. Тогда непонятно: почему требования к квалификации специалистов НК, проводящих контроль этих объектов, различаются?
Для разрешения данного противоречия, на наш взгляд, необходимо привести существующие схемы сертификации к единой основе использования нормативных документов. В качестве базиса можно рассматривать СДАНК-02-2020. Данная схема сертификации также является наиболее апробированной, т. к. процедуру сертификации по СДАНК-02-2020 прошли по состоянию на начало 2010 г. более сорока тысяч специалистов НК.
Таким образом, опираясь на основные положения СДАНК-02-2020 и дорабатывая их в части вопросов, относящихся к отраслевой специфике, можно прийти к единообразию схем сертификации. Это позволит сделать всю систему сертификации в области НК более понятной, доступной и ориентированной, прежде всего, на потребителя услуг данного вида.
Кроме того, для обеспечения единообразия подходов при оценке результатов квалификационного экзамена должны быть разработаны и приняты во всех системах сертификации: – банк экзаменационных вопросов пофизическим основам методов НК; – требования к экзаменационным образцам (геометрическая форма, размеры, тип и максимальное количество дефектов) по различным методам НК в зависимости от отраслевой специфики; – методики оценки практического экзамена по различным методам НК; – порядок инспекционного контроля деятельности сертифицированного (аттестованного) специалиста.
Литература
1. СДАНК-02-2020. Правила аттестации персонала в области неразрушающего контроля. Утверждены постановлением Госгортехнадзо-ра России от 23 января 2002 г. ¹ 3. Зарегистрировано в Минюсте РФ 17 апреля 2002 г. Рег. ¹ 3378.
2. Порядок аттестации контролеров, выполняющих контроль металла на предприятиях ОАО «Концерн Росэнергоатом». Утв. 01.03.2010 г. Зам. Ген. директора ОАО «Концерн Росэнергоатом» – директором по производству и эксплуатации АЭС.
3. ПР 32.113 – 98. Правила сертификации персонала по неразрушающему контролю технических объектов железнодорожного транспорта. – М.: МПС России, 1998.
4. ОР-03.120.00-КТН-071-09. Требования к аттестации специалистов неразрушающе-го контроля, выполняющих работы на объектах ПАО «Транснефть».
5. СДСПНК РОНКТД (Система добровольной сертификации персонала неразрушающего контроля Российского общества по неразрушающе-му контролю и технической диагностике).
6. EN 4179. Авиация и космонавтика. Квалификация и допуск персонала неразрушающего контроля.
7. EN 473:2008. Квалификация и сертификация персонала неразрушающего контроля. Общие принципы.
Источник - статья С. А. Попоудина опубликованная в журнале «В мире НК» № 3(37). 2007.
Другие статьи на тему толщинометрии изделий можно посмотреть в разделе Статьи.
Ультразвуковая толщинометрия (УЗТ) находит широкое применение во многих отраслях народного хозяйства.
УЗТ позволяет оценивать толщину изделий в процессе производства и эксплуатации, а также выявлять расслоения в материале изделий.
В настоящее время, в связи с возросшими требованиями к точности проводимых измерений, на смену аналоговым ультразвуковым толщиномерам приходит аппаратура на основе микропроцессоров [1] с представлением информации на дисплее в виде А-развертки и В-развертки, с дополнительной информацией о фазе отраженного сигнала.
За последние десять лет в Беларуси, благодаря большой информационно-методической работе Белорусской ассоциации НК и технической диагностики (БАНК и ТД) и при ее содействии интенсивно идет замена морально и физически устаревших средств НК, в том числе и ультразвуковых толщиномеров.
Качество выполнения УЗТ зависит прежде всего от наличия и технического уровня технических нормативных правовых актов (ТНПА).
В странах СНГ в области УЗТ на сегодняшний день действуют ТНПА, которые разрабатывались более тридцати лет назад и не потеряли своей актуальности, а также разрабатываются новые документы и вводятся в качестве государственных международные и европейские стандарты. В общем случае, применительно к УЗТ, так же как и ко всем методам НК, стандарты можно разделить на следующие группы.
1. Термины и определения:
– ГОСТ 23829-85. Контроль неразруша-ющий акустический. Термины и определения.
– *СТБ ЕН 1330-4-2004. Контроль нераз-рушающий. Часть 4. Термины, применяемые при ультразвуковом контроле.
-----------------
* СТБ – Государственный стандарт Республики Беларусь.
2. Технические требования к СНК и методам контроля (включая требования к точности измерений):
– ГОСТ 18353-79. Контроль неразрушаю-щий. Классификация видов и методов.
– ГОСТ 20415-82. Контроль неразруша-ющий. Методы акустические. Общие положения.
– ГОСТ 28702-90. Контроль неразруша-ющий. Толщиномеры ультразвуковые. Общие технические требования.
– СТБ ЕН 583-2-2005. Контроль нераз-рушающий. Ультразвуковой метод. Часть 2. Настройка чувствительности и длительности развертки.
– СТБ ИСО/МЭК 17025-2001. Общие требования к компетентности испытательных и калибровочных лабораторий.
– ГОСТ 8.010-99. Государственная система обеспечения единства измерений. Методики выполнения измерений. Основные положения.
– СТБ ИСО 5725. Точность (правильность и прецизионность) методов и результатов измерений, части 1–6.
3. Метрологическое обеспечение СНК:
– ПМГ 06-2001. Порядок признания результатов испытаний и утверждения типа, поверки, метрологической аттестации средств измерений.
– ГОСТ 8.495-83. Толщиномеры ультразвуковые контактные. Методы и средства поверки.
Кроме перечисленных ТНПА в странах СНГ действуют нормативные документы (РД, ОСТ, ВСН, СНиП) по УЗТ различных объектов, например [2] и [3].
Опуская детальный анализ недостатков и взаимной несогласованности перечисленных ТНПА, остановимся на стандарте ЕN 14127 «Неразрушающий контроль. Ультразвуковые измерения толщины» [7], который был введен в действие в августе 2004 г. С февраля 2005 г. в странах Евросоюза он действует как национальный.
Рис. 1. Методы проведения измерений толщины ультразвуковым методом.
Согласно стандарту ЕN 14127:2004 оценка точности измерений выражается в виде неопределенности результатаизмерения. Оценка неопределенности измерений проводится в соответствии с ISO 14253-2 [8] «Спецификации на Геометрические Параметры Изделий (GPS) – Инспекция путем измерения рабочих заготовок и измерительного оборудования. Часть 2. Руководство по оценке неопределенности при измерениях GPS, при калибровке измерительного инструмента, а также верификации продукции», положения которого позволяют определить, когда результат измерения можно считать соответствующим показанию прибора. Стандарт ISO 14253-2 представляет интерес при рассмотрении процедуры по планированию и использованию неопределенности и, конечно же, требует отдельного рассмотрения.
Стандарт ЕN 14127:2004 устанавливает:
– основные требования к ультразвуковому методу измерения толщины;
– методы проведения измерения толщины (рис. 1);
– типы применяемой аппаратуры для проведения измерений;
– требования к квалификации персонала;
– факторы, влияющие на точность измерений (табл. 1);
– выбор аппаратуры, порядок настройки аппаратуры с цифровой индикацией и имеющей экран с А-разверткой;
- порядок и особенности технологии проведения измерений;
- оценку точности;
- составление отчета.
В стандарте ЕN 14127:2004 приводятся информативные приложения в виде таблиц и схем:
- возможные виды коррозии сосудов и трубопроводов;
– особенности настройки аппаратуры;
– учет параметров, влияющих на точность измерений;
– схемы проведения контроля с учетом особенностей при проведении измерений в процессе производства или эксплуатации с рекомендациями по выбору аппаратуры и др.
Исходя из содержания рассматриваемого стандарта, можно сказать о том, что он достаточно полно раскрывает особенности УЗТ и может служить в качестве основы для совершенствования и разработки ТНПА.
В соответствии с ЕN 14127:2004 специалист, выполняющий УЗТ, должен знать физические основы ультразвука, а также иметь теоретические и практические навыки измерения толщины ультразвуковым методом. Кроме этого, оператор должен иметь информацию о конструкции объекта контроля и его материале, особенностях эксплуатации, возможном состоянии его обратной поверхности. В качестве подтверждения своей квалификации специалист должен иметь сертификат в соответствии со стандартом EN 473 или его эквивалентом.
Точность проведения измерений с помощью ультразвука – это тот важный момент, который выделяет УЗТ из области дефектоскопии и должен быть учтен при подготовке специалистов, проводящих ультразвуковые измерения толщины. Специалист должен знать, с какой точностью он должен выполнять измерения и как ее добиться при проведении измерений. Практика показывает, что персонал, имеющий сертификат по ультразвуковой дефектоскопии, в курс обучения которого не входила углубленная подготовка по обеспечению точности проведения измерений ультразвуковым методом, не сможет качественно выполнить задачу, связанную с оценкой остаточной толщины изделия в процессе эксплуатации. Очевидно, что сертификация специалистов для этого направления весьма актуальна [9].
Выводы:
1. Ввести в качестве межгосударственного стандарта европейский стандарт ЕN 14127:2004. Эту работу мог бы взять на себя межгосударственный комитет по НК МТК 515 «Неразрушающий контроль».
2. Ввести сертификацию персонала по ультразвуковой толщинометрии, для чего разработать программы подготовки специалистов для целей сертификации, схемы сертификации, экзаменационные вопросы и т. д.
Литература
1. Гиллер Г. А., Могильнер Л. Ю. Современные ультразвуковые толщиномеры. Новые возможности. – «В мире НК». 1999. № 5. С. 6–9.
2. ПНАЭ Г 7-031-91. Унифицированные методики контроля основных материалов (полуфабрикатов), сварных соединений и наплавки оборудования и трубопроводов атомных энергетических установок. Ультразвуковой контроль. Часть ІІІ. Измерение толщины монометаллов, биметаллов и антикоррозионных покрытий. – М.: ЦНИИ атоминформ, 1992.
3. РД РОСЭК 006-97. Машины грузоподъемные. Толщинометрия ультразвуковая. Основные положения. – М.: Машиностроение, 1998.
4. Руководство по выражению неопределенности измерения. Перевод с англ. Под науч. ред. проф. Слаева В. А. – СПб.: ГП ВНИИМ им. Д. И. Менделеева, 1999.
5. СТБ ИСО 5725-1-2002. Точность (правильность и прецизионность) методов и результатов измерений. Часть 1. Общие принципы и определения. – Минск: БелГИСС, 2002.
6. Руководство ЕВРАХИМ/СИТАК. Количественное описание неопределенности в аналитических измерениях. 2-е издание, 2000, перевод с англ. Р. Л. Кадиса, Г. Р. Нежиховского, В. Б. Силенка под общей редакцией Л. А. Конопелько. – СПб.: ВНИИМ им. Д. И. Менделеева, 2002.
7. ЕN 14127:2004 (Е). Non-Destructive Testing – Ultrasonic Thickness Measurement.
8. ISO/TS 14253-2:1999(E) Geometrical Product Specifications (GPS) – Inspection by Measurement of Workpieces and Measuring Equipment – Part 2: Guide to Estimation of Uncertainty in GPS Measurement, in Calibration of Measuring Equipment and in Product Verification.
9. Попоудина С. А. Развитие системы сертификации персонала в области НК в Республике Беларусь. – В мире НК. 2005. № 4(30). С. 54–55.
Табл. 1. Таблица параметров, влияющих на точность измерений
Основные области | Параметры | Результат | |
Объект контроля | Материал | Химический состав | Ослабление, поглощение, рассеяние и местные вариации скорости |
Структура | |||
Анизотропия | |||
Состояние поверхности |
Отсутствие загрязнений |
Локальные изменения состояния поверхности ведут к местным вариациям скорости | |
Шероховатость | |||
Профиль поверхности | |||
Покрытие | Покрытие | Скорость распространения ультразвука в покрытии отличается от скорости ультразвука в основном материале, что является результатом неточности | |
Лакокрасочное | |||
Обработка поверхности | |||
Геометрические параметры | Непараллельность | Исчезновение отраженного сигнала или его искажение | |
Криволинейность | Снижение эффективности контактной смазки | ||
Измеряемый диапазон | Искажение, искривление отраженного сигнала вследствие ослабления | ||
Настройка для проведения измерений | Метод калибровки | Неопределенность метода калибровки | Неопределенность показаний прибора |
Reference блок или стандартный образец предприятия (СОП) | Неопределенность, связанная с толщиной и скоростью | Точность не может быть выше той, которая связана с неопределенностью Reference блока или СОП | |
Проведение измерений | Оборудование | Точность измерений | Точность выполненных измерений не может быть выше точности аппаратуры |
Длина кабеля | Излишняя длина кабеля причина искажения сигналов | ||
Колебание параметров аппаратуры | Неточность показаний прибора | ||
Временной путь ультразвука |
Точность выполненных измерений не может быть выше точности измерения временного пути ультразвука |
||
Линейность | Неточность показаний прибора | ||
Точка отсчета | Неточность показаний прибора | ||
Операция | V-образный путь | Неверные показания, имеющие связь с путем ультразвука в материале изделия и его толщиной | |
Изменение фазы | Ошибочные показания | ||
Повторяемость | Составные части | Метод | Неправильные действия |
Контактная смазка | Плохая контактная смазка способствует отсутствию стабильности показаний | ||
Подготовка специалиста | Ошибочное толкование | ||
Прочее | Температура | Вариации скорости ультразвука | Ошибочное толкование |
Источник - статья А. К. Гурвича опубликованная в журнале «В мире НК» № 2(40). 2008.
Другие статьи на тему толщинометрии изделий можно посмотреть в разделе Статьи.
Материал подготовили А. К. Гурвич, В. А. Сясько, Б. В. Артемьев, А. Я. Грудский, Ю. К. Федосенко, В. Г. Шевалдыкин с учетом действующих ГОСТ, ряд из которых требует пересмотра.
Авторы полагают, что первая редакция данной таблицы будет развита и дополнена читателями журнала. Файл с таблицей может быть выслан редакцией журнала для корректировки по запросу читателей в июле-августе этого года.
---------------
*ПЭП - пьезоэлектрический преобразователь; ЭМАП - электромагнитно-акустический преобразователь; АР - антенная решетка
Источник - статья Е. Ф. Кретова опубликованная в журнале «В мире НК» № 2(40). 2008.
Другие статьи на тему толщинометрии изделий можно посмотреть в разделе Статьи.
Как правило, ультразвуковой метод измерения толщины применяют в таких местах металлоконструкций, которые недоступны или труднодоступны для измерения механическим измерительным инструментом. Особенно широко этот метод используют для определения толщины стенок труб, котлов, сосудов, то есть объектов замкнутого типа или с односторонним доступом. Обычно измерения производят на эквидистантных (равноудаленных друг от друга) поверхностях или участках поверхности, хотя принципиально возможны измерения и в других случаях.
По физическим принципам, используемым для измерения толщины, акустические толщиномеры делят на эхо-импульсные и резонансные. Принцип ультразвуковой толщинометрии импульсными приборами основан на измерении времени прохождения ультразвукового импульса в изделии или в слое и умножении измеренного времени на коэффициент, учитывающий скорость звука в материале изделия. В резонансных приборах для измерения толщины используется локальный резонансный метод или локальный метод свободных колебаний, а также интерференционные явления, возникающие при распространении акустических волн в изделии.
Резонансный метод позволяет измерять толщину от минимального значения
hmin= 0,5с/fmax
где с - скорость звука в материале изделия; fmax - максимальная частота прибора [1].
При повышении частоты до 30 МГц можно измерять толщины стальных изделий, начиная с 0,1 мм. Измерение таких толщин эхо-методом выполнить не удается. Использование иммерсионного варианта метода обеспечивает непрерывный контроль труб диаметром 3-^4 мм и более, что также трудно обеспечить другими методами; погрешность составляет при этом 1-^2%. Резонансный метод применяют для контроля изделий с гладкими поверхностями. Изменение толщины в зоне измерения не должно превышать 8 %, при этом измеряется средняя толщина, а не наименьшее ее значение. Этими возможностями определена область преимущественного использования резонансных толщиномеров для измерения толщины при автоматическом контроле тонкостенных труб малого диаметра в иммерсионном варианте. В остальной области повсеместно применяют ультразвуковые эхо-импульсные толщиномеры - простые в управлении и компактные приборы, позволяющие с хорошей точностью измерять толщину > 0,5 мм.
Долгое время измерение толщины ультразвуковым эхо-методом воспринималось со стороны такой же простой операцией, как измерение линейкой. Действительно: поставили искатель в указанную точку на изделии и считали результат. При использовании толщиномеров в лучшем случае руководствовались инструкцией по эксплуатации прибора. Первый отраслевой стандарт в этой области [2] (далее - ОСТ), распространяющийся на изделия судовой техники, появился в 1985 г., то есть существенно позже стандартов (инструкций) по ультразвуковому контролю сплошности материалов и сварных соединений. В1992 г. введен в действие отраслевой методический документ по толщинометрии в атомной энергетике [3] (далее - ПНАЭ), а в 1998 г. - методика измерения толщины элементов грузоподъемных машин [4] (далее - РД РОСЭК). Рассмотрим основные положения технологии ультразвуковой толщинометрии на основе этих трех документов.
Общие положения
В стандартах отмечается, что толщинометрия способом однократных измерений применяется в местах, недоступных для измерения механическим измерительным инструментом. Ее выполняют при изготовлении изделий, их эксплуатации, техническом диагностировании и экспертном обследовании. Измерения выполняют дискретно в запланированных точках на ОК. Необходимость проведения измерений толщины ультразвуковым методом, объем измерений, конкретные точки для измерений и критерии оценки результатов должны быть оговорены в производственно-конструкторской документации.
Современные толщиномеры позволяют производить сплошное (непрерывное) измерение толщины с сигнализацией (или регистрацией) выхода измеряемой толщины за указанные пределы. Однако технология такого контроля в рассматриваемых документах не предусмотрена.
ОСТ и ПНАЭ не ограничивают диапазон измеряемых толщин. РД ограничивает измеряемые толщины диапазоном 2,5 - 60,0 мм. Это ограничение связано с толщинами реально существующих элементов грузоподъемных машин.
Рис. 1. Стандартный образец предприятия для настройки дефектоскопа при измерении толщины антикоррозионной наплавки
ОСТ и РД РОСЭК регламентируют измерение толщины монометаллических элементов, область применения ПНАЭ распространяется дополнительно на биметаллические изделия, а также на антикоррозионные покрытия из сталей аустенитного класса на изделиях из сталей перлитного класса.
К работе по измерению толщины допускаются дефектоскописты, аттестованные по правилам, действующим в соответствующей отрасли, и изучившие отраслевой стандарт по толщино-метрии. Руководство работами по измерению толщины, периодическая проверка качества его исполнения и оформление заключений по его результатам возлагается на инженерно-технических работников в соответствии с правилами, действующими в отрасли.
Средства контроля
РД РОСЭК регламентирует для целей толщинометрии применение ультразвуковых толщиномеров с цифровой или стрелочной индикацией результатов. Как известно, в функциональной схеме толщиномера реализуются дополнительные относительно дефектоскопа блоки, позволяющие повысить точность измерений (например, автоматическая регулировка усиления для стабилизации амплитуды первого донного сигнала) или дополнительные требования к блокам (короткий и крутой зондирующий импульс, широкополосность) [5]. Поэтому применение толщиномеров при контроле толщин примерно до 100 мм более оправдано, чем дефектоскопов. Однако при толщинах элементов более 100 мм, которые встречаются в судовых конструкциях и характерны для оборудования атомных электростанций (АЭС), чувствительности толщиномеров не всегда достаточно, а измерение толщины антикоррозионных покрытий вообще возможно только дефектоскопом. Поэтому ультразвуковые дефектоскопы включены в состав средств измерения толщины в методиках ОСТ и ПНАЭ.
При использовании толщиномеров следует применять пьезоэлектрические преобразователи (ПЭП), которые входят в комплект толщиномера. Чаще всего это прямые раздельно-совмещенные (PC) ПЭП, иногда применяют прямые совмещенные ПЭП сзадержкой. Взависимости от измеряемой толщины используют ПЭП с частотой из диапазона 2,0 - 10,0 МГц. При измерении толщины монометаллов и биметаллов дефектоскопами используют прямые совмещенные ПЭП с жестким протектором. Толщину антикоррозионного покрытия измеряют прямыми совмещенными (со стороны основного металла) или PC ПЭП (со стороны покрытия). Используют частоты 2,0 - 5,0 МГц.
Для настройки прибора применяют стандартные образцы предприятия (СОП), изготовленные из материала ОК. Основные требования к СОП: воспроизведение скорости звука, формы и состояния поверхности соответствующим параметрам ОК. Так, например, если ставится задача измерения толщины объекта с лакокрасочным покрытием, образец должен иметь покрытие, выполненное по такой же технологии. В тех случаях, когда ОК имеет малый радиус кривизны (менее 50 мм), сложную криволинейную форму поверхности (гибытруб), необходимо применять СОП в виде фрагментов соответствующих изделий. Обычно рекомендуют иметь СОП со ступенями минимально и максимально допустимой толщины. Пример СОП для измерения толщины антикоррозионной наплавки приведен на рис. 1.
Средства контроля должны быть паспортизованы и проходить поверку в установленном порядке.
Подготовка к контролю
Перед проведением измерений необходимо произвести настройку прибора. Конкретные способы настройки для каждого прибора определены инструкцией по эксплуатации, однако они всегда содержат две операции: настройка нуля (т.е. момента входа ультразвукового импульса в ОК) и настройка на скорость звука в ОК. Настройка нуля в современных толщиномерах может быть выполнена без применения внешних образцов. Настройку на скорость звука в ОК осуществляют по СОП. Точность настройки проверяют по нижней и верхней границам диапазона измерений.
Для измерения толщины монометалла или биметалла подготавливают площадку размером 30x30 мм2 с центром в точке измерения. В случае измерения толщины наплавки готовят площадку размером 50x50 мм2. Больший размер площадки связан с тем, что не в каждой точке ОК можно получить отчетливый эхо-сигнал от зоны сплавления основного металла с наплавкой. Иногда для этого требуется произвести небольшие перемещения ПЭП около намеченной точки измерения. Подготовленная площадка должна быть свободна от загрязнений, отслаивающейся окалины или краски. Шероховатость поверхности со стороны ввода ультразвуковых колебаний должна быть R < 6,3 мкм по ГОСТ 2789-73.
Чем более точно необходимо произвести измерение, тем более жесткие требования предъявляются к состоянию обеих поверхностей ОК. Нетсмысла требовать погрешность измерения 8 < 0,1 мм на объекте с корродированной поверхностью.
При измерении толщины на участках удаления поверхностных дефектов для установки ПЭП должна быть подготовлена площадка диаметром 15 мм, параллельная поверхности изделия. Преобразовательдолжен плотно прилегать к поверхности изделия. В некоторых случаях измерение может быть выполнено со стороны, противоположной выборке. Если выборка имеет крутой профиль, не позволяющий обеспечить плоскую площадку для установки ПЭП, измеряют толщину в точках вокруг выборки. Глубину выборки измеряют микрометрическим или индикаторным глубиномером. Толщину в месте выборки находят как разность между минимальной толщиной в окрестности выборки и глубиной выборки.
В соответствии с ПНАЭ температура окружающего воздуха и ОК должна находиться в пределах 5 - 40 "С. ОСТ и РД РОСЭК позволяют выполнять измерения в диапазоне температур, разрешенном инструкцией по эксплуатации применяемого толщиномера. По данным американской спецификации SE-797 каждое увеличение температуры на 55 °С влечет за собой уменьшение скорости звука в стали на 1% [6].
Проведение измерений
Перед началом измерений необходимо ознакомиться с документацией на измеряемый объект и, если возможно, составить представление об ожидаемом состоянии донной поверхности.
На каждый размеченный участок наносят контактную жидкость, устанавливают ПЭП и тщательно притирают к поверхности ОК, добиваясь минимального устойчивого показания. При измерении толщины трубопроводов экран PC ПЭП должен быть ориентирован перпендикулярно образующей трубы. Причиной отсутствия показаний могут быть плохой акустический контакт (например, из-за плохого качества контактной поверхности), язвенная коррозия донной поверхности, отсутствие эквидистантности поверхностей, наличие элемента, приваренного к донной поверхности, наличие внутреннего дефекта материала в месте измерения и др.
При измерении толщины ультразвуковыми дефектоскопами следует проводить и настройку, и измерение в режиме «по фронту». Для уменьшения погрешности настройку и измерение необходимо выполнять при одинаковой высоте эхо-сигнала.
При измерении толщины в местах язвенной и пятнистой поверхности коррозии внутренней поверхности прибор фиксирует отдельные язвины сферической формы размером более 2,5 ч- 3,0 мм. Для определения участка наименьшей толщины приходится выполнять измерения с малым шагом (до Змм и меньше). О наличии пятнистой или язвенной коррозии говорят скачущие показания прибора на небольшом участке измерений.
Считывание результата измерения проводят после получения устойчивого и достоверного показания. Для цифрового прибора оно характеризуется либо одним значением, либо двумя, изменяющимися в пределах дискретности прибора. В последнем случае записывают значение, ближайшее к границе допуска на размер. Если возникает сомнение в правильности показаний толщиномера, участок измерения целесообразно проверить дефектоскопом.
Возможность измерения толщины антикоррозионной наплавки основана на том, что акустические сопротивления основного металла и антикоррозионной наплавки несколько отличаются (z1 = 4,6 х 107 кг-м~2/с; z2 = 4,2 х 107 кгм~2/с), следовательно, на границе сплавления образуется отраженная ультразвуковая волна, которая регистрируется ультразвуковым дефектоскопом. При измерении со стороны основного металла толщина наплавки рассчитывается как разность показаний полной толщины объекта и толщины основного металла (рис. 2).
Рис. 2. Схема измерения толщины антикоррозионной наплавки со стороны основного металла
Измерение со стороны наплавки усложняется тем, что материал наплавки представляет собой литую аустенитную крупнозернистую структуру. Поскольку коэффициент отражения от границы раздела наплавка-основной металл довольно мал (расчетный коэффициентбез учета диффузного рассеяния Rp = 0,035), требуется установить высокую чувствительность для получения сигнала от границы сплавления. При этом может оказаться, что структурный шум из объема наплавки не позволит выявить сигнал от зоны сплавления. Для оптимизации измерения в этом случае выбирают такой PC ПЭП, у которого фокусное расстояние больше толщины наплавки (рис. 3).
Рис. 3. Схема к выбору PC ПЭП для измерения толщины наплавки со стороны наплавки: А-амплитуда сигнала от отражателя в виде плоскости; r - расстояние от поверхности ввода до отражателя
При этом оказывается, что чувствительность ПЭП в области зоны сплавления всегда выше, чем в материале наплавки, следовательно, можно ожидать, что уровень структурных шумов позволит выделить сигнал от зоны сплавления.
Ошибки измерений
При измерениях могут возникать ошибки трех видов.
Грубыми называют такие ошибки (промахи), при которых получают результат, существенно отличающийся от ожидаемого в данных условиях. Для надежного выявления промаха нужно либо повторить измерение спустя некоторое время, когда контролер уже «забыл» полученный им результат, либо произвести независимое повторное измерение, начиная с настройки прибора, другим контролером. Иногда промах можно легко выявить при беглом просмотре результатов измерений, если какой-то результат явно выпадает из общего ряда.
Систематические - это такие ошибки, величина которых одинакова или закономерно изменяется во всех измерениях, проводимых одним и тем же методом с помощью одних и техже приборов. При ультразвуковой толщинометрии такая ошибка возникает при неправильной настройке задержки нуля или скорости ультразвука.
Указанные два вида ошибок можно минимизировать путем тщательной настройки прибора и внимательном и аккуратном проведении измерений и записи результатов. Наиболее сложно уменьшать величину случайных ошибок, которые изменяются случайным образом при повторных измерениях одной и той же величины. Случайные ошибки возникают из-за:
- колебаний технических параметров в допустимых пределах;
- смещения ПЭП при повторных его установках в точку измерения;
- колебания толщины прослойки контактной жидкости из-за неравномерного прижима ПЭП к изделию;
- срабатывания прибора по разным периодам колебаний в радиоимпульсе;
- других факторов.
Величину случайной ошибки можно уменьшить путем проведения многократных (3-5) измерений в одной точке. Погрешность измерений определяется преимущественно случайными ошибками. Экспериментальное определение погрешности измерений основано на статистической обработке многократных измерений в нескольких точках и сравнении результатов измерений с действительной толщиной [2]. В общем случае погрешность измерений в машиностроении принимают равной +(-) 0,2 мм при измеряемой толщине Н до 20 мм и 0,01Н при толщине более 20 мм. Для дальнейшего уменьшения погрешности измерений следует:
- проводить измерение при отношении максимального к минимальному значению толщин не более 2;
- использовать для настройки две ступени СОП из материала ОК: одну - с максимальной, вторую - с минимальной допустимой толщиной;
- производить настройку прибора по точке ОК, в которой известно точное значение толщины.
При этих условиях можно добиться погрешности измерений, равной дискретности показаний прибора.
Погрешность измерения толщины антикоррозионной наплавки связана не с техническими параметрами прибора или технологическими особенностями процесса измерения, а с колебаниями положения зоны сплавления в пределах падающего на нее пучка ультразвуковых колебаний, другими словами - с технологией выполнения самой наплавки. Установленная погрешность измерений толщины антикоррозионной наплавки, выполненной ленточными электродами, составляет +(-) 1,0 мм [3].
Форма записи результата измерений
Результат измерений должен быть представлен в виде:
x, d от dн до dв; Р, где х, мм - номинальное значение результата измерения; dн, dв - нижний и верхний пределы погрешности измерения; Р - вероятность, с которой погрешность находится в этих границах.
Пример: 22,3 мм +(-) 0,2 мм; Р = 0,972.
Значение доверительной вероятности допускается не указывать, если Р = 0,95.
При оформлении результатов нескольких измерений, выполненных в одинаковых условиях и имеющих одинаковые показатели точности (d и Р), их указывают один раз для всех результатов измерений.
Литература
1. Ермолов И. Н., Ланге Ю. В. Ультразвуковой контроль. - В кн.: Неразрушающий контроль/ Справочник// Под общ. ред. В. В. Клюева. Т. 3.
- М.: Машиностроение, 2004. - 864 с.
2. ОСТ 5Р.5550-85. Отраслевой стандарт. Контроль неразрушающий. Полуфабрикаты и изделия металлические. Ультразвуковой метод измерения толщины. - М.: Изд-во стандартов, 1985.
3. ПНАЭ Г-7-031-91. Унифицированные методики контроля основных материалов (полуфабрикатов), сварных соединений и наплавки оборудования и трубопроводов атомных энергетических установок. Ультразвуковой контроль. Часть III. Измерение толщины монометаллов, биметаллов и антикоррозионных покрытий. - М.: ЦНИИатом-информ, 1992. Не действует - Не подлежит применению.
4. РД РОСЭК-006-97. М. Машины грузоподъемные. Конструкции металлические. Толщино-метрия ультразвуковая. Основные положения.
- М.: Машиностроение, 1998.
5. Алешин Н. П. и др. Методы акустического контроля металлов. - М.: Машиностроение, 1989. - 456 с.
6.ASME Code, секция V, раздел V, статья 23, спецификация SE-797. Типовая методика измерения толщины ручным ультразвуковым эхо-импульсным методом.
Аттестация персонала, выполняющего контроль качества оборудования и трубопроводов на действующих АЭС
Источник - статья В. Н. Ловчева опубликованная в журнале «В мире НК» № 2(48). 2010.
Другие статьи на тему аттестации специалистов и лабораторий неразрушающего контроля можно посмотреть в разделе Статьи.
Вопросам подготовки и аттестации специалистов по неразрушающим и разрушающим (лабораторным) методам контроля оборудования и трубопроводов в атомной энергетике уделяется большое внимание. В первую очередь это связано с пониманием опасности потенциальных последствий, связанных с аварийными ситуациями в атомной энергетике.
В 1970-х гг. Национальный аттестационный комитет (НАК) инициировал разработку первых общесоюзных документов по обучению и аттестации специалистов по НК объектов, подконтрольных Госгортехнадзору России.
В атомной отрасли еще до образования НАК с 1960-х гг. уже действовала система подготовки и аттестации специалистов на базе ведущих отраслевых институтов (ЦНИИ «Прометей», НПО «НИКИМТ», НПО «ЦНИИТМАШ»), работающих по проблематике атомной отрасли.
В этих организациях с учетом отечественного и международного опыта были разработаны типовые и специальные программы по теоретической и практической подготовке и аттестации работников, занятых контролем качества сварных соединений и основного металла. Одновременно был разработан порядок аттестации, предусматривающий допуск их к работе с правом выдачи заключений о качестве продукции (СПВЗ) и без права выдачи заключений (БПВЗ). Наиболее квалифицированные специалисты СПВЗ проходили аттестацию в качестве членов аттестационной комиссии.
Комплект этих документов утверждался на уровне Министерств и Главных управлений, приказами по которым полномочия Головных отраслевых ма-териаловедческих организаций, впоследствии Головных материаловедче-ских организаций (ГМО), были даны указанным выше ЦНИИ «Прометей», НПО «НИКИМТ» и «ЦНИИТМАШ». Документы по аттестации персонала согласовывались соответствующими надзорными органами.
Такая система подготовки и аттестации персонала имела как положительные, так и отрицательные стороны.
Положительной стороной можно считать наличие в ГМО высококвалифицированных специалистов, знающих специфику атомной энергетики, а также научно-производственной инфраструктуры, на базе которой проходила подготовка и аттестация персонала, что в условиях жесткой централизованной системы управления позволяло обеспечивать компетентное и ответственное выполнение данных работ.
Очевидный недостаток такой системы – консервативность и узковедомственные возможности, недостаточно учитывающие передовой отечественный и международный опыт.
Отечественные «Правила аттестации персонала в области неразрушающего контроля» (СДАНК-02-2020) [1], которые были разработаны на базе Европейских правил аттестации персонала ЕN 473, соответствуют Концепции управления Системой НК [2].
Система НК – совокупность участников, которые в рамках регламентирующих норм, правил, методик, условий, критериев и процедур осуществляют деятельность в области одного из видов экспертизы промышленной безопасности, связанной с применением НК
В Системе НК аттестация персонала является одним из ее элементов наряду с аттестацией лабораторий, методических документов и средств НК. Следует отметить, что в Системе НК разработан взаимосвязанный комплекс документов, регламентирующих основные вопросы, входящие в ее компетенцию. В настоящее время основным документом по аттестации персонала по НК в атомной энергетике являются ПНАЭ Г-7-010-89 [3]. Этот документ содержит раздел «Аттестация контролеров», согласно которому «аттестация контролеров (специалистов, дефектоскопистов, лаборантов ОТК, непосредственно выполняющих контроль) осуществляется путем проверки их теоретических знаний и практических навыков по контролю конкретными методами».
Основными методическими документами по НК, которые применяются при реализации требований [3] в части аттестации контролеров, являются:
– ПНАЭ Г-7-016-89 (визуальный и измерительный контроль); – ПНАЭ Г-7-017-89 (радиографический контроль);
– ПНАЭ Г-7-019-89 (контроль герметичности);
– ПНАЭ Г-7-014-89, часть I; ПНАЭ Г-7-030-89, часть II; ПНАЭ Г-7-031-89, часть III; ПНАЭ Г-7-032-89, часть IV (ультразвуковой контроль);
– ПНАЭ Г-7-018-89 (капиллярный контроль);
– ПНАЭ Г-7-015-89 (магнитопорошко-вый контроль).
В связи с необходимостью отражения в атомной энергетике современных тенденций по аттестации персонала и постепенного перехода в общероссийскую Систему НК с учетом специфики атомной отрасли ОАО НПО «ЦНИИТМАШ» разработал «Порядок аттестации контролеров, выполняющих контроль металла на действующих АЭС» [4]. Этот документ развивает основные положения [3]. В частности, аттестация персонала должна проводиться постоянно действующими аттестационными комиссиями (ПДАК) на предприятиях ОАО «Концерн Росэнергоатом» и/или в Аттестационных органах специализированных организаций, к которым относятся ГМО и другие организации (структурные подразделения), имеющие опыт работы в атомной энергетике не менее 5 лет и получившие от Ростехнадзора разрешение или подтверждение полномочий на право проведения аттестации персонала с перечислением методов контроля. Аттестационный орган должен быть признан эксплуатирующей организацией – ОАО «Концерн Росэнергоатом». Члены ПДАК должны проходить периодическую аттестацию в Аттестационном органе по разработанным этим органом программам.
Программы по теоретическим вопросам должны быть общими для всех ПДАК и Аттестационных органов, а экзаменационные вопросы ПДАК на предприятиях ОАО «Концерн Росэнергоатом» и в каждом Аттестационном органе могут быть разными.
Экзаменаторы Аттестационного органа, кроме требований, предъявляемых к контролерам высшего уровня квалификации, должны:
– иметь, как минимум, пятилетний стаж работы в области атомной энергетики;
– являться разработчиками (соавторами) методических, нормативных или технических документов, утвержденных и внедренных на предприятиях атомной энергетики;
– пройти проверку на знание Правил и норм в области использования атомной энергии и руководящих документов Ростехнадзора РФ с оформлением соответствующих удостоверений;
– руководствоваться порядком и требованиями к аттестации персонала [4].
Основной функцией Аттестационного органа и ПДАК предприятий ОАО «Концерн Росэнергоатом» является объективное определение уровня квалификации персонала, занятого в области контроля оборудования и трубопроводов атомных энергетических установок. Обязательным требованием к Аттестационному органу является отсутствие административной, финансовой, юридической и нормативной зависимости от юридических и физических лиц, заинтересованных в результатах аттестации.
Виды аттестации
Аттестация подразделяется на первичную, дополнительную, периодическую и внеочередную [3, 4].
Первичную аттестацию проходят кандидаты, не имевшие ранее удостоверения на право непосредственного выполнения соответствующего контроля и прошедшие теоретическую подготовку по специальной программе.
Дополнительную аттестацию проходят контролеры, прошедшие первичную аттестацию, перед допуском к выполнению работ, не указанных в их удостоверениях, при введении в действие новых методических документов по контролю, а также после перерыва в выполнении соответствующих работ по контролю свыше шести месяцев.
Периодическую аттестацию проходят все контролеры в целях продления срока действия их удостоверений. Периодическая аттестация по проверке теоретических знаний проводится не реже одного раза в три года, а проверка практических навыков – не реже одного раза в год.
Внеочередную аттестацию проходят контролеры перед допуском к выполнению контроля после временного отстранения от работы за нарушение технологии контроля.
Кандидаты на квалификационный уровень должны проходить первичную аттестацию в Аттестационных органах. Дополнительная, периодическая и внеочередная аттестации проводятся в ПДАК и/или в Аттестационных органах.
Уровни квалификации
Порядок аттестации контролеров оборудования и трубопроводов АЭС устанавливает три уровня квалификации при контроле:
– БПВЗ – проведение контроля без права выдачи заключения по результатам контроля;
– СПВЗ – проведение контроля с правом выдачи заключения по результатам контроля;
– СПА – проведение контроля с правом выдачи заключения по результатам контроля и правом аттестации контролеров в качестве члена ПДАК.
При проведении контроля с использованием автоматизированных систем контроля устанавливаются те же три уровня профессиональной квалификации – БПВЗ, СПВЗ, СПА. В этом случае кандидаты проходят дополнительную аттестацию с учетом специфики работы автоматизированных средств контроля и особенностей требований соответствующих методических документов.
Требования к общей и специальной подготовке персонала
Кандидат, претендующий на присвоение квалификационного уровня, должен иметь общее образование, теоретическую и практическую подготовку в соответствии с требованиями табл. 1.
Для допуска к экзаменам на соответствующий квалификационный уровень кандидат должен пройти предаттестаци-онную подготовку по определенному методу контроля в соответствии с программой Аттестационного органа. К аттестации допускаются кандидаты, не имеющие противопоказаний по состоянию здоровья и представившие соответствующее медицинское заключение (справку).
Аттестация в Аттестационном органе
Требования к Аттестационной комиссии
Состав Аттестационной комиссии в Аттестационном органе утверждается Приказом по предприятию.
Для приема экзаменов на уровни квалификации БПВЗ и СПВЗ в комиссии Аттестационного органа должно быть не менее двух контролеров с уровнем СПА. Для приема экзаменов у членов ПДАК предприятий ОАО «Концерн Росэнергоатом» на уровень СПА в Аттестационном органе должно быть не менее трех контролеров с уровнем СПА.
Требования к аттестации персонала
К первичной аттестации допускаются кандидаты, прошедшие теоретическую предаттестационную подготовку по программе, включающей вопросы физики данного метода контроля, технологию и специфику контроля объектов, подведомственных Федеральной службе по экологическому, технологическому и атомному надзору.
Первичная аттестация состоит из двух экзаменов – теоретического и практического. При первичной аттестации кандидата после теоретического экзамена проводится проверка практических навыков по данному методу контроля на экзаменационных образцах.
Уровень квалификации | Требования: | ||
к общему образованию | к специальной подготовке | к стажу по данному виду НК | |
1 | 2 | 3 | 4 |
БПВЗ | Среднее. Средне-техническое. Средне-специальное. Высшее | Подготовка на специальных курсах или по месту работы в подразделениях НК по программе, согласованной с Аттестационным органом | Нет |
СПВЗ | Один год | ||
СПА | Средне-техническое. Средне-специальное. Высшее | Знание учебных пособий, нормативно-методических документов, подготовка контролеров БПВЗ и СПВЗ, участие в конференциях и семинарах. | Иметь уровень квалификации СПВЗ и стаж работы не менее 5 лет |
Табл. 1. Общие требования к подготовке кандидатов на первичную аттестацию
Метод контроля |
Общее количество вопросов в сборнике, не менее |
Количество вопросов, задаваемых на экзамене на уровни квалификации |
||
БПВЗ | СПВЗ | СПА | ||
ТЕОРЕТИЧЕСКИЙ ЭКЗАМЕН | ||||
ЧАСТЬ 1 – ФИЗИЧЕСКИЕ ОСНОВЫ | ||||
Визуальный и измерительный (ВИК) | 60 | 30 | 30 | 40 |
Капиллярный (КК) | 60 | 30 | 30 | 30 |
Магнитопорошковый (МПК) | 80 | 40 | 40 | 40 |
Ультразвуковой (УЗК) | 80 | 40 | 40 | 40 |
Радиографический (РГК) | 80 | 40 | 40 | 40 |
Контроль герметичности (КГ) | 60 | 30 | 30 | 30 |
Вихретоковый (ВТК) | 80 | 40 | 40 | 40 |
Акустико-эмиссионный (АЭ) | 80 | 40 | 40 | 40 |
Телевизионный (ТВК) | 60 | 30 | 30 | 30 |
Телевизионный измерительный (ТИК) | 80 | 40 | 40 | 40 |
ЧАСТЬ 2 – НОРМАТИВНЫЕ И МЕТОДИЧЕСКИЕ ДОКУМЕНТЫ | ||||
Визуальный и измерительный (ВИК) | 60 | 20 | 20 | 20 |
Капиллярный (КК) | 60 | 20 | 20 | 20 |
Магнитопорошковый (МПК) | 60 | 20 | 20 | 20 |
Ультразвуковой (УЗК) | 60 | 20 | 20 | 20 |
Радиографический (РГК) | 60 | 20 | 20 | 20 |
Контроль герметичности (КГ) | 60 | 20 | 20 | 20 |
Вихретоковый (ВТК) | 60 | 20 | 20 | 20 |
Акустико-эмиссионный (АЭ) | 60 | 20 | 20 | 20 |
Телевизионный (ТВК) | 60 | 20 | 20 | 20 |
Телевизионный измерительный (ТИК) | 60 | 20 | 20 | 20 |
Табл. 2. Требования к минимальному количеству вопросов на экзаменах
Дополнительные требования к аттестации персонала, выполняющего автоматизированный контроль, и контроль с применением компьютерных средств обработки
Отличия этих требований от требований в случае контроля с применением ручных средств проявляются в части технологии контроля (специальные сканирующие устройства) и применения компьютерных средств обработки и сбора информации. К квалификации персонала, проводящего контроль с применением автоматизированных систем, предъявляются следующие требования:
Для получения права контроля по методикам автоматизированного контроля необходимо пройти аттестацию на предприятиях ОАО «Концерн Росэнергоатом» или у разработчика (поставщика) оборудования по работе с применением конкретных автоматизированных систем контроля с записью в квалификационном удостоверении.
Основные требования к проведению квалификационных экзаменов
Каждый кандидат при первичной аттестации сдает два экзамена по заявленному методу:
– теоретический экзамен, состоящий из двух частей: по физическим основам данного метода контроля (часть 1) и технологии и нормативно-технической документации НК (часть 2);
– практический экзамен, подтверждающий производственные навыки кандидата для контролера соответствующего уровня квалификации.
Требования к сборнику экзаменационных вопросов по теоретическому экзамену
Сборник экзаменационных вопросов должен быть разработан Аттестационным органом и утвержден его Руководством. Сборник должен содержать количество вопросов, указанное в табл. 2, и может быть представлен как в виде сброшюрованной книги, так и в компьютерной программе.
Требования к аппаратуре, стандартным, контрольным образцам и нормативной документации при проведении практического экзамена
Аппаратура для практического экзамена должна иметь паспорт, быть в рабочем состоянии и поверена, если это указано в паспорте на прибор.
Стандартные и контрольные образцы должны иметь паспорт.
Нормативная документация должна быть предоставлена в последнем издании (с изменениями).
Требования к комплекту экзаменационных образцов для практического экзамена
В комплект образцов для практического экзамена по НК должны входить образцы, соответствующие типам реальных объектов контроля (основной металл с заданным химическим составом или сварное соединение с соответствующей разделкой и технологией сварки), причем в них должны быть несплошности различного типа, возникающие как при производстве, так и в процессе эксплуатации. Комплект образцов для практического экзамена по НК должен содержать отдельные образцы без дефектов. Каждый экзаменационный образец должен иметь паспорт, содержащий сведения об образце и имеющихся в нем несплошностях, де-фектограмму, радиографический снимок и технологическую карту контроля и заключение в соответствии с категорией сварного соединения или основного металла, наплавки. Заключение на экзаменационный образец должно составляться по результатам контроля контролером с уровнем квалификации СПА.
Проведение теоретического экзамена
Теоретический экзамен сдается в письменной форме.
Для каждого уровня квалификации и метода НК должны быть разработаны Аттестационным органом сборники по теоретическим экзаменам, где каждый вопрос имеет многовариантные ответы.
Экзаменационные вопросы выбираются из сборника случайным образом.
Допускается сдача письменного теоретического экзамена на компьютере. После проведения экзамена проводится собеседование с аттестуемым.
В сборник вопросов по радиографическому методу должны входить вопросы по защите от излучения.
Теоретический экзамен при аттестации контролера уровня квалификации СПА включает вопросы на знание:
– технологии металлов и материаловедения, механизмов образования дефектов и их типов;
– методов контроля, на которые кандидат аттестуется в качестве члена аттестационной комиссии предприятия ОАО «Концерн Росэнергоатом».
Проведение практического экзамена
При проведении практического экзамена комиссия выдает кандидату протокол практического экзамена, который включает:
– для БПВЗ – технологическую карту контроля и бланк для фиксирования обнаруженных несплошностей;
– для СПВЗ и СПА – бланк, в котором кандидат должен разработать технологическую карту контроля.
Кандидат на СПВЗ и СПА проводит контроль не менее двух экзаменационных образцов: основного металла и сварного соединения с выдачей заключения по результатам контроля. Кандидат имеет право использовать на практическом экзамене необходимую нормативную документацию (ГОСТ, ОСТ, ПНАЭ Г, РД и т. п.). При аттестации по радиографическому методу кроме контроля образцов кандидат проводит расшифровку рентгеновских снимков: не менее пяти рентгенограмм и не менее трех на артефакты пленки.
Кандидат, претендующий на уровень квалификации СПА, должен сдать практический экзамен в объеме требований уровня квалификации СПВЗ. Кандидат может представить разработанный им документ (технологическую инструкцию, техническое решение, методический документ, экзаменационные билеты по какому-либо методу контроля, курс лекций по теоретическим вопросам или для дополнительной аттестации и т. п.).
Оценка результатов экзаменов и их оформление
Кандидат на уровни квалификации БПВЗ, СПВЗ и СПА считается выдержавшим экзамен, если он набрал в сумме по всему экзамену не менее 80 %, но не менее 70 % по каждой части экзамена.
Оценка ответов по теоретическому экзамену Nтеор, %, либо подсчитывается экзаменаторами, либо распечатывается в протоколах ответов при компьютерном варианте экзамена.
Итоговая оценка практического экзамена определяется путем сравнения полученных кандидатом результатов с паспортом на экзаменационный образец и подсчитывается в соответствии с методикой оценки практического экзамена, разработанной Аттестационным органом для данного метода контроля. В качестве примера представлена методика оценки практического экзамена по капиллярному контролю (табл. 3).
Содержание пунктов билета | Максимальная оценка, % | Оценка образца ¹ 1, % | Оценка образца ¹ 2, % |
1. Составление технологической карты контроля экзаменационного образца | всего 25, из них: | всего 25, из них: | всего 25, из них: |
1.1. Выбор способа контроля | 10 | 10 | 10 |
1.2. Выбор дефектоскопических материалов | 10 | 8 | 10 |
1.3. Выбор комплекта контрольных образцов для проверки чувствительности | 5 | 3 | 5 |
2. Определение чувствительности выбранного дефектоскопического набора | 10 | 6 | 10 |
3. Очистка контролируемой поверхности | 5 | 5 | 5 |
4. Проведение контроля | 15 | 13 | 15 |
5. Оформление дефектограммы | 10 | 9 | 10 |
6. Выявление не менее 80 % дефектов на экзаменационном образце от указанных на контрольной дефектограмме | 10 | 8 | 10 |
7. Оформление результатов контроля | 15 | 12 | 15 |
8. Окончательная очистка экзаменационного образца от дефектоскопических материалов | 5 | 5 | 5 |
9. Соблюдение Правил техники безопасности и охраны окружающей среды | 5 | 5 | 5 |
Итого: | 100 | N1 = 84 | N2 = 100 |
Итоговая оценка за практику: | N = (N + N )/пр 1 2 | 2 = (100 + 84)/ | 2 = 92 % |
Табл. 3. Методика оценки практического экзамена по капиллярному контролю
Итоговая оценка N экзаменов кандидата на уровни квалификации БПВЗ, СПВЗ и СПА рассчитывается по формуле:
N = 0,25N 1теор + 0,25N 2теор + 0,5N пр ;
где N 1теор - оценка по теоретическому экзамену (часть 1);
N 2теор - оценка по теоретическому экзамену (часть 2);
N - оценка по практическому экзамену.
Оформление квалификационного удостоверения в Аттестационном органе
Контролерам, прошедшим проверку теоретических знаний и практических навыков, должны выдаваться удостоверения за подписью председателя комиссии с печатью организации (предприятия), проводящей аттестацию.
Результаты проверки теоретических знаний и практических навыков контролеров указываются в Итоговом протоколе, при этом одновременно оформляется Протокол аттестационной комиссии с указанием решения о допуске к выполнению соответствующих работ.
Аттестация контролеров в ПДАК на предприятиях ОАО «Концерн Росэнергоатом»
В ПДАК предприятий ОАО «Концерн Росэнергоатом» может проходить периодическая, дополнительная и внеочередная аттестации контролеров (БПВЗ, СПВЗ).
ПДАК предприятия назначается приказом директора и включает штатных контролеров предприятия; она состоит из председателя, его заместителя и членов аттестационной комиссии. Члены ПДАК должны проходить периодическую аттестацию один раз в три года в Аттестационном органе.
Все виды аттестаций состоят из двух экзаменов – теоретического и практического. Для приема экзаменов в комиссии должно быть не менее двух контролеров по каждому методу контроля, аттестованных в качестве членов аттестационной комиссии, имеющих квалификационный уровень СПА. Программы должны быть разработаны Аттестационным органом или согласованы с ним, если они разработаны предприятием ОАО «Концерн Росэнергоатом».
После принятия положительного решения ПДАК по результатам экзаменов в квалификационное удостоверение аттестованного контролера, выданное Аттестационным органом, вносится результат аттестации, который подписывается председателем ПДАК и заверяется печатью предприятия ОАО «Концерн Росэнергоатом».
Ежегодная проверка практических навыков фиксируется в удостоверении с указанием номера протокола, даты и подписи председателя ПДАК. К удостоверению при любом виде аттестации прилагается Протокол аттестационной комиссии.
Для продления срока действия удостоверения контролеры проходят периодическую аттестацию по проверке теоретических знаний не реже одного раза в три года, а практических навыков – не реже одного раза в год.
Следует отметить, что в представленном документе [4] не полностью отражен ряд практически важных вопросов. В частности, отсутствуют требования к организационной структуре ПДАК и взаимодействию с надзорными органами, к оснащенности учебно-методическими материалами, обеспеченности паспортизированными экзаменационными образцами и т. д. Не приведены критерии оценки результатов практического экзамена на АЭС, особенно при использовании в качестве объекта контроля находящегося в эксплуатации участка оборудования или трубопровода.
Отсутствует механизм обеспечения объективности и достоверности результатов аттестации, в том числе из-за того, что на данном этапе нельзя признать деятельность ПДАК независимой от администрации АЭС.
Учитывая сказанное, можно рассматривать предложенный порядок аттестации контролеров на действующих АЭС как временный документ по разработке отраслевых правил аттестации персонала контроля в атомной энергетике.
В перспективе эти отраслевые правила аттестации должны базироваться на документе федерального уровня Ростехнадзора РФ СДАНК-02-2020 и отражать специфику отрасли в виде Приложения.
Литература
1. СДАНК-02-2020. Правила аттестации персонала в области неразрушающего контроля (утв. постановлением Госгортехнадзора России от 23.01.2002, ¹ 3; зарегистрировано в Минюсте РФ 17.04.2002, регистрационный ¹ 3378). – В кн.: Сб. документов. Сер. 28. Вып. 3. – М: ГУП «НТЦ «Промышленная безопасность», 2002.
2. Концепция управления Системой нераз-рушающего контроля и основные направления ее развития (утв. Госгортехнадзором России 28.08.1999 – В кн.: Сб. документов. Сер. 28. Вып. 1. – М: ГУП «НТЦ «Промышленная безопасность», 2000, с. 5–16.
3. ПНАЭ Г-7-010-89. Оборудование и трубопроводы атомных энергетических установок. Сварные соединения и наплавки. Правила контроля / Нормативный документ (действует с изменением ¹ 1 от 01.09.2000, постановление Госатомнадзора России от 27.12.1999 ¹ 7). – М.: НТЦ ЯРБ, 2000.
4. ПР 1.3.3.99.0010-2010. Порядок аттестации контролеров, выполняющих контроль металла на действующих АЭС. – М: ОАО «НПО ЦНИИТМАШ», 2010.
Ю.Н. КОЗИН, А.С. ПЕЧЕРКИН, О.В. ПОКРОВСКАЯ,
(НТЦ «Промышленная безопасность»)
Федеральный закон «О промышленной безопасности опасных производственных объектов» (от 21.07.97 № 116-ФЗ) определил основные элементы регулирования промышленной безопасности. Один из них - экспертиза промышленной безопасности технических устройств, применяемых на опасных производственных объектах. В соответствии с приказом Госгортехнадзора России от 12.08.99 № 152 она включает техническое диагностирование оборудования и проведение контроля оборудования и материалов неразрушающими методами. Таким образом, неразрушающий контроль (НК) - инструмент экспертизы промышленной безопасности, позволяющий определить состояние технических устройств, оценить срок их дальнейшей безопасной эксплуатации. Использование неразрушающего контроля при изготовлении, монтаже, строительстве, ремонте и эксплуатации технических устройств, зданий и сооружений позволяет предотвратить отказы в работе, аварии и разрушения, что особенно важно для опасных производственных объектов в условиях увеличенного износа основных фондов. Качество неразрушающего контроля зависит от ряда факторов:
состояния оборудования и приспособлений для неразрушающего контроля (исправность, соответствие установленным характеристикам);
уровня квалификации персонала, проводящего контроль;
полноты и качества методик неразрушающего контроля;
организации подготовки и проведения контроля различными методами в лабораториях неразрушающего контроля.
До настоящего времени отсутствовала единая организационная структура управления неразрушающим контролем в различных отраслях промышленности. Существуют организации разных форм собственности, занимающиеся подготовкой персонала, разработкой методических документов по неразрушающему контролю и другими вопросами неразрушающего контроля. Попытка комплексного решения последних была ++предпринята общественной организацией - Национальным аттестационным комитетом по неразрушающему контролю, который решил часть вопросов в области создания уровневой системы подготовки персонала для неразрушающего контроля. Проблемы, связанные с аттестацией средств неразрушающего контроля, методических документов по неразрушающему контролю, лабораторий неразрушающего контроля, существуют до сих пор. Решение их будет осуществляться в рамках Системы экспертизы промышленной безопасности (СЭПБ), созданной Госгортехнадзором России.
Участники СЭПБ: Госгортехнадзор России и его территориальные органы, Наблюдательный и Консультативный советы, отраслевые и функциональные комиссии, Координирующий орган (НТЦ «Промышленная безопасность») и его Территориальные уполномоченные органы, экспертные организации, Независимые органы по аттестации. СЭПБ постоянно расширяется, в настоящее время в нее вошла Система подготовки руководителей и специалистов организаций по промышленной безопасности и охране труда. Новым этапом развития СЭПБ явилось утверждение Госгортехнадзором России Концепции управления системой неразрушающего контроля и основных направлений ее развития, в соответствии с которой вопросы управления Системой НК решаются в рамках СЭПБ. Для этого в СЭПБ дополнительно создаются Управляющий совет и Совет экспертов по НК; Независимые органы по аттестации персонала НК, методических документов по НК, лабораторий и средств НК.
В соответствии с Концепцией основными направлениями развития Системы НК должны стать: разработка единых требований по каждому элементу данной системы, нормативов по аттестации в области НК (аттестация персонала, лабораторий, методических документов, средств по видам и методам НК), аккредитация, аттестация и проверка каждого из элементов Системы НК.
Источник - статья А. А. Майорова опубликованная в журнале « В мире НК » № 1(35). 2007.
Введение
В течение более 100 лет, прошедших после открытия рентгеновских лучей, их применение для неразрушающего контроля основывалось на использовании рентгеновской пленки и специальных пленочных систем (промышленная радиография) и позднее – на использовании рентгенооптических преобразователей (промышленная радиоскопия).
По сути, оба эти метода получения изображений являются аналоговыми, хотя в последнее время с развитием компьютерной техники в промышленной радиографии нашла применение техника оцифровки пленочных изображений с целью уменьшения затрат на содержание архивов, а в промышленной радиоскопии стали применять цифровые телевизионные камеры высокого разрешения. Хотя и ту, и другую технологии можно назвать цифровыми (используется компьютер и специальное программное обеспечение), они не будут являться предметом рассмотрения в настоящей статье. Применение оцифровщиков стало обыденным в практике дефектоскопистов (системы ВидеоРен, Унирен, Марс и др.)
Целью настоящей статьи является рассмотрение цифровых технологий, замещающих пленку с требуемым качеством изображения. Мотивацией замены обычно является уменьшение стоимости вследствие уменьшения времен экспозиции и уменьшения стоимости хранения, уменьшения требуемых рабочих площадей и исключения химии из процесса обработки. Такими технологиями являются:
• цифровая радиография (ЦР) с использованием цифровых детекторных систем ЦДС (плоскопанельных и линейных детекторов).
КР начала использоваться около 20 лет назад в медицине для замены пленки и обладает существенными преимуществами перед пленочной технологией:
• каждая пластина может использоваться несколько тысяч раз;
• время экспозиции по сравнению с пленкой в несколько раз меньше;
• изображение архивируется в цифровом виде.
Чтобы конкурировать с пленочными системами, в последние годы разработаны высококачественные КР системы, имеющие пространственное разрешение и отношение сигнал/шум, сравнимые при соответствующих дозах облучения с пленочными системами неразрушающего контроля.
Цифровая радиография также была использована в первую очередь для замены пленки в медицине. Разработанные для этой цели ЦДС оказали революционизирующее влияние на радиологическую технику. Эти детекторы позволили развить новые, основанные на компьютерных технологиях, приложения. Эти технологические и алгоритмические разработки оказались применимы также и для использования в НК. Имеются в виду новые технологии калибровки ЦДС, которые позволяют практически полностью избавиться от их собственных шумов. Такие возможности отсутствуют у пленочных систем и систем КР с ЗП. Поэтому ЦДС имеют самый низкий уровень шумов в радиографии и открывают путь к новым приложениям, где требуются чрезвычайно высокие чувствительность и контраст изображения в сочетании с возможностью контроля слабых изменений радиационной толщины.
Чрезвычайно важным являются также экономические преимущества ЦДС перед классической пленочной техникой. Гораздо более быстрый процесс обработки и интерпретации при высоком качестве изображения приводит к существенному выигрышу во времени по сравнению с пленкой и/или другими методами неразрушающего контроля. Целью настоящей статьи является обсуждение возможностей новых цифровых технологий, для чего будет проведено сравнение с возможностями пленочной радиографии. Сравнение начнем с классификации существующих детекторов рентгеновского излучения.
Детекторы рентгеновского излучения

На рис. 1 представлена схема, иллюстрирующая основные типы детекторов рентгеновского излучения, применяемых для получения изображения.
Рентгеновская пленка
Рентгеновская пленка до сих пор является наиболее широко используемым в промышленности детектором рентгеновского излучения в силу хорошо отработанной законодательной базы применения во всех отраслях промышленности, существующей инфраструктуры применения (фотолаборатории, оборудование, обученный персонал и т. п.). Однако объемы применения пленки с каждым годом уменьшаются в связи с развитием новых методов регистрации рентгеновских изображений, о которых речь пойдет дальше.
Запоминающие пластины
В компьютерной радиографии для получения изображения вместо пленки применяются специальные гибкие пластины многократного использования. Кассеты с такими пластинами имеют типовые для рентгеновской пленки размеры, например 18 х 24, 18 х 30, 24 х 30, 35 х 43 см, а также аналоги рулонных пленок. Возможна также резка пластин, т. е. считывание и других размеров. Для запоминания изображений в пластине использован слой с фотостимулируемой памятью – сложное химическое соединение. Чаще всего используются соединения типа BaFBrxI1-x:Eu2+.
Цифровые детекторы непрямого преобразования рентгеновского излучения
Начнем обсуждение с детекторов непрямого преобразования, как наиболее часто используемых на практике. Они отличаются тем, что рентгеновские кванты сначала взаимодействуют со сцинтиллятором с образованием фотонов света, а затем свет преобразуется или сразу в электрический сигнал, как в твердотельных плоскопанельных детекторах, или в поток электронов в рентгеновском электроннооптическом преобразователе (РЭОП), который создает видимое изображение на выходном люминофорном экране. В качестве плоскопанельных детекторов непрямого преобразования чаще всего используются панели на основе аморфного кремния (аSi). В них используются сцинтилляторы из CsI или Gadolinium Oxisulfide, которые преобразуют рентгеновское излучение в видимый свет. Этот свет затем конвертируется в заряд сенсорами из аморфного кремния (рис. 2). Чувствительность детектора со сцинтиллятором из Gadolinium Oxisulfide будет зависеть от толщины покрытия (рис. 2а). Однако при увеличении толщины покрытия из-за рассеяния света ухудшается пространственное разрешение детектора. В какой-то степени от этого недостатка свободны панели с покрытием из CsI (рис. 2 б).
CsI хорошо поглощает рентгеновское излучение, причем в области энергий рентгеновских фотонов, обычно используемых в промышленной дефектоскопии (40 – 300 кэВ), поглощение происходит в основном за счет фотоэффекта (вклад в поглощение за счет эффекта Комптона становится существенным при энергиях выше 300 кэВ). Слой CsI:Na генерирует при поглощении рентгеновского излучения голубой свет, который распространяется по направлению к фотодиодной матрице вдоль монокристаллических острий как по оптоволокну (т. е. без рассеяния).
Ранние эксперименты с аSi показали высокий уровень шума этих панелей. Прогресс в технологии вместе с программными возможностями, позволяющими усреднение по многим кадрам, позволил резко улучшить отношение сигнал/шум. Качество изображений, получаемое сейчас на этих панелях, превышает качество, получаемое на запоминающих пластинах, и приближается к качеству изображения на панелях аSe.
Более того, панели из аSi менее чувствительны к свойствам окружающей среды, что делает возможным их применение в полевых условиях и неконтролируемых приложениях. На рис. 3 в качестве примера показаны фотографии некоторых широко используемых в практике детекторов.
Цифровые детекторы прямого преобразования рентгеновского излучения
В детекторах прямого преобразования при воздействии рентгеновского кванта в толще полупроводника сразу генерируются электронно-дырочные пары. Под действием приложенного напряжения возникает электронный ток, который может быть усилен и с помощью считывающей электроники преобразован в изображение (рис. 4).

Наиболее распространенными вариантами ЦДС прямого преобразования являются панели на основе аморфного селена (aSe) и монокристаллического теллурида кадмия (CdTe). В первом случае сборка тонкопленочных транзисторов (TFT) покрывается аморфным селеном, что позволяет конвертировать рентгеновское излучение напрямую в цифровой сигнал без использования сцинтилляторов или фосфора. Вследствие отсутствия влияния рассеяния и оптимального отношения сигнал/шум качество изображения достигает качества, характерного для среднезернистой пленки. Ограничением селенового детектора является узкий диапазон рабочих температур. Как для работы, так и при хранении детектор нужно поддерживать в температурном диапазоне 5 – 30 °С для того, чтобы избежать разрушения селенового слоя. Также при высоких энергиях (> 180 кэВ) селен склонен к образованию фантомных изображений.
Все эти ограничения делают возможным применение aSe панелей в очень специфичных приложениях, где можно строго контролировать необходимые для этих панелей условия работы. Детекторная система прямого преобразования на основе CdTe свободна от ряда недостатков системы на основе aSe. Она может работать в гораздо более широком температурном диапазоне при энергиях рентгеновских квантов до 300 кэВ, обладая при этом в несколько раз большей чувствительностью. На рис. 5 показан один из типов детекторов прямого преобразования.
Технологии формирования и считывания сигналов в ЦДС
Механической основой любого плоскопанельного детектора является стеклянная подложка, на которую устанавливается считывающая электроника.
TFT-технология
TFT (thin film transistors)-технология используется в основном в панелях на базе аморфных кремния или селена. Панели детекторов непрямого преобразования являются типичными сборками фотодио- дов на активной TFT-матрице. Для детек- торов с прямым преобразованием, де- текторный слой располагается прямо на эту матрицу. Матрица TFT-транзисторов представляет собой достаточно простую структуру электронных переключателей (типовая схема для любого типа панелей показана на рис. 6).

Емкость каждого светодиода в исходном состоянии заряжена до напряжения U+. При облучении светом она разряжается: чем больше света, тем меньше остаточный заряд. При считывании TFT транзистор открывается, и емкость снова заряжается через считывающий усилитель до значения U+. Величина заряда измеряется усилителем считывания и в виде напряжения U подается на аналогоцифровой преобразователь.
Панели могут быть очень больших размеров (40 ?40 см). Они имеют не очень высокое разрешение (типичное значение ве- личины пикселя 127 мкм). Отличительной особенностью аморфного кремния является очень высокая радиационная устойчивость, что позволяет применять такие панели при высоких энергиях рентгеновских квантов. Поскольку процесс производства панелей на базе аморфного материала и TFT-технологии требует специфического оборудования и условий производства, такие панели достаточно дороги.
CCD-технология
ССD (coupled charge device)-технология является одной из ведущих для получения высококачественных рентгеновских изображений. В отличие от матричных панелей типа TFT или CMOS, в ССD панелях считывание сигнала происходит путем транспортировки зарядовых пакетов вдоль кремниевой подложки. Преимуществом таких панелей является низкий шум, высокая чувствительность. Обычно в ССD панелях используют оптоволоконные буферные вставки, позволяющие увеличить площадь приемного окна панели и служащие одновременно защитой от радиации. Но даже с таким дополнительным экранированием ССD панели могут работать только при энергиях рентгеновских квантов < 50 кэВ. Как и в случае с аморфным кремнием, их производство требует специальных условий, поэтому они достаточно дороги.
CMOS-технология
CMOS (complementary metal oxide semiconductor) – эта технология, как и TFT с аморфным кремнием, является матричной сборкой. Основным преимуществом этой технологии перед остальными является использование хорошо развитой промышленной базы производства интегральных схем. Уровень шумов CMOS-панелей приблизился к уровню ССD-панелей, динамический диапазон в несколько раз выше. На CMOS-панелях получено самое высокое пространственное разрешение (размер пикселя несколько микрометров). Стоимость таких панелей хотя еще достаточно высока, тем не менее динамично снижается и скоро, на наш взгляд, станет меньше стоимости РЭОП со сравнимыми характеристиками.
Калибровка Цифровых Детекторных систем
Калибровка плоскопанельного детектора (наряду с коррекцией «плохих» пикселей) является одной из важнейших операций, обеспечивающих, как мы увидим в дальнейшем, получение отношения сигнал/шум и контрастной чувствительности, существенно превышающих эти значения для других типов детекторов (рентгеновской пленки и запоминающих пластин). Вполне естественные вариации характеристик сенсоров в панели, неоднородности распределения рентгеновского излучении, также как особенности электроники, будут вызывать некоторые различия сигналов от различных пикселей панели. С помощью калибровки можно полностью скорректировать изображения. Обычно калибровка включает захват изображений при полной (светлопольное изображение), средней (среднепольное изображение) и нулевой (темнопольное изображение) дозовых нагрузках. Темнопольное изображение используется для получения, базового, «темнового» сигнала от детектора, который определяется токами фотодиодов, токами утечки тонкопленочных транзисторов и разницей между различными зарядовыми усилителями, используемыми в считывающей электронике. Светлопольное и среднепольное изображения используются для расчета усиления, или отклика, каждого пикселя, и соответствующего считывающего усилителя. Одним из источников шума в детекторе является коррелированный линейный шум, который является шумом, присущим одновременно всем пикселям данной строки. Современные программные средства позволяют провести процедуру коррекции этого шума, которая должна приводить к минимизации вариаций вследствие этого шума. Для этого доля сенсоров панели маскируется от сцинтилляционного экрана, и, таким образом, не получает светового сигнала во время рентгеновской экспозиции. Сигнал от этой части панели соотносится с темнопольным изображением, для определения коррекции, которая должна быть внесена в каждую строку. Результирующие калибровочные изображения используются для нормализации отклика пикселей.
Коррекция «плохих» пикселей
Основными типами «плохих» пикселей можно назвать следующие три:
- Не усиливающий пиксель, или «мертвый» пиксель. Сигнал от него не зависит от дозы облучения.
- Сверхчувствительный пиксель. Значение уровня серого для него болеечем в 1,3 раза превышает среднее по площадке из 21х21 пикселей.
- Малочувствительный пиксель. Значение уровня серого для него менее чем в 0,6 раза меньше среднего по площадке из 21х21 пикселей.
Для того, чтобы скорректировать «плохие» пиксели, выявляющиеся в виде плохих строк, используется алгоритм коррекции плохих пикселей. Этот алгоритм усредняет сигналы от соседних пикселей, используя это среднее значение для плохих пикселей. Каждый пиксель имеет 8 ближайших соседних пикселей (за исключением тех, которые находятся на краю сенсорной панели). Если по крайней мере 3 из них считаются хорошими, тогда возможна операция усреднения их для получения значения плохого пикселя. В противном случае плохой пиксель не может быть скорректирован правильно. В качестве примера на рис. 7 приведены два изображения, полученные с помощью плоскопанельного детектора FlashScan 33 (данные компании Юнитест). Слева (рис. 7, а) радиографическое изображение сварного шва (сталь 10 мм, 100 кВ) с характерными непроварами и «плохими» пикселями, проявленными в виде «плохих» строк. Справа (рис. 7,б) то же изображение после интерполяционной корректировки.

Сравнение качества изображения различных детекторных систем
Весьма важным при контроле изделий, работающих в зонах повышенного риска, например в аэрокосмической и атомной промышленности, является оценка верхнего предела качества изображения, получаемого с помощью новых цифровых технологий. Как уже отмечалось, для ЦДС (плоскопанельных детекторов и линейных детекторов) разработаны методики калибровки и вычитания собственных шумов, позволяющие получить максимально достижимые отношения сигнал/шум для этих приборов. Такая процедура улучшает контрастную чувствительность настолько, что позволяет контролировать изменение 1/1000 радиационной толщины контролируемого материала. В то же время мы знаем, что стандартная пленочная радиография с использованием пленочных систем (со свинцовым экраном или без него) позволяет достичь контраста 1/100 даже с использованием пленочных систем высшего класса (класс «С1» по обще европейскому стандарту EN 584-1 или «специальный» по ASTM E 1815). Компьютерная радиография с использованием фосфорных запоминающих пластин является реальной заменой пленочных технологий даже без дополнительного компьютерного улучшения изображения. Сравнение основано на изучении измеренных значений отношения сигнал шум, пространственного разрешения и сравнения радиографических изображений, как с использованием собственных экспериментальных данных, так и с привлечением данных из других источников.
Основные параметры качества изображения
Радиографическое изображение в соответствии с терминологией описывается следующими главными параметрами качества изображения:
- Базовое пространственное разрешение SRb, измеренное с помощью эталона с двойной проволокой согласно стандарту EN 462-5 и равное половине зарегистрированной не резкости изображения или эффективному размеру пикселя. Иногда пользуются понятием Разрешающая способность, которая определяется из зависимости контраста соседних объектов от расстояния их разделяющего. Эта зависимость называется модуляционной передаточной функцией (MTF) или контрастной передаточной функцией. Величина обратная расстоянию, разделяющему соседние объекты, называется Пространственной частотой и измеряется, по аналогии с пленкой, в парах линий/мм.
- Нерезкость изображения определяется геометрической нерезкостью, деленной на увеличение (проекционная нерезкость) и нерезкостью детектора описываемой базовым пространственным разрешением SRb (равным половине нерезкости детектора).
- Отношение сигнал/шум SNR. Детектор характеризуется нормированным отношением сигнал/шум SNRnorm как функции условий экспозиции (экспозиционной дозы и радиационного качества). Нормировка измеренного отношения сигнал/шум на базовое пространственное разрешение необходима, поскольку измеренное значение отношения сигнал/шум увеличивается как квадратный корень от площади детектирующих пикселей (результат статистики Пуассона для рентгеновских фотонов).
- Отношение контраст/шум CNR. В общем случае CNR зависит от отношения сигнал/шум детектора и эффективного коэффициента поглощения материала.
- Чувствительность детектирования (контрастная чувствительность Сs = 1/CNR, где CNR есть отношение контраст/шум) небольшого изменения радиационной толщины объекта Δw (происшедшей из-за наличия дефекта внутри объекта) определяется отношением контраста (изменения интенсивности сигнала ΔI) к уровню шума изображения (стандартное отклонение от I). CNR для данного Δw может быть рассчитано из SNR (отношения сигнал/шум) изображения с учетом коэффициента поглощения μ и коэффициента рассеяния k (равного отношению интенсивностей рассеянного и первичного излучения).
- Динамический диапазон (диапазон радиационных толщин объекта, доступных анализу на одном и том же изображении). Поскольку для пленок эта величина фиксирована (ограничена диапазоном оптических плотностей 2 – 4.5 и μэфф), то она не считается параметром для пленочной радиографии, учитываемым в стандартах. В то же время большой динамический диапазон ЦДС в ряде практических приложений может иметь решающее значение при выборе детектора.
В работе проведен комплекс измерений по определению качества радиографических изображений, получаемых с помощью пленочных NDT систем, систем компьютерной радиографии и цифровых детекторных систем. Для демонстрации получаемого с разными детекторами качества изображения использовался один и тот же стандартный образец. Это была 8 мм стальная пластина со сварным швом с 2 мм усилением, содержащим все типовые дефекты.
Качество изображения, достижимое с помощью пленочных систем.
Показано, что SNRnorm зависит от класса пленочной системы, но имеет предельное значение (см. таблицу 1).

Минимальное значение 43 (класс С6 при D-D =2, рассчитанная доза 2 мГр), а максимальное 250 (лучший класс С1, D-D0=4,5, рассчитанная доза 60 мГр). Более высокие значения SNRnorm не достижимы для пленочных систем согласно стандарту EN584-1, потому что увеличение дозы ведет к увеличению оптической плотности почернения D>5, а такие изображения практически являются нечитаемыми. Базовое пространственное разрешение пленочной системы определяется качеством излучения (220 кВ, 8 мм фильтр медь), потому что это определяет толщину используемых свинцовых экранов (см. стандарт EN 444) и разброс электронов, генерируемых свинцовыми экранами для экспозиции пленки. Таблица 2 в стандарте EN ISO 14096-2 приводит значения, подобные SRb для корректной оцифровки пленки при переводе изображения на пленке в цифровую форму.
Качество изображения, достижимое с помощью систем компьютерной радиографии
Качество изображения, получаемое с помощью КР систем, классифицируется в соответствии с классами для пленочных NDT систем (таблица 1). Предельные значения SNRnorm соответствуют предельным значениям для подобных пленочных систем. Дополнительно к параметрам, характеризующим пленку, вводится базовое пространственное азрешение КР системы (SRb, мкм, в соответствии со стандартом 14874-1). Этот параметр определяет ограниченное пространственное разрешение КР систем по сравнению с пленкой.
Главным достижением в применении КР в неразрушающем контроле для замены пленки при контроле литья и сварки стало появление в последние годы сканера HD CR 35 (Duerr)*. Требования к КР системам в неразрушающем контроле определены стандартами EN 14784-1 и EN 14784-2. Таблица 4 стандарта определяет минимальное пространственное разрешение в зависимости от класса контроля, энергии облучения и толщины объекта контроля. В то время как большая часть содержания стандарта EN 14784-2 подобна EN 444 (основные принципы радиографического контроля в NDT), Таблица 4 в EN 14784-2 является нововведением и ограничивает значения пространственного разрешения используемых КР систем.
Существует еще одно ограничение на качество изображения систем КР. С увеличением экспозиционной дозы максимально достижимое значение SNRnorm ограничено. Это вызвано наличием структурного шума используемой запоминающей пластины. Дополнительные шумы в виде дополнительных пульсаций может вносить также сканер. Структурный шум запоминающей пластины связан с неоднородностями фосфорного слоя, связанными с процессом производства. Этот эффект известен также и для флуоресцентных экранов. При высоких экспозиционных дозах вклад квантового шума рентгеновского излучения невелик по сравнению с этими структурными шумами, отсюда качество изображения приходит к ограничению.

Пример достижимого качества изображения при контроле сварных соединений приведен на рис.9. Времена экспозиции достаточно высоки, поэтому шум на изображениях определяется структурным шумом самих КР систем. Очевидно, что стандартная КР система имеет худшее качество изображения (как значения SRb, так и SNRnorm) по сравнению с лучшей пленочной NDT системой, в то время как на HD-CR системе можно получить немного лучший результат, чем на пленочной системе. Согласно EN 14784-2 система HD-CR достигает класса В. Стандартная система не достигает класса А в этом примере.
Качество изображения, достижимое с помощью цифровых детекторных систем
ЦДСизображения были получены помощью плоскопанельного детектор XRD 1620 компании Perkin Elmer.Использовались две геометрии просвечивания:1. Тестовый образец находился непосредственно перед детектором (увеличение = 1) и 2. Тестовый образец находился межддетектором и рентгеновской трубко (увеличение = 3,5). Последняя геометрия требует применения мини фокусной трубки, чтобы геометрическая нерезкость на детекторе не превышала 200 мкм. На рис. 10 для сравнения представлены изображения одного и того же участка сварного шва на тестовом образце, полученные на пленке и с применением ЦДС.
Из чисто визуального сравнения двух изображений следует, что качество изображения, полученного с помощью плоской панели, выше при гораздо меньших дозовых нагрузках. Для более детального исследования было проведено сравнение изображений (рис. 11) одного и того же участка тестового образца (область шириной 12 мм с выявленными трещинами), приведенных к одному размеру (увеличение левого, пленочного изображения регулировалось с помощью оцифровщика, среднее изображение получено на плоской панели с геометрическим увеличением =1, правое – на плоской панели с увеличением 3,5).

Значительное увеличение SNRnorm в ЦДС технологии позволяет даже при увеличении 1 и базовом пространственном разрешении 200мкм детектировать микротрещины, которые на пленке (с гораздо лучшим SRb порядка 50 мкм) находятся на уровне шумов При увеличении 3,5 (рис. 11, правое изображение, предполагаемое SRb=70 мкм) можно различить гораздо больше деталей по сравнению с пленкой. Это улучшение качества изображения основано на увеличении SNRnorm по сравнению с пленочной технологией. Улучшенное SNR для ЦДС позволяет детектировать элементы с размерами, гораздо меньшими размера пикселя! На рис. 12 показаны два изображения одного и того же участка, полученные на пленке и плоской панели. Слева на пределе различима проволока W16. Справа мы видим проволоку W19 (50 мкм) при размере пикселя 200 мкм! Этот эффект называется субпиксельным разрешением. Недостаточное SRb компенсируется высоким SNR!
Как уже упоминалось, максимально достижимое значение SNRnorm для пленочной системы наивысшего класса ограничено максимальным рабочим диапазоном негатоскопов и оцифровщиков, с максимальным значением плотности почернения D=4,7. Это также ограничивает максимально возможную дозу облучения. Более высокие значения SNRnorm (больше 250) потребуют больших экспозиционных доз. Но пленки в принципе не читаемы при плотностях D>5. В случае КР систем, качество изображения ограничено их структурным шумом. Максимальное значение SNRnorm для современных КР систем пока не может быть выше 300. Эти ограничения SNRnorm для пленочных и КР систем преодолеваются для ЦДС следующим образом: перед насыщением ЦДС изображение может быть считано, ЦДС обнулен и может быть начат новый цикл экспозиции. Все изображения, полученные в таких циклах, могут усредняться в компьютере с получением окончательного усредненного изображения. Таким образом, время экспозиции может увеличиваться без какого-либо предела.
SNRnorm будет увеличиваться как квадратный корень из числа усредненных изображений, и/или квадратный корень дозы. Время экспозиции такого цикла может продолжаться без какого либо технического предела. SNRnorm будет линейно увеличиваться в зависимости от квадратного корня от дозы (эквивалентно времени экспозиции или количеству усредненных изображений). В [4] проведен детальный расчет SNRnorm при различных условиях просвечивания для детектора DIC100TL компании Ajat. Получены значения SNRnorm до нескольких тысяч.
Однако такие высокие значения SNRnorm обычно не достигаются в радиографической практике. Существуют практические ограничения: отклонения в чувствительности отдельных пикселей ЦДС ограничивают достижимое значение SNR на изображении. Не может быть достигнуто какого-либо дальнейшего улучшения SNRnorm, если пуассоновский шум рентгеновских квантов уменьшили в результате многократного усреднения до уровня ниже разницы между соседними пикселями. SNRnorm ограничено структурным шумом детектора. Здесь та же самая причина, что и в КР.
Однако ЦДС имеет существенное преимущество перед КР, о котором мы уже говорили в разделе «калибровка»: пиксели цифровой детекторной системы расположены в матрице, их положение фиксировано в процессе экспозиции и считывания. Поэтому небольшие отличия между пикселями (в чувствительности или в условиях вывода сигнала) приемлемы и могут быть точно измерены. Поскольку эти изменения стабильны во времени, возможна компенсация разницы между различными пикселями с помощью соответствующего программного обеспечения в процессе калибровки.
Такая калибровка ЦДС является ключом к улучшению контрастной чувствительности и высокому отношению сигнал/шум вследствие уменьшения структурного шума ЦДС. По сравнению со «стандартной калибровкой», предусматривающей однократную компенсацию в условиях вывода сигнала и усиления изображения можно произвести многократную корректировку усиления, приводящую к гораздо большему увеличению SNRnorm за счет компенсации различий между отдельными пикселями. Таким образом, для ЦДС с помощью хорошей калибровки можно преодолеть ограничения на величину SNRnorm, имеющиеся для пленочной и КР технологий.
Преимущество калибровки состоит не только в увеличении SNR, но и в уменьшении времени экспозиции. Требуемое качество изображения определяет необходимое время накопления. По сравнению с однократной калибровкой адаптивная многократная калибровка позволяет получить изображение с тем же самым отношением сигнал/шум за гораздо меньшее время накопления. Авторы исследовали достижимые значения SNRnorm при различных видах калибровки для детектора Hamamatsu, С7942, (экспозиция при 120 кВ, 7 мА, 30 мм Al). Показано, что если задача требует, чтобы SNR было 500, то этого можно достичь за 250 сек. при однократной калибровке и только за 15 сек. при многократной.
Показано также, что в отличие от расчетных, реальные значения SNRnorm ограничены. Все кривые достигают насыщения. Причина этого или в наличии структурного шума детектора уже после калибровки, или вследствие неоднородности материала самого объекта контроля. По той же причине наступает ограничение минимального детектируемого значения изменения толщины материала в % от толщины объекта. Эта контрастная чувствительность ограничена значением 0,1%, что соответствует SNRnorm примерно 1000. Увеличение времени экспозиции от 60 до 600 сек. изменяет ситуацию очень незначительно. Таким образом, Цифровые Детекторные Системы позволяют проводить неразрушающий контроль с гораздо лучшей контрастной чувствительностью, чем прописано в стандартах по радиографии. Это подтверждается и нашими экспериментами с плоскопанельным детектором FlashScan 33 производства компании Thales. Рис. 13 показывает зависимости чувствительности контроля, определенной с помощью ступенчатого эталона на образцах нержавеющей стали различной толщины.
Выводы
Детально рассмотрены новые цифровые технологии в неразрушающем контроле – компьютерная радиография с использованием многоразовых запоминающих пластин и цифровая радиография на базе плоскопанельных цифровых детекторных систем. Проведено сравнение этих технологий с традиционной пленочной технологией. Обсуждены важнейшие параметры, характеризующие качество и информативность изображения при использовании различных технологий. Показано, что с помощью систем компьютерной радиографии можно получать качество изображения, несколько лучшее по сравнению с пленочными системами и подтверждено, что эта технология в большинстве практических случаев позволяет полностью заменить пленку. Показано, что применение цифровых детекторных систем (плоскопанельных и линейных детекторов), позволяет получить существенно более высокое качество изображения, чем в пленочных и КР системах, что стало возможным в результате операций калибровки детекторов. Показано, что в результате использование цифровых детекторных систем позволяет снизить предел обнаружения изменения толщины материала до 0,1%. Показано, что вследствие высокого отношения сигнал шум, присущего цифровым детекторам, возможна индикация дефектов, существенно меньших по размеру, чем пиксель.
Отмечая новые, прорывные возможности цифровых детекторов, хочу упомянуть и о некоторых ограничениях, присущих этой технике. Она требует очень аккуратного обращения, критична к условиям окружающей среды, поэтому используется пока в полулабораторных условиях (специализированные радиографические комплексы, компьютерная радиография). Кроме того, будущее цифровой радиографии в значительной степени будет зависеть от того, как на технологическом уровне будут решаться проблемы с «плохими» пикселями и надежностью этой техники в целом.
Источник - статья А. А. Майорова опубликованная в журнале « В мире НК » № 1(35). 2007.
Другие статьи на тему цифровой радиографии можно посмотреть в разделе Статьи.
Источник - статья А. А. Майорова опубликованная в журнале «В мире НК» № 3(25). 2004.
Другие статьи на тему цифровой радиографии можно посмотреть в разделе Статьи.
Метод компьютерной радиографии основан на использовании способности некоторых люминофоров накапливать скрытое изображение, которое формиру¬ется в кристаллах, когда электроны, об¬разующиеся в них в результате облучения рентгеновским или гамма-излучением, захватываются на энергетические уров¬ни и остаются на них в течение длительно¬го времени. Из этого состояния они могут быть выведены возбуждением лазерным пучком (упрощенная зонная диаграмма процесса приведена на рис. 1)
Рис. 1. Образование скрытого изображения на флуоресцентной запоминающей пластине под действием рентгеновского или гамма-излучения (концентрация электронов на уровнях пропор¬циональна интенсивности излучения)
Посколь¬ку считывание информации, записанной на флуоресцентную запоминающую пла¬стину, возможно лишь с использованием современной компьютерной техники, этот вид записи получил название компьютер¬ной, или цифровой радиографии.
История вопроса
Свойства люминесцентных запоминающих составов известны уже давно, однако, первый коммерческий сканер (основной элемент системы компьютерной радиографии) был разработан и выпущен компанией Fuji в 1983 г. С тех пор различными фирмами (AGFA, Kodak и др.) было выпущено несколько моделей сканеров. Важный шаг был сделан в 1998 - 2000 гг., когда фирмами Orex и ICR были выпущены настольные варианты систем для компьютерной радиографии.
Куда записываем информацию?
В компьютерной радиографии для получения изображения вместо пленки применяется специальная пластина многократного пользования. Кассеты с такими пластинами имеют типовые для рентгеновской пленки размеры 18x24, 18x30, 24x30 и 35x43 см. Возможна также резка пластин, т. е. считывание и других размеров. Как уже указывалось, для запоминания изображений в пластине использован слой с фотостимулируемой памятью - сложное химическое соединение.
Как записываем информацию?
Под действием рентгеновского или гамма-излучения электроны внутри «флуоресцентных» кристаллов возбуждаются и переходят в квазистабильное состояние. Специальный считыватель сканирует экспонированную пластину лазерным пучком (рис. 2).
Рис. 2. Схема процесса сканирования запо¬минающей пластины и получения цифрового изображения: / -лазер; 2-оптика формиро¬вания пучка; 3 - зеркало; 4 - фотоумножитель; 5 - фильтр; 6 - оптика сбора света люминесцен¬ции; 7 - запоминающая пластина
При этом электроны высвобождаются из ловушки, что сопровождается эмиссией видимого света, длина волны которого отличается от длины волны излучения сканирующего лазера. Этот свет собирается фотоприемником и конвертируется в цифровой сигнал, преобразуемый в цифровое изображение.
Принцип действия цифровой радиографии
- Кассета с запоминающей пластиной экспонируется аналогично пленке, т.е. располагается за объектом. Пластина гибкая и может экспонироваться и без кассеты, если в этом есть необходимость. Загрузка и выгрузка пластины из кассеты (при использовании ручной загрузки) производится на свету, т. е. специальной темной комнаты не требуется. Поскольку чувствительность пластины существенно выше, чем у пленки, время экспозиции пластины в 5 - 10 раз меньше, что существенно уменьшает дозовую нагрузку на персонал.
- После экспонирования пластина загружается в сканер. При использовании сканеров с ручной загрузкой пластина вынимается из кассеты (если она экспонировалась в кассете) и помещается в сканер. В случае использования сканера с автоматической загрузкой пластина загружается в сканер только в кассете.
- Производится считывание изображения (время считывания, несколько десятков секунд, зависит от установленного пространственного разрешения).
- Считанное сканером изображение архивируется, обрабатывается, в том числе с использованием программ поиска дефектов, делается заключение и производится распечатка протокола контроля.
- После считывания информация стирается с пластины, и пластина вновь готова к работе.
Какое получаем изображение?
Все параметры прибора оптимизированы таким образом, чтобы получить изображение, эквивалентное получаемому на пленке соответствующего типа. Однако в отличие от пленки это изображение может быть улучшено, отмасштабировано, архивировано, растиражировано и за несколько секунд направлено по электронной почте в любое место без потери качества.
Сколько это стоит?
Хотя предлагаемое оборудование пока еще является не дешевым, оценку его окупаемости надо производить, учитывая, что при его использовании отпадает необходимость в рентгеновской пленке, оборудовании для проявки, сушки, помещениях, персонале и т. д.
Стандартизация Российских стандартов по компьютерной радиографии пока не существует. Однако существуют европейские и американские стандарты, ре гламентирующие деятельность в области компьютерной радиографии:
- СЕМ 138 N 540 94: Промышленная компьютерная радиография с фосфорными запоминающими пластинами. Часть 1: Классификация систем;
- СЕN 138 N 541 95: Часть 2: Общие принципы контроля металлических материалов с использованием рентгеновского и гамма-излучения;
- А5ТМ Е2007: Стандарт по компьютер ной радиологии (метод фотостимулированной люминесценции);
- А5ТМ Е2033: Стандарт по практическому использованию компьютерной радиологии (метод фотостимулированной люминесценции).
Преимущества цифровой радиографии:
- быстрота получения информации;
- исключается «мокрая» технология обработки пленки;
- дозы облучения существенно меньше необходимых для экспонирования обычной пленки (при сравнительно низких энергиях для получения изображения одинакового качества, например в случае пленки АСРА 07, напряжение
на трубке можно уменьшить на 30 %, а время экспозиции - в 10 раз; - благодаря более широкому, чем у пленки динамическому диапазону появляется возможность исследовать и контролировать детали более сложной формы с большей толщиной;
- пластина для записи является многоразовой, допускается экспонирование до 30 тыс. раз;
- имеется возможность архивирования информации в компьютере на различных носителях, делать необходимое количество идентичных копий, использовать электронную почту для передачи информации; время хранения лазерного диска без потери информации составляет не менее 30 лет;
- прямое получение цифровых изображений позволяет отказаться от оборудования для оцифровки рентгеновских пленок;
- уже сейчас достижимое пространственное разрешение при считывании составляет 10 пар линий/мм, что позволяет получать изображения чрезвычайно высокого качества.
Недостатки цифровой радиографии:
- радиографическое качество применяемых сейчас запоминающих пластин примерно соответствует крупнозернистой высокочувствительной пленке 07, что ограничивает сферу применения обсуждаемой техники; однако недостаток этот следует считать временным, поскольку уже разработаны [3] и скоро начнут выпускаться пластины, соответствующие по радиографическому качеству пленкам 04/05.
- чувствительность контроля, полученная при испытаниях систем компьютерной радиографии в различных лабораториях составляет 1,6 % и имеет тенденцию к некоторому ухудшению при более высоких энергиях; выпуск нового поколения запоминающих пластин, адаптированных к задачам промышленного НК (сейчас используются пластины, применяемые в медицине) решает и эту проблему;
- при увеличении энергии рентгенов ского излучения имеется тенденция к увеличению времени экспозиции (хотяоно все равно существенно меньше необходимого для экспозиции пленки).
Вывод
Среди средств НК появилась новая, мощная, быстро развивающаяся технология. Это свершившийся факт, существование которого игнорировать уже невозможно. От того, насколько быстро и правильно мы сумеем адаптироваться к нему, зависит будущее промышленного рентгеновского неразрушающего контроля и наше в нем будущее.
Источник - статья N. Parspour опубликованная в журнале « В мире НК » № 4(10) 2010г.
В статье описаны цифровые рентгеновские детекторы, применяемые для автоматического выявления дефектов в отливках.
Программа автоматического распознавания дефектов, рассматривая их как объемные, разделяет дефекты плотностного контраста как разницу значений уровня серого и геометрическую величину дефекта как площадь поверхности. С обычными усилителями изображения могут обнаруживаться дефекты плотностного контраста до 6%, с цифровыми детекторами изображения – до 3% толщины просвечиваемого материала. Такие возможности цифровых детекторов – следствие применения технологии амфорного кремния, которая обеспечивает прямое цифровое изображение. Таким образом может быть получен и использован сигнал с разрешением по величине 14 бит на точку вместо 8 бит для обычного усилителя изображения с ССD камерой. Поэтому цифровой детектор изображения позволяет регистрировать и анализировать участки с сильно меняющейся толщиной всего при одной позиции контроля.
Устройство автоматической системы контроля
Подлежащие контролю детали поступают по транспортеру в кабину с радиационной защитой, где находится манипулятор с четырьмя степенями свободы, на котором закреплены рентгеновский излучатель и цифровой детектор.Манипулятор устанавливается в позицию контроля после чего на детектор, в течении так называемого времени ввода картинки проецируется теневое рентгеновское изображение. Это время зависит от требуемого соотношения сигнал/шум и составляет для современных детекторов от 150 до 600 мсек.
После ввода картинки манипулятор перемещается в следующую позицию. Введенное изображение обрабатывается компьютером по алгоритму автоматической обработки изображения.
Требования к автоматическим системам контроля.
Современная промышленность ищет компромисс между постоянно ужесточающимися требованиями стандартов безопасности и требованиями заказчиков к снижению материальных и временных затрат. Применение цифровых детекторов дает реальный шанс удовлетворить эти противоречивые требования.
Время контроля системы определяется главным образом временем, необходимым для перемещения отливки внутри кабины от одной позиции контроля к другой и временем ее просвечивания.
Упрощенно время контроля можно представить следующей формулой:
Tr = Nпоз (Tпер + Tдан + Tввод) где Nпоз – число позиций контроля для детали, Tпер – время механического перемещения между отдельными позициями контроля, Tдан – время передачи данных, Tввод – время ввода картинки.
Видно что общее время контроля определяется главным образом, числом необходимых позиций контроля которое в свою очередь зависит от трех факторов: геометрической сложности отливки, выбора приемника и заданных заказчиком требований контроля. Чем сложнее деталь и жестче требования контроля, тем больше число необходимых позиций контроля.
Зависимости числа позиций контроля от выбора детектора определяется двумя параметрами: размером детектора и способа преобразования плотности потока прошедшего через деталь рентгеновского излучения в изображение. Уже несколько лет кроме существующих усилителей изображения используются так называемые ASD детекторы, которые непосредственно формируют цифровое изображение и поэтому известны как цифровые детекторы. Эти детекторы обладают расширенным диапазоном уровня серого и поэтому позволяют контролировать детали с очень большой разницей толщины стенок, в то время как обычным усилителям изображения необходима одна или более дополнительных позиций контроля, для того, чтобы участки с разной толщиной стенки просветить с разных направлений.
Цифровые детекторы


Устройство и принцип действия цифрового детектора показаны на рис. 2.
Рентгеновское излучение попадает сначала на слой сцинтиллятора (например Csl), в котором оно преобразуется в световые фотоны. За слоем расположена светодиодная матрица, по своей спектральной чувствительности соответствующая сцинтиллятору. Светодиоды состоят из амфорного кремния, который дал имя ASD (Amorphus Silicon Detector = детектор из амфорного кремния). Фотоны наводят в элементах матрицы электрический заряд. Считывание заряда производится бипараллельным управлением всех элементов внутри каждой ячейки.
Специальная малошумящая микросхема преобразует заряд в электрический сигнал, который после усиления поступает на внутренний аналого-цифровой преобразователь и оцифровывается. Прямое преобразование рентгеновского изображения в цифровую картинку (минуя трубку ускорителя и камеру, как в обычном усилителе изображения) определяет высокие характеристики цифровых детекторов.
Тогда кА визуальное разрешение обычных усилителей изображения в настоящее время больше, чем у имеющихся на рынке цифровых детекторов, последние имеют значительно лучшее плотностное разрешение.
При применении цифровых детекторов достигается диапазон сигнала 16 бит на точку теоретически и 14 бит на точку практически. То есть в одной позиции может различаться 214 значений серого. Обычные усилители изображения с CCD камерой различают 28 значений серого. Для сравнения можно упомянуть, что глаз человека может различать 26 значений серого.
У обычных усилителей изображения имеется, однако, возможность повышения числа различаемых значений серого до 14 бит при применении цифровой камеры, камеры, однако, необходимо принимать во внимание некоторые отрицательные последствия, такие как худшее отношение сигнал/шум, большую подверженность засветке и меньшую компактность.
В таблице 1 приводится сравнение плоских цифровых детекторов и обычных усилителей изображения
Таблица 1
Характеристики | Плоский цифровой детектор | Обычный усилитель изображения |
Поглощение рентгеновского излучения | Очень хорошее | Хорошее |
Компактность | Высокая | Низкая |
Засветка | Очень малая | Большая |
Искажение картинки | Нет | Искажение в краевых областях |
Коэффициент преобразования | Очень хорошая | Хорошая |
Динамический диапазон серого | Широкий | Средний |
Отношение сигнал/шум | От хорошего до очень хорошего | Среднее |
Контраст | Высокий | Низкий |
Для решения задач современного литейного производства, требующих в основном быстрого массового контроля отливок и выявления дефектов в миллиметровом диапазоне, отлично подходят имеющиеся на рынке цифровые детекторы средней стоимости.
В таблице 2 представлены параметры детекторов фирм Varian и Perkin-Elmer – лидеров рынка в области цифровых детекторов.
Величина, приведенная в таблице как плотностное разрешение, характеризует разрешение детектора по толщине материала. Эта величина определяется в конечном итоге для данного детектора динамическим диапазоном серого цвета (числом значений серого).
Визуальное разрешение определялось экспериментально.
Таблица 2
Тип | Фирма | Формат | Визуальное разрешение мм |
Плотностное разрешение, % толщины |
Условная цена |
Применял YXLON |
УИ9'' | Thomson + CCD камера 758 строк | 9'' 5'' |
0,32 0,17 |
6 | 1 | х |
УИ13'' | Siemens + CCD камера 758 строк | 13'' | 0,45 | 6 | 1,55 | |
ЦД | Perkin Elmer | 512 х 512 точек | 0,44 | 3 | 1,60 | х |
ЦД | Perkin Elmer | 1024 х 1024 точек | 0,44 | 3 | 3,20 | х |
ЦД | Perkin Elmer | 2000 х 2000 точек | 0,22 | 3 | ||
ЦД | Varian | 1408 х 1888 точек 0,127х0,4 | 0,14 | 3 | 6 |
Первым цифровым детектором использованным YXLON для автоматического контроля отливок, были детекторы 512х512 точек фирмы Perkin Elmer. Они применены в кабине для фирмы AMCAST весной 1998.
Пример из практики

В феврале 1998 мы получили от фирмы Dimler-Chrysler заказ на автоматическую систему контроля двух цельнолитных деталей подвески типов W203 R230.
Рисунок 3. Отливка R230. Габаритные размеры 900х400х20мм.
По техническому заданию требовалось распознать дефекты размером 1мм в критических и 2мм в некритических областях. Для уверенности, что время контроля будет выдержано при соблюдении заданных требований фирмой YXLON International X-Ray GmbH летом 1998г. Было проведено соответствующее исследование, результаты которого приведены в таблице 3.
Таблица 3
Число позиций контроля | УИ9'' | УИ13'' | ЦД 512 х 512 | ЦД 1024х1024 |
Nпоз критическое | 34 | 34 | 26 | 17 |
Nпоз некритическое | 66 | 46 | 44 | 29 |
Nпоз суммарное | 98 | 80 | 70 | 46 |
Время контроля сек. | 196 | 160 | 140 | 92 |
Отливок за 24 часа | 440 | 540 | 617 | 939 |
Выяснилось, что число необходимых позиций необходимых при применении цифрового детектора может быть значительно снижено. На стадии запроса Dimler-Chrysler по данному проекту фирмой – конкурентом было предложено применение 13''
усилитель изображения. Определенное при этом число позиций контроля для R230 было примерно 57. Это число в наших исследованиях при соблюдении требований контроля –Chrysler не могло быть подтверждено. Необходимо отметить что мы проводили свои исследования с усилителями изображения имеющими CCD камеру, использующую 8 бит. Указанное фирмой – конкурентом число позиций контроля было получено предположительно при применении усилителя изображения с цифровой камерой. Учитывая уже описанные отрицательные стороны применения усилителя изображения с цифровой камерой, YXLON предложил решение с цифровым детектором.
Фирма Dimler-Chrysler весной 1999г. Выбрала разработку фирмы YXLON и двойную рентгеновскую систему с двумя цифровыми детекторами форматом 512х512 точек. YXLON International реализовала автоматическую систему с 70 позициями контроля для R230 системой ежедневно проверяется 1234 отливки.
Выводы
Цифровые детекторы обладают рядом достоинств:
• очень низким эффектом засвечивания;
• неискаженной картинкой;
• компактной конструкцией;
• высоким коэффициентом преобразования;
• очень высоким коэффициентом сигнал/шум.
К недостаткам цифровых детекторов относится в первую очередь относительно высокая покупная цена. Как следующий недостаток можно назвать отклонения качества внутри каждого класса детекторов, примером которых могут служить более иле менее часто встречающиеся точечные дефекты.
Обобщенно можно утверждать что при применении цифровых детекторов в автоматических системах контроля два требования со стороны литейной промышленности могут быть выполнены. Это высокая чувствительность при распознавании дефектов и сокращенное время контроля.
Эти утверждения результат практического применения цифровых детекторов в более чем 20 рентгеновских системах фирмы YXLON International за последние три года.
Источник - статья N. Parspour опубликованная в журнале « В мире НК » № 4(10) 2010г.
Другие статьи на тему цифровой радиографии можно посмотреть в разделе Статьи.
Источник - статья ВВ. Клюева и Ф.Р. Соснина по материалам XV Международной (Рим, 2000) и 8-й Европейской (Барселона, 2002) конференций по НК опубликованная в журнале « В мире НК » № 4(18) декабрь 2002г.
Поиск новых средств и методов повышения объективности и надежности радиационного контроля был и остается одним из приоритетных направлений развития этого метода НК. Достигнутые в течение 30 последних лет беспрецедентные успехи в электронике и вычислительной технике оказали глубокое воздействие на системы радиационного контроля промышленной продукции и, как следствие, привели к новым возможностям представления количественных характеристик материалов и изделий и к возрастанию роли этих систем для повышения качества промышленной продукции, к появлению полностью автоматизированных систем контроля.
Цифровую технику, используемую во многих системах радиационного контроля, удобно разделить на две основные группы: улучшения изображений и их анализа. И та, и другая являются важными элементами автоматической оценки качества объекта контроля (ОК). Операция по улучшению изображения состоит в том, что входное изображение в результате ее применения преобразуется в улучшенное изображение. При использовании операции анализа изображения входное изображение преобразуется в некоторую совокупность чисел. Эти числа могут быть значениями некоторого набора признаков, характеризующих изображение. Такими признаками могут быть площадь дефекта, его размеры и координаты и т. п.
Методы улучшения изображения связаны с тем, что при выделении информации, заключенной в световом изображении, например, на рентгенограммах, наблюдатель не реагирует на некоторую ее часть (пороговый контраст, различимый глазом, ≈ 0,02 / 0,04) и, следовательно, имеет место некоторая «избыточность» информации на рентгенограмме. Поэтому действительные возможности теневого изображения (в смысле извлечения максимального количества заключенных в нем сведений о просвечиваемом объекте) обычно реализуются не полностью. Поэтому вопросам повышения качества теневого изображения путем его коррекции в настоящее время уделяется достаточно большое внимание. Эффективность корректирующих процедур и их предельные возможности существенно зависят от соотношений между пороговыми характеристиками устройств, формирующих изображение, и характеристиками зрительного аппарата наблюдателя. Анализ докладов показывает, что достаточно высокая эффективность коррекции достигается за счет использования малошумящих средств, формирующих изображение, и низко энергетического рентгеновского излучения.
Поскольку эффективность корректирующих изображение процедур тесно связана с параметрами радиационных преобразователей, ниже в краткой форме рассматриваются и анализируются системы преобразования радиационных изображений и методы, широко используемые в цифровой рентгенотехнике.
Перевод изображения на пленке в цифровую форму
Наиболее важными результатами оцифровки пленочных изображений являются корректировка изображений, количественный анализ и архивирование. Промышленные рентгеновские пленки используются для получения изображений с оптическими плотностями до 4 и иногда до 5. Только некоторые из существующих сканеров способны перекрыть подобный диапазон плотностей. Кроме этого, рентгеновские пленки для НК характеризуются большим отношением сигнал/шум, определяемым стандартами EN 584, ISO 11699, ASTM E 1815-96. Преобразователь в цифровое изображение не только должен быть способен извлекать информацию из снимков с оптическими плотностями 4 или 5, но и не должен увеличивать шум изображения шумом собственного детектора. Он также должен обладать очень высоким пространственным разрешением. Из-за большого диапазона энергии фотонов (50 12000 кэВ), используемых в НК, при разработке требований к переводу изображения в цифровую форму было решено снизить требования по пространственному разрешению до не резкости, создаваемой взаимодействием высокоэнергетического рентгеновского излучения с системой экран-пленка.
Так, преобразователь изображения на пленке в цифровую форму RAD View Film Digitiser может обрабатывать все используемые в настоящее время форматы пленок шириной до 36 см и неограниченной длины с пространственным разрешением от 50 до500 мкм. Пленка размером 36х43 см может быть обработана всего за 7 с.
Исходя из показателей качества изображения на рентгеновских пленках и из характеристик современных систем оцифровки изображений, были предложены три класса качества систем оцифровки (табл. 1 и 2).
Табл. 1. Минимальный диапазон плотностей системы оцифровки радиографических изображений с минимальной чувствительностью по контрасту плотности
Параметры | Класс DS | Класс DB | Класс DA |
Диапазон плотности | 0,5 ÷ 4,5 | 0,5÷4,0 | 0,5 ÷ 3,5 |
Цифровое разрешение, бит | 12 | 10 | 10 |
Чувствительность по контрасту плотности в цифровой радиографии | 0,02 | 0,02 | 0,02 |
Табл. 2. Предлагаемое минимальное пространственное разрешение систем перевода изображения на пленке в цифровую форму: I – размер элемента изображения, мкм; II – пространственная частота при значении МПФ, равного20 %, пар линий/мм*
Энергия, кэВ | Класс DS | Класс DB | Класс DA | |||
I | II | I | II | I | II | |
100 | 15 | 16,7 | 50 | 5 | 70 | 3,6 |
200 | 30 | 8,3 | 70 | 3,6 | 85 | 3 |
450 | 60 | 4,2 | 85 | 3 | 100 | 2,5 |
75Sе, 192Ir | 100 | 2,5 | 125 | 2 | 150 | 1,7 |
60Co | 200 | 1,25 | 250 | 1 | 250 | 1 |
Здесь модуляционной пространственной функцией (МПФ) называют отношение коэффициента модуляции цифрового изображения к коэффициенту модуляции пропускания рентгенограммы в зависимости от пространственной частоты (ПЧ). Наряду с термином МПФ в отечественной литературе для этой же функции употребляют термины: частотно-контрастная характеристика(ЧКХ), частотно-контрастная функция (ЧКФ) и др. Чем выше значение МПФ для данной ПЧ, тем лучше передача контраста какой-либо системой мелких деталей изображения. Значение ПЧ, например, 16,7 пар линий/мм для класса DS и энергии фотонов 100 кэВ означает, что при этой ПЧ значение МПФ равно20 % от ее максимального значения, равного100 %.
Пользователь может выбрать класс систем, исходя из задач оцифровки.
DS – улучшенная система, используемая для перевода изображения в цифровую форму без существенного ухудшения отношения сигнал/шум и пространственного разрешения, область применения: цифровое архивирование пленок.
DB – система, допускающая некоторое ухудшение качества шифровки изображения, область применения: цифровой анализ изображения и архивирование.
DA – основная система, допускающая снижение качества цифрового изображения и ухудшение пространственного разрешения при удовлетворении требований в соответствии со стандартами ISO 5579 и EN 444 при контроле класса А (основной метод).
Каталоги эталонных изображений на рентгенограммах, например, ASTM E155 для отливок из легких сплавов и IIW ISO5817 для сварных швов широко используются для обучения персонала по интерпретации рентгенограмм и для создания шкалы опасностей несплошностей в ОК. Новые детекторы, такие как РЭОП, люминесцентные платы, плоские панели детекторов и т. п., используемые в цифровой рентгенотехнике, во многих случаях заменяют рентгеновскую пленку. В работе сообщается о том, что в ASTM (Американское общество по испытаниям и материалам) образован подкомитет для разработки стандарта на цифровые эталонные каталоги.
Авторы предложили использовать эталонные изображения на рентгенограммах совместно с детекторами цифровых радиационных систем и специальным программным обеспечением, требующим ввода в программы передаточных характеристик детекторов. Новые эталонные изображения необходимы для оценки изображений дефектов цифровыми средствами. Эталонные рентгенограммы должны сканироваться устройством с разрешением 10 мкм или меньше, цифровым разрешением 16 бит и рабочим диапазоном оптических плотностей рентгенограмм от 0,5 до4,5.
Радиоскопические цифровые системы
Главными преимуществами таких систем перед другими системами радиационного контроля являются экспрессность, простота оптимизации геометрии контроля, предпочтительность с точки зрения оцифровки изображений, техники безопасности и стоимости контроля. В этих системах в качестве детекторов используются:
- усилители яркости изображений;
- линейные дискретно-детекторные преобразователи;
- плоские панели детекторов с аморфным селеном (а-Se) и с аморфным кремнием (a-Si);
- флюоресцентные экраны.
Системы с усилителями яркости изображений имеют диаметры входных экранов РЭОП от 40 до 400 мм с предельным разрешением примерно10 пар линий/мм, твердотельную телевизионную камеру, компьютер, манипулятор. Цифровая часть таких систем позволяет улучшить отношение сигнал/шум в элементах выходного изображения путем интегрирования телевизионных кадров и запоминать изображение на жестком диске. По сравнению с обычной радиографией время контроля снижается в 5–7 раз.
Линейные дискретно-детекторные системы имеют разрешение ~ 50 мкм. Формируемое такими системами изображение сварных швов, например, в трубах, улучшено по сравнению с радиографическим изображением как за счет отсечки рассеянного излучения (98 %), так и за счет улучшения геометрии просвечивания (одинаковая локальная радиационная толщина труб).
Плоский матричный детектор с покрытием из аморфного селена в сочетании с тонкопленочными транзисторами преобразует радиационное изображение непосредственно в цифровые сигналы без применения сцинтилляторов и люминофоров. Цифровое14-битовоеизображениеразмером 35 ÷ 43 см может наблюдаться в реальном времени на видео мониторе, передаваться по компьютерной сети, запоминаться и выводиться в виде твердой копии. При этом качество изображения приближается к качеству рентгенограммы на среднезернистой пленке.
Плоские матрицы из аморфного кремния используют сцинтиллятор, состоящий из иодида цезия или оксисульфида гадолиния, который преобразует падающее на него рентгеновское излучение в видимый свет. Световые фотоны преобразуются матрицей из аморфного кремния в электрический сигнал. Прогресс в технологии изготовления таких преобразователей и современное программное обеспечение позволили настолько улучшить отношение сигнал/шум в выходном изображении за счет суммирования по кадрам, что качество выходного изображения приблизилось к изображению, полученному с помощью a-Se матриц. Эти матрицы менее чувствительны к условиям окружающей среды, что позволяет использовать их в полевых условиях. При одиночном снимке быстродействие a-Si матрицы примерно в 4 раза выше, чем a-Sе матрицы.
На рис. 1 представлены функции передачи модуляции (ФПМ) для различных систем получения изображений, а на рис. 2 – эквивалентные чувствительности по пенетрометру EPS (equivalent penetrometer sensitivity) согласно стандарту ASTM E 746:EPS = 100 (Т h/2)1/2/х, %, где Т – толщина пластинчатого пенетрометра; h – диаметр видимого отверстия пенетрометра; x – радиационная толщина ОК. Из рис. 1 видно, что контраст элементов изображения, полученного с использованием a-Se матриц, сравним с контрастом элементов изображения на рентгенограммах примерно до 4 пар линий/мм (около125 мкм), тогда как компьютерная рентгенография с использованием пластин со стимулируемым люминофором достигает высокого контраста при значительно более низкой пространственной частоте.
Характер EPS на рис. 2 дает информацию о том, что чувствительность радиационного контроля с a-Sе может быть сравнима с чувствительностью рентгенографии на среднезернистую пленку, аEPS систем с фотостимулированным фосфором приближается к чувствительности контроля с использованием крупнозернистой пленки.

В докладе сообщается об устройстве и характеристиках плоской панели на основе конвертора из Gd2O2S:Тb, сочлененного с матрицей a-Si фотодиодов и тонкопленочными транзисторами. Размер окна 28Ч 40 см, размер элемента изображения 127 мкм, цифровые уровни серого14 бит, линейность по уровням серого от 40 до400 кВ, динамический диапазон 3500:1 и более, время формирования кадра с его корректировкой 2,6 с, вес 9 кг.
Доклад посвящен техническим характеристикам плоского матричного преобразователя на основе аморфного кремния (a-Si) фирмы General Electric. Вариант DXR-500 с размером элемента изображения 100 мкм при пространственной частоте 5 пар линий/мм имеет значения функции передачи модуляции свыше 20 %. Преобразователь обладает линейной характеристикой в широком диапазоне экспозиций: от менее чем 1 мР, до более чем 60 мР при напряжении на трубке 80 кВ. Шумовая характеристика преобразователя определяется статистикой падающих на него фотонов, что позволяет выполнять эффективное сглаживание по кадру выходного изображения.
Высокоэнергетическая радиоскопия
В докладе сообщается о разработке и характеристиках преобразователя с площадью входного экрана из Gd2O2S:Тb 0,48 м2, размером элемента изображения 0,64 мм, который может использоваться в высокоэнергетической цифровой рентгенотехнике. Пространственное разрешение преобразователя, полученное на линейном ускорителенаэнергию8 МэВ, примерноравно0,5 пар линий/мм, а чувствительность радиационного контроля составляет 2 % при просвечивании 30 см бетона, быстродействие– 9 кадров/с. Схема радиационно-телевизионной установки на основе этого преобразователя представлена на рис. 3. Установка предназначена для контроля ракетных двигателей на твердом топливе, контейнеров.
Стандарты
Стандарты на радиоскопию были разработаны, совершено независимо ASTM (Е1000, Е1411, Е1416, Е1734) и Европейским комитетом по стандартизации (CEN, EN 13068), они сильно отличаются друг от друга, особенно в том, что часть 3 EN 13068 основана на системе классов контроля стандарта EN 444, который гарантирует качество изображения в соответствии с «минимальными требованиями» к процедуре контроля.
Стандарты ASTM чаще описывают метод и качество, в них нет минимальных требований. EN 13068-3 требует выполнения оценок качества изображения двумя индикаторами качества изображения (ИКИ): проволочным (EN 462-1) – для оценок контраста и индикатором с двойными проволочками (EN 462-5, рис. 4 и табл. 3) – для измерения пространственного разрешения.
Табл. 4 определяет минимальные значения размеров проволочек в зависимости от класса контроля (SA или SB) и толщины стенки металлических материалов. Оборудование для проведения радиоскопического контроля согласно EN 13068-3 подразделено на три классаSCI1 – SCI3, которые зависят от задач контроля. Более низкие требования по пространственному разрешению в сравнении с пленочной радиографией (EN 444, ISO 3579) компенсируются ужесточенными требованиями к оценкам контраста элементов.
Табл. 3. Номер элемента ИКИ (I), соответствующая не резкость изображения (II), диаметр проволочек и расстояние между ними (III)
I | II | III | I | II | III |
13D | 0,10 | 0,050 | 6D | 0,50 | 0,250 |
12D | 0,13 | 0,063 | 5D | 0,64 | 0,320 |
11D | 0,16 | 0,080 | 4D | 0,80 | 0,400 |
10D | 0,20 | 0,100 | 3D | 1,00 | 0,500 |
9D | 0,26 | 0,130 | 2D | 1,26 | 0,630 |
8D | 0,32 | 0,160 | 1D | 1,60 | 0,800 |
7D | 0,40 | 0,200 |
Табл. 4. Данные по системе контроля металлических материалов SA и SB
Класс контроля SA | Класс контроля SB | ||||
Класс системы | SC2 | Класс системы | SC3 | ||
Толщина стенки, мм | Диаметр по EN 462-1, мм | Номер элемента ИКИ по EN 462-5 | Толщина стенки, мм | Диаметр по EN 462-1, мм | Номер элемента ИКИ по EN 462-5 |
1,2–2,0 | 0,08 | 11D | < 1,5 | 0,05 | 13D |
2,0–3,5 | 0,10 | 10D | 1,5–2,5 | 0,063 | 12D |
3,5–5,0 | 0,125 | 9D | 2,5–4,0 | 0,08 | 11D |
5,0–7,0 | 0,16 | 8D | 4,0–6,0 | 0,10 | 10D |
7,0–10,0 | 0,20 | 7D | 6,0–8,0 | 0,125 | 9D |
10,0–15,0 | 0,25 | 7D | 8,0–12,0 | 0,16 | 9D |
15,0–25,0 | 0,32 | 7D | 12,0–20,0 | 0,20 | 9D |
25,0–32,0 | 0,40 | 7D | 20,0–30,0 | 0,25 | 9D |
32,0–40,0 | 0,50 | 7D | 30,0–35,0 | 0,32 | 9D |
40,0–55,0 | 0,63 | 7D | 35,0–45,0 | 0,40 | 9D |
55,0–85,0 | 0,8 | 6D | 45,0–65,0 | 0,50 | 9D |
Люминесцентные платы
Компьютерная рентгенография с использованием слоя активированного европием галогенида бария (CR) начала применяться в практике контроля около15 лет назад. Такой фотостимулированный фосфор способен запоминать (накапливать) часть поглощенной в нем энергии рентгеновского излучения, а также под действием света He-Ne лазера испускать люминесцентное излучение, интенсивность которого пропорциональна поглощенной энергии. Фотоны люминесцентного излучения преобразуются в электрический сигнал, кодирующийся для получения цифрового изображения.
Итак, сканирующее устройство RAD View CR Tower фирмы Agfa позволяет получать цифровое изображение с пластин размером 20 ÷ 25 и 35 ÷ 43 см. Пластина в кассете, размещенная во входном устройстве сканера, внутренним механизмом изымается из кассеты и транспортируется в блок сканирования для получения цифрового изображения. Остаточное скрытое изображение на пластине стирается, она перемещается обратно в кассету, готовая к новой экспозиции.
В докладе представлена информация о разработке новой пластины, содержащей игольчатые кристаллы галогенида цезия, активированного излучением. Этот фосфор высвечивается с максимумом излучения на длине волны 440 нм, а стимулируют высвечивание фосфора фотоны инфракрасного излучения с минимумом интенсивности надлиневолны685 нм. Пластины с игольчатой структурой люминофора дают лучшее качество изображения, чем пластины с порошковым слоем, по двум причинам. Первая – кристаллические иглы действуют как световод, вторая – высокая плотность люминофора в пластине увеличивает поглощение рентгеновского излучения. Немецкое общество по НК внесло предложение по стандартизации общих принципов контроля металлических материалов с помощью люминесцентных пластин. Суть предложения состоит в определении минимальных требований к достижению определенного контраста и пространственного разрешения. По аналогии с радиоскопией, для измерений необходимы два индикатора качества изображений – проволочный и индикатор с двойными проволочками. Требования к пространственному разрешению выше, чем в радиоскопии, и подобны требованиям к изображениям, полученным переводом изображений с пленки в цифровую форму (табл. 5–7).
Источник излучения | Толщина стенки | Класс IPA | Класс IPB | ||||||
Размер элемента изображения, мкм |
Номер элемента ИКИ |
Размер элемента изображения, мкм |
Номер элемента ИКИ |
||||||
Рентг. излучение Up ≤ 50 кВ |
W < 4 | 40 | 13 | 30 | 13 | ||||
W ≥ 4 | 60 | 13 | 40 | 13 | |||||
Рентг. излучение 50 < Up≤ 150 кВ |
W < 4 | 60 | 13 | 30 | 13 | ||||
4 ≤ W < 12 | 70 | 12 | 40 | 13 | |||||
W ≥ 12 | 85 | 11 | 60 | 13 | |||||
Рентг. излучение 150 < Up≤ 250 кВ |
W < 4 | 60 | 13 | 30 | 13 | ||||
4 ≤ W < 12 | 70 | 12 | 40 | 13 | |||||
W ≥ 12 | 85 | 11 | 60 | 13 | |||||
Рентг. излучение 250 < Up≤ 350 кВ |
12 ≤ W < 50 | 110 | 10 | 70 | 12 | ||||
W ≥ 50 | 125 | 9 | 110 | 10 | |||||
Рентг. излучение 350 < Up≤ 450 кВ |
W < 50 | 125 | 9 | 85 | 11 | ||||
W ≥ 50 | 160 | 8 | 110 | 10 | |||||
169Yb, 170Tm | 85 | 11 | 60 | 13 | |||||
75Se, 192Ir | W < 40 W ≥ 40 |
160 200 |
8 7 |
110 125 |
10 9 |
||||
60Co | 250 | 6 | 200 | 7 | |||||
Рентг. излучение Up> 1 МэВ |
250 | 6 | 200 | 7 |
Табл. 6. Эквивалентная толщина экрана для пластин с люминофором
Анодное напряжение, кэВ или радионуклид | 100 | 200 | 300 | 400 | 192Ir | 60Co |
Экран для пленки | 27 мкм, свинец | 27 мкм, свинец | 100 мкм, свинец | 100 мкм, свинец | 100 мкм, свинец | 500 мкм, железо |
Экран для пластины с люминофором | 100 мкм, свинец | 100 мкм, свинец | 200 мкм, свинец | 300 мкм, свинец | 350 мкм, свинец | 1 мм, свинец; 0,5 мм, железо |
Табл. 7. Классы систем «пластина с люминофором – сканирующее устройство» в зависимости от минимального отношения сигнал/шум
Класс системы | Минимальное отношение «сигнал/шум» |
IP2 | 110 |
IP3 | 90 |
IP4 | 70 |
IP5 | 60 |
IP6 | 50 |
Компьютерная томография
Компьютерная томография в настоящее время достаточно активно используется в НК. ASTM разработало ряд стандартов для этого метода контроля:
- Е 1570-95а. Контроль с помощью компьютерной томографии;
- Е 1814-96. Контроль отливок с помощью компьютерной томографии; Е 1695-95. Измерение характеристик компьютерно-томографической системы;
- Е 1441-97. Получение компьютерно-томографического изображения;
- Е 1672-95. Выбор компьютерно-томографической системы;
- Е 1935-97. Калибровкаи измерение плотности компьютерно-томографического изображения;
- Е 1931-97. Томография с использованием рентгеновского комптоновского рассеянного излучения.
Методы анализа изображений
В докладе представлен обзор современных систем и методов автоматического анализа теневых изображений при просвечивании алюминиевых отливок для классификации их дефектов с целью разбраковки отливок.
Почти во всех известных системах автоматического распознавания дефектов в алюминиевых отливках придерживаются общей начальной стратегии:
- сегментируют возможные дефектные области теневых изображений;
- создают бездефектное эталонное изображение этих областей;
- строят разностное изображение, вычитая полученное эталонное изображение из исходного.
Хотя известные методы имеют очевидные сходства, они имеют существенные отличия в деталях. Один из вопросов состоит в том, какую предварительную обработку изображений следует выполнить, например, если разностное изображение при неизменном эталонном изображении будет иметь нежелательные артефакты, обусловленные допусками на позиционирование краями отливок или конкретными особенностями различных литейных форм.
Ниже перечислены наиболее важные проблемы, стоящие перед системами автоматического обнаружения дефектов в серийно изготавливаемых отливках:
- обнаружение очень малых дефектов, обладающих незначительным контрастом на рентгеновских снимках;
- обнаружение больших дефектов, имеющих низкую плотность почернения на радиограммах, замаскированных изображением элементов отливок.
Первая проблема связана с размером элемента цифрового изображения, вторая – с размером ядра обрабатывающего изображение фильтра и качеством данных, полученных системой при ее управляемом обучении. Разработанный авторами «обучаемый медианный фильтр (TMF)» устраняет все слабые стороны существующих методов автоматического распознавания дефектов литья по радиационным изображениям. Даже плоские дефекты в областях с насыщенной структурой надежно обнаруживаются. TMF выполняется на персональном компьютере общего назначения в среде Microsoft Windows 2000.
Типичные интервалы времени для современной системы контроля серийной продукции:
• перемещение от одной позиции просвечивания к другой – 0,8 с;
• интегрирование системой одного изображения – 0,5 с;
• цифровая обработка одного изображения – 1,3 с;
• контроль всей отливки, включая тринадцать позиций – 20 с.
В сообщении [9] дана информация о составе системы для автоматического рентгеновского контроля дисков автомобильных колес, процессе контроля и обзор экономических преимуществ таких систем. Упрощенные экономические сравнения системы MU 281 с визуальным контролем дисков по таким параметрам, как:
- стоимость системы автоматического распознавания дефектов с программным обеспечением – 130 тыс. евро;
- амортизация – 8 %;
- обслуживание – 300 евро в месяц;
- стоимость работ по визуальному контролю – 20 евро в час;
- 3 смены в день, 7 дней в неделю показывают, что затраты окупаются в течение одного года.
Вдокладе сообщается о разработке новой механической системы позиционирования объектов контроля при цифровом рентгеновском контроле – карданном манипуляторе, который, в сравнении с традиционными С-манипуляторами и роботизированными системами, повышает точность позиционирования на 20 % и уменьшает вибрации при просвечивании, улучшая тем самым качество изображения.
Выводы
- 15th WCNDT и 8th ECNDT продемонстрировали интеграцию современных технических направлений в рентгеновской технике: использование высокостабильных источников излучений, современных радиационных преобразователей и манипуляторов ОК, компьютерных методов управления ими, и наконец, применение новейших методов цифровой обработки изображений и их анализа.
- Идет интенсивный переход систем контроля с использованием радиационных РЭОП на системы с использованием многоэлементных преобразователей, выпускаемых по технологиям микроэлектроники: с аморфным селеном и аморфным кремнием. Усложняется структура пластин с фотостимулированным фосфором: переход от пластин с порошковым слоем фосфора на пластины с игольчатой структурой люминофора.
- Современные автоматические системы анализа радиационных изображений литых изделий достигли высоких показателей по надежности обнаружения дефектов (около95 %) и производительности (более100 изделий в час).
- Эталонные радиографические снимки являются ценным пособием по расшифровке световых изображений цифровых систем. Рекомендуется иметь собственную библиотеку цифровых изображений.
- В США и Европе идет активное пополнение фонда стандартов по НК новыми стандартами по цифровой рентгенотехнике с использованием стандартизированной терминологии.
Источник - статья ВВ. Клюева и Ф.Р. Соснина по материалам XV Международной (Рим, 2000) и 8-й Европейской (Барселона, 2002) конференций по НК опубликованная в журнале « В мире НК » № 4(18) декабрь 2002г.
Другие статьи на тему цифровой радиографии можно посмотреть в разделе Статьи.
Методы и приборы неразрушающего контроля бетона
Для оценки состояния бетонных конструкций необходим всесторонний анализ факторов, влияющих на их эксплуатационные характеристики, такие как прочность, толщина защитного слоя, диаметр арматуры, теплопроводность, влажность, адгезия покрытий и т.д. Неразрушающие методы контроля особенно актуальны, когда характеристики бетона и арматуры неизвестны, а объёмы контроля значительны. Методы НК дают возможность контроля как в лабораторных условиях, так и на строительных площадках в процессе эксплуатации.
В чём плюсы неразрушающего контроля:
- Возможность не организовывать на площадке лабораторию оценки бетона.
- Сохранение целостности проверяемой конструкции.
- Сохранение эксплуатационных характеристик сооружений.
- Широкая сфера применения.
Лаборатория НТЦ «Эксперт» оказывает услуги по контролю бетона методами УЗК, магнитной индукции и методом упругого отскока. Данные методы дают возможность определять прочность бетона, наличие внутренних дефектов, глубину и диаметр арматуры. Неразрушающие методы применимы, когда нет возможности изъятия образцов для контроля прямыми методами, особенно в процессе строительства и реконструкции. Процедура обследования бетонных конструкций регламентирована ГОСТ 22690-2015 и ГОСТ 17624-2012. Общие правила проверки качества бетона изложены в ГОСТ 18105-2010.
При всем многообразии контролируемых параметров контроль прочности бетона занимает особое место, поскольку при оценке состояния конструкции определяющим фактором является соответствие фактической прочности бетона проектным требованиям.
Процедура обследований регламентирована ГОСТ 22690-2015 и ГОСТ 17624-2012. Общие правила проверки качества бетона изложены в ГОСТ 18105-2010. Неразрушающий контроль прочности бетона подразумевает применение механических методов (удар, отрыв, скол, вдавливание) и ультразвукового сканирования.
Контроль прочности готовых бетонных конструкций как правило проводится по графику, в установленном проектом возрасте, либо при необходимости, например, когда планируется реконструкция. Контроль прочности строящихся конструкций даёт возможность оценить распалубочную и отпускную прочность, сравнить реальные характеристики материала с паспортными.
Методы неразрушающего контроля прочности бетона делят на две группы
Прямые (методы местных разрушений) | Косвенные |
|
|
Прямые методы испытания бетона (методы местных разрушений)
Методы местных разрушений относят к неразрушающим условно. Их основное преимущество – достоверность. Они дают настолько точные результаты, что их используют для составления градуировочных зависимостей для косвенных методов. Испытания проводятся по ГОСТ 22690-2015.
Метод | Описание | Плюсы | Минусы |
Метод отрыва со скалыванием | Оценка усилия, которое требуется, чтобы разрушить бетон, вырывая из него анкер (видео). | - Высокая точность. - Наличие общепринятых градуировочных зависимостей, зафиксированных ГОСТом. |
- Трудоёмкость. - Невозможность использовать в оценке прочности густоармированных сооружений, сооружений с тонкими стенами. |
Скалывание ребра | Измерение усилия, которое требуется, чтобы сколоть бетон на углу конструкции. Метод применяется для исследования прочности линейных сооружений: свай, колонн квадратного сечения, опорных балок. | - Простота использования. - Отсутствие предварительной подготовки. |
- Не применим, если слой бетона меньше 2 см или существенно повреждён. |
Отрыв дисков | Регистрация усилия для разрушения бетона при отрыве от него металлического диска. Способ широко использовался в советское время, сейчас почти не применяется из-за ограничений по температурному режиму. | - Подходит для проверки прочности густоармированных конструкций. - Не такой трудоёмкий, как отрыв со скалыванием. |
- Необходимость подготовки: диски нужно наклеить на бетонную поверхность за 3-24 часа до проверки. |
Основные недостатки методов местных разрушений – высокая трудоёмкость, необходимость расчёта глубины прохождения арматуры, её оси. При испытаниях частично повреждается поверхность конструкций, что может повлиять на их эксплуатационные характеристики.
Косвенные методы испытания бетона
В отличие от методов местных разрушений, методы, основанные на ударно-импульсном воздействии на бетон, имеют большую производительность. Однако, контроль прочности бетона ведется в поверхностном слое толщиной 25-30 мм, что ограничивает их применение. В упомянутых случаях необходима зачистка поверхности контролируемых участков бетона или удаление поврежденного поверхностного слоя.
Неразрушающий контроль прочности бетона на заводах ЖБИ и в строительных лабораториях осуществляется после приведения градуировочных зависимостей приборов в соответствие с фактической прочностью бетона по результатам испытания контрольных партий в прессе.
Метод | Описание | Плюсы | Минусы |
Ударного импульса | Регистрация энергии, которая появляется при ударе специального бойка. Для обследований используется молоток Шмидта. Как работает молоток Шмидта |
- Компактное оборудование. - Простота. - Возможность одновременно устанавливать класс бетона. |
- Относительно невысокая точность |
Упругого отскока | Измерение пути бойка при ударе о бетон. Для обследования используют склерометр Шмидта и аналогичные устройства. | - Простота и скорость исследования. | - Жёсткие требования к процедуре подготовки контрольных участков. - Техника требует частой поверки. |
Пластической деформации | Измерение отпечатка, оставшегося на бетоне при ударе металлическим шариком. Метод устаревший, но используется часто. Для оценки применяют молоток Кашкарова и аппараты статического давления. Оценка прочности бетона молотком Кашкарова. |
- Доступность оборудования. - Простота. |
- Невысокая точность результатов. |
Ультразвуковой метод | Измерение скорости колебаний ультразвука, проходящего сквозь бетон. | - Возможность проводить массовые изыскания неограниченное число раз. - Невысокая стоимость исследований. - Возможность оценить прочность глубинных слоёв конструкции. |
- Повышенные требования к качеству поверхности. - Требуется высокая квалификация сотрудника. |
Метод ударного импульса
Метод ударного импульса – самый распространённый среди неразрушающих методов из-за простоты измерений. Он позволяет определять класс бетона, производить измерения под разными углами к поверхности, учитывать пластичность и упругость бетона.
Суть метода. Боёк со сферическим ударником под действием пружины ударяется о поверхность. Энергия удара расходуется на деформации бетона. В результате пластических деформаций образуется лунка, в результате упругих возникает реактивная сила. Электромеханический преобразователь превращает механическую энергию удара в электрический импульс. Результаты выдаются в единицах измерения прочности на сжатие.
К достоинствам метода относят оперативность, низкие трудозатраты, отсутствие сложных вычислений, слабую зависимость от состава бетона. Недостатком считается определение прочности в слое глубиной до 50 мм.
Метод упругого отскока
Метод упругого отскока заимствован из практики определения твёрдости металла. Для испытаний применяют склерометры – пружинные молотки со сферическими штампами. Система пружин допускает свободный отскок после удара. Шкала со стрелкой фиксирует путь ударника при отскоке. Прочность бетона определяют по градуировочным кривым, которые учитывают положение молотка, так как величина отскока зависит от его направления. Среднюю величину вычисляют по данным 5-10 измерений, выполненных на определённом участке. Расстояние между местами ударов – от 30 мм.
Диапазон измерений методом упругого отскока – 5-50 МПа. К достоинствам метода относят простоту и скорость измерений, возможность оценки прочности густоармированных конструкций. Ключевые недостатки такие же, как у других ударных методов: контроль прочности в поверхностном слое (глубина 20-30 мм), необходимость частых поверок (каждые 500 ударов), построение градуировочных зависимостей.
Ниже представлены измерители прочности бетона, работающие по принципу ударного импульса, из ассортимента нашей компании
![]() |
![]() |
![]() |
![]() |
Молоток Шмидта ORIGINAL SCHMIDT | Молоток Шмидта SILVER SCHMIDT | Молоток Шмидта Original Schmidt Live | Измерители прочности бетона ИПС-МГ4 |
Метод пластической деформации
Метод пластической деформации считается одним из самых дешёвых. Его суть – в определении твёрдости поверхности посредством измерения следа, который оставляет стальной шарик/стержень, встроенный в молоток. При проведении испытаний молоток располагают перпендикулярно поверхности бетона и совершают несколько ударов. С помощью углового масштаба измеряют отпечатки на бойке и бетоне. Для облегчения измерений диаметров используют листы копировальной или белой бумаги. Полученные характеристики фиксируют и вычисляют среднее значение. Бетонная прочность определяется по соотношению размеров отпечатков.
Принцип действия приборов для испытаний методом пластических деформаций основан на вдавливании штампа при помощи удара либо статического давления. Устройства статических давлений применяются ограниченно, более распространены приборы ударного действия – ручные и пружинные молотки, маятниковые устройства с шариковым/дисковым штампом. Твёрдость стали штампов минимум HRC60, диаметр шарика — минимум 10 мм, толщина диска — не меньше 1 мм. Энергия удара должна быть равна или больше 125 H.
Метод прост, может применяться в густоармированных конструкциях, отличается быстротой, но подходит для оценки прочности бетона не больше М500.
Ультразвуковое обследование
Ультразвуковой метод – это регистрация скорости прохождения ультразвуковых волн. По технике проведения испытаний можно выделить сквозное ультразвуковых прозвучивание, когда датчики располагают с разных сторон тестируемого образца, и поверхностное прозвучивание, когда датчики расположены с одной стороны. Сквозной метод позволяет, в отличие от всех остальных методов НК прочности, контролировать прочность в приповерхностных и глубоких слоях конструкции.
Ультразвуковые приборы неразрушающего контроля бетона могут использоваться не только для контроля прочности бетона, но и для дефектоскопии, контроля качества бетонирования, определения глубины и поиска арматуры в бетоне. Они позволяют многократно проводить массовые испытания изделий любой формы, вести непрерывный контроль нарастания или снижения прочности.
На зависимость «прочность бетона – скорость ультразвука» влияют количество и состав заполнителя, расход цемента, способ приготовления бетонной смеси, степень уплотнения бетона. Недостатком метода считается довольно большая погрешность при переходе от акустических характеристик к прочностным.
Ниже даны ссылки на приборы неразрушающего контроля бетона, представленные в ассортименте нашей компании
Кроме перечисленных способов контроля прочности существуют менее распространённые. На стадии экспериментального использования метод электрического потенциала, инфракрасные, вибрационные, акустические методы.
Опыт ведущих специалистов по неразрушающему контролю прочности бетона показывает, что в базовый комплект специалистов, занятых обследованием, должны входить приборы, основанные на разных методах контроля: отрыв со скалыванием (скалывание ребра), ударный импульс (упругий отскок, пластическая деформация), ультразвук, а также измерители защитного слоя и влажности бетона, оборудование для отбора образцов.
Погрешность методов неразрушающего контроля прочности бетона
№ | Наименование метода | Диапазон применения*, МПа | Погрешность измерения** |
1 | Пластическая деформация | 5 ... 50 | ± 30 ... 40% |
2 | Упругий отскок | 5 ... 50 | ± 50% |
3 | Ударный импульс | 10 ... 70 | ± 50% |
4 | Отрыв | 5 ... 60 | нет данных |
5 | Отрыв со скалыванием | 5 ... 100 | нет данных |
6 | Скалывание ребра | 10 ... 70 | нет данных |
7 | Ультразвуковой | 10 ... 40 | ± 30 ... 50% |
* по ГОСТ 17624 и ГОСТ 22690; ** источник: Джонс Р., Фэкэоару И. Неразрушающие методы испытаний бетонов. М., Стройиздат, 1974. 292 с. |
Процедура оценки
Общие правила контроля прочности бетона изложены в ГОСТ 18105-2010. Требования к контрольным участкам приведены в следующей таблице
Метод | Общее число измерений на участке | Минимальное расстояние между местами измерений на участке, мм | Минимальное расстояние от края конструкции до места измерения, мм | Минимальная толщина конструкции, мм |
Упругий отскок | 9 | 30 | 50 | 100 |
Ударный импульс | 10 | 15 | 50 | 50 |
Пластическая деформация | 5 | 30 | 50 | 70 |
Скалывание ребра | 2 | 200 | -0 | 170 |
Отрыв | 1 | 2 диаметра диска | 50 | 50 |
Отрыв со скалыванием при рабочей глубине заделки анкера: 40 мм < 40 мм |
1 2 |
5h |
150 |
2h |
Наиболее сложными для контроля бетонных конструкций являются случаи воздействия на них агрессивных факторов: химических (соли, кислоты, масла), термических (высокие температуры, замораживание в раннем возрасте, переменное замораживание и оттаивание), атмосферных (карбонизация поверхностного слоя). При обследовании необходимо визуально, простукиванием, либо смачиванием раствором фенолфталеина (случаи карбонизации бетона), выявить поверхностный слой с нарушенной структурой. Подготовка бетона таких конструкций для испытаний неразрушающими методами заключается в удалении поверхностного слоя на участке контроля и зачистке поверхности наждачным камнем. Прочность бетона в этих случаях необходимо определять преимущественно методами местных разрушений или путём отбора образцов. При использовании ударно-импульсных и ультразвуковых приборов шероховатость поверхности не должна превышать Ra 25.
Прочность бетона по маркам
Класс бетона (В) по прочности на сжатие | Ближайшая марка бетона (М) по прочности на сжатие | Средняя прочность бетона данного класса кгс/см² | Отклонения ближайшей марки бетона от средней прочности бетона этого класса,% |
В3,5 | М50 | 45,84 | +9,1 |
В5 | М75 | 65,48 | +14,5 |
В7,5 | М100 | 98,23 | +1,8 |
В10 | М150 | 130,97 | +14,5 |
В12,5 | М150 | 163,71 | -8,4 |
В15 | М200 | 196,45 | +1,8 |
В20 | М250 | 261,94 | -4,6 |
В22,5 | М300 | 294,68 | +1,8 |
В25 | М350 | 327,42 | +6,9 |
В27,5 | М350 | 360,16 | -2,8 |
В30 | М400 | 392,90 | +1,8 |
В35 | М450 | 458,39 | -1,8 |
В40 | М500 | 523,87 | -4,6 |
В45 | М600 | 589 | |
В50 | М650 | 655 | |
В55 | М700 | 720 | |
В60 | М800 | 786 |
Измерение защитного слоя и диаметра арматуры
Основная задача защитного слоя – обеспечить надежное сцепление бетона с арматурой на этапах монтажа и эксплуатации бетонной конструкции. Кроме того, он выполняет функцию защиты от перепадов температур, повышенной влажности, агрессивных химических реагентов. Толщина защитного слоя бетона диктуется условиями эксплуатации конструкции, видом и диаметром используемой арматуры.
При создании защитного слоя бетона руководствуются указаниями СНиП 2.03.04-84 и СП 52-101-2003. Контроль толщины защитного слоя проводится по ГОСТ 22904-93.
Для оперативного контроля качества армирования железобетонных конструкций и определения толщины защитного бетонного слоя используют приборы для поиска арматуры в бетоне - локаторы арматуры. Они работают по принципу импульсной магнитной индукции. Помимо измерения толщины защитного слоя, измеритель способен поиск арматуры в бетоне и определять наличие арматуры на определенном участке, фиксировать сечение, диаметр и другие параметры арматурных включений.
Оборудование для измерения толщины защитного слоя и оценки расположения арматуры
![]() |
![]() |
![]() |
![]() |
![]() |
![]() |
Локатор арматуры Profoscope | Локатор арматуры Profometer PM-600 | Локатор арматуры Proceq GPR Live | Анализатор коррозии Canin+ | Измеритель защитного слоя бетона ИПА-МГ4 | Прибор диагностики свай ПДС-МГ4 |
Неразрушающий контроль влажности
Влажность бетона оценивают по ГОСТ 12730.0-78: Бетоны. Общие требования к методам определения плотности, влажности, водопоглощения, пористости и водонепроницаемости. Некоторое количество влаги (в ячеистом бетоне до 30–35%) остаётся в стройматериалах в ходе производственного процесса (технологическая влага). В нормальных условиях содержание влаги в бетонных конструкциях в течение первого отопительного периода сокращается до 4-6% по весу.
Для получения полной картины целесообразно использовать несколько различных по физическому принципу методов оценки. Для измерения влажности бетона применяют влагомеры или измерители влажности. Принцип действия влагомера основан на зависимости диэлектрической проницаемости материала и содержания в нем влаги. Следует учитывать, что содержание влаги в бетоне отличается от ее содержания на поверхности. Методы измерения на поверхности дают результат для глубины до 20 мм и не всегда отражают реальное положение вещей.
Оборудование для измерения влажности и проницаемости бетона
![]() |
![]() |
![]() |
![]() |
Измеритель влажности бетона Hygropin | Тестер проницаемости бетона Torrent | Измеритель влажности бетона МГ4Б | Измеритель влажности бетона МГ4БМ |
Адгезия защитных и облицовочных покрытий
Адгезия измеряется при помощи прямых (с нарушением адгезионного контакта), неразрушающих (с измерением ультразвуковых или электоромагнитных волн) и косвенных (характеризующих адгезию лишь в сопоставимых условиях) методов. Наиболее распространен метод оценки с помощью адгезиметра. Методика оценки установлена ГОСТ 28574-2014: Защита от коррозии в строительстве. Конструкции бетонные и железобетонные. Методы испытаний адгезии защитных покрытий.
Оценка бетона с помощью адгезиметра проводится при диагностике повреждений покрытия, контроле качества антикоррозийных работ, а также при проверке качества строительных материалов. Интенсивность адгезии определяется давлением отрыва, которое следует приложить к покрытию (штукатурке, краске, герметику и т.д.), чтобы отделить его от бетонной основы.
Оборудование для измерения адгезии
![]() |
![]() |
Измеритель адгезии DY-2 | Измеритель адгезии ПСО-ХМГ4 |
Морозостойкость
В большинстве нормативных документов устойчивость покрытий и изделий из застывшей смеси определяется количеством переходов через нулевую отметку, после которого начинается падение эксплуатационных характеристик. Морозостойкость бетона – способность выдерживать температурные перепады, а также количество циклов заморозки и оттаивания бетонной смеси. В ГОСТ 10060-2012 выделяют 11 марок бетона с различной морозостойкостью, которая имеет градацию на циклы от F50 до F1000.
Группы бетонов по морозостойкости
Группа морозостойкости | Обозначение | Примечание |
Низкая | менее F50 | Не находит широкого использования |
Умеренная | F50 – F150 | Морозостойкость и водонепроницаемость бетона этой группы имеет оптимальные показатели. Такие смеси встречаются наиболее часто. |
Повышенная | F150 – F300 | Морозостойкость бетонной смеси в этом диапазоне дает возможность эксплуатировать здания в достаточно суровых условиях. |
Высокая | F300 – F500 | Такие растворы требуются в особых случаях, например, при эксплуатации с переменным уровнем влаги. |
Особо высокая | более F500 | Бетон морозостойкий получается впрыскиванием особых добавок. Применяется при сооружении конструкций на века. |
Дополнительная информация
- Методы неразрушающего контроля прочности бетона
- Определение прочности бетона с использованием молотка Шмидта (по DIN EN 12504-2: 2001-12)
- Определение прочности бетона на отрыв адгезии нанесённых на бетон покрытий
- Трещины в бетоне (по DIN 1045-1: 2008). Наблюдение за трещиной и определение ширины раскрытия трещины в бетоне
- Способы измерения твёрдости металла, резины, бетона
Морозостойкость бетона оценивают ультразвуковыми методами по ГОСТ 26134-2016. Ультразвуковая диагностика отличается невысокой стоимостью, даёт возможность проводить обследования неограниченное число раз. При этом предъявляются высокие требования к качеству бетонной поверхности и квалификации сотрудника.
Подробную консультацию по контролю бетонных сооружений вы можете получить у наших специалистов по телефонам +7 (495) 972-88-55, +7 (495) 660-49-68.
Смотрите так же разделы: Дефектоскопы для бетона, Услуги по неразрушающему контролю бетона, Определение прочности бетона, Приборы для поиска арматуры, Обучение и аттестация специалистов по УЗК.
Оборудование для неразрушающего контроля бетона можно купить с доставкой до двери либо до терминалов транспортной компании в городах: Москва, Санкт-Петербург, Екатеринбург, Саратов. Амурск, Ангарск, Архангельск, Астрахань, Барнаул, Белгород, Бийск, Брянск, Воронеж, Великий Новгород, Владивосток, Владикавказ, Владимир, Волгоград, Волгодонск, Вологда, Иваново, Ижевск, Йошкар-Ола, Казань, Калининград, Калуга, Кемерово, Киров, Кострома, Краснодар, Красноярск, Курск, Липецк, Магадан, Магнитогорск, Мурманск, Муром, Набережные Челны, Нальчик, Новокузнецк, Нарьян-Мар, Новороссийск, Новосибирск, Нефтекамск, Нефтеюганск, Новочеркасск, Нижнекамск, Норильск, Нижний Новгород, Обнинск, Омск, Орёл, Оренбург, Оха, Пенза, Пермь, Петрозаводск, Петропавловск-Камчатский, Псков, Ржев, Ростов, Рязань, Самара, Саранск, Смоленск, Сочи, Сыктывкар, Таганрог, Тамбов, Тверь, Тобольск, Тольятти, Томск, Тула, Тюмень, Ульяновск, Уфа, Ханты-Мансийск, Чебоксары, Челябинск, Череповец, Элиста, Ярославль и другие города. А так же Республики Казахстан, Белоруссия и другие страны СНГ.